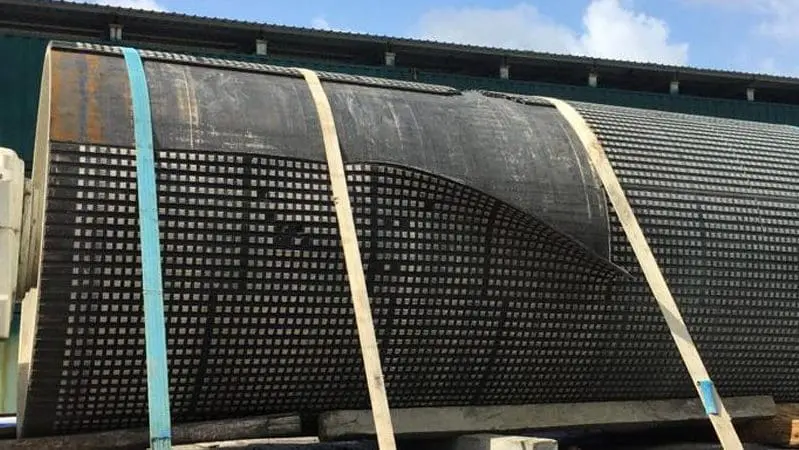
Consequences of Catastrophic Failure with Cold Bonded Lagging for New Mining Projects

Catastrophic lagging failure due to debonding occurred within two weeks of installation and operation of the pulley, resulting in a shutdown of production, and necessitated a replacement of the pulley. Within only two weeks of service, this ceramic lagging was already experiencing loss of the ceramic tiles.
The second pulley put into service as a replacement also suffered the same catastrophic lagging debonding, and resulted in a second plant shutdown. At this point, the conveyor component manufacturer PROK was contacted by the customer to evaluate and provide a solution to the failure. The pulleys in question were cold bond lagged and provided by another well-known pulley manufacturer.
PROK engaged partner supplier Elastotec to work on a solution. Our recommendation was for both new and refurbished pulleys to be applied with hot vulcanised lagging. The reason for this is that the 100% rubber tear bond achieved with a hot vulcanised lagging application, eliminates any chance of lagging failure due to debonding. In this instance, due to time pressure to restart the plant, and the lead time required to ship the pulleys for hot vulcanising, this was not an option, and the Elastotec cold bonded lagging and adhesive system was chosen.
In addition to the catastrophic debonding and the tile loss after only two weeks service, a fundamental flaw in application technique was observed in a circumferential join in the lagging (see photo below).



Elastotec ceramic lagging being applied on conveyor with Elastotec supervision and training.
These pulleys have a 3600 mm face width and the original applicators have chosen to cut and join shorter strips to cover the 3600 mm pulley. This places a weak point midway across the pulley and greatly increases the risk of a lagging failure. Strip pulley lagging must always be applied as strips that cover the full pulley face width in a single piece.
Elastotec supported PROK to urgently manufacture the 3800 mm long ceramic lagging strips for the four pulleys and had this shipped, with the Elastotec cold bonding system, by airfreight to the mine site. An Elastotec applications engineer was sent to the site to assist with training, and supervision of the lagging application – duplicate adhesion tests were carried out on each pulley lagged, and the results were above the Elastotec requirement of a minimum of 12N/mm. The pulleys are back online and are operating satisfactorily.
The limitations of cold bonded lagging are well documented and result from moderate adhesion strength under the best of conditions and variability in application techniques and applicator knowledge.
While you could argue that the fact that as these pulleys are now operating satisfactorily with Elastotec cold bonded lagging, there is no need for hot vulcanised lagging, this ignores how dependent cold bonding is on all parts of the process being done correctly – there is little margin for error.
The hot vulcanised application process is robust and has much less variability when compared to cold bonded lagging application. For these reasons, PROK and Elastotec recommend hot vulcanised (HV) application of lagging (rubber, ceramic or polyurethane) for all new pulleys and pulleys being refurbished. The adhesion to the pulley always provides 100% rubber tear bonds and bond strengths >20N/mm, roughly double the adhesion strength achieved with cold bonded lagging – we test adhesion on every HV pulley application to ensure the correct outcome.
For the Elastotec Hot Vulcanised lagging system we provide a written guarantee:
- No lagging debonding from the pulley shell and
- No tile loss due to debonding.
For new projects why take the risk with cold bonded lagging?
Download Case Study
Large Gold Mine in Australia – increased service life of pulleys with Elastotec/PROK HVCL
One of the largest gold mines in Australia, located in southeast of Perth, produces around 750,000 o
T&T Perú 2023
Thank you to the Peruvian mining sector. Thank you for the space to discuss your challenges. Thank y
Prevention of blisters in steam heated autoclaves
This technical bulletin will outline the causes of blister formation and will detail a series of sim