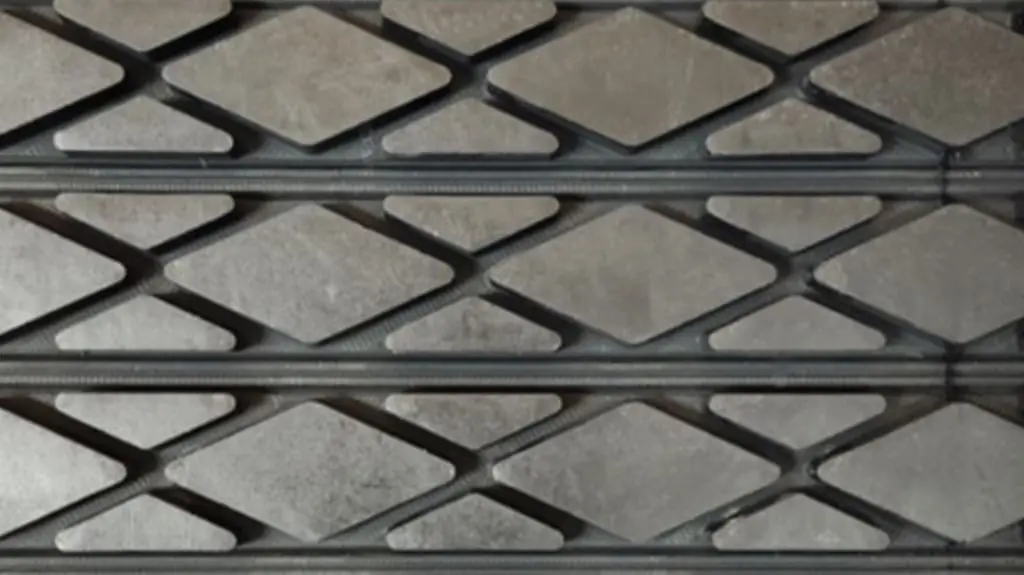
Reibung ist nicht gleich Reibung
Dieser Artikel erschien ursprünglich in der März/April-Ausgabe des Australische Überprüfung der Massengutabfertigung.
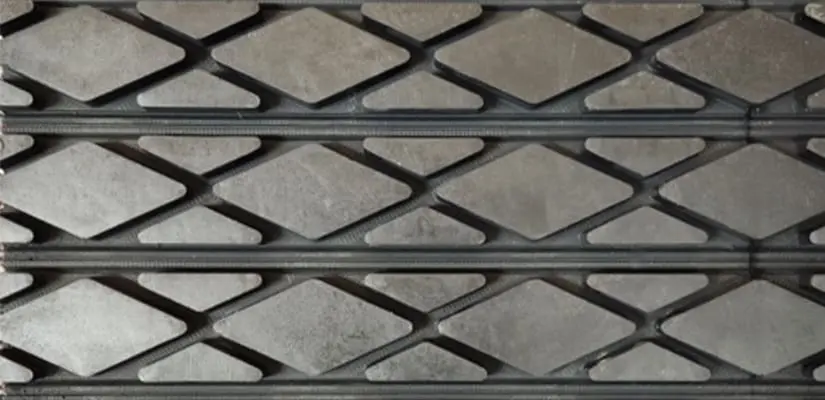
Experten von Elastotec und der University of Newcastle erklären, warum es für die Optimierung von Design, Leistung, Effizienz und Sicherheit von Fördersystemen so wichtig ist, den Reibungskoeffizienten zwischen der Riemenscheibe und dem Riemen zu kennen.
Der Reibungskoeffizient zwischen der Riemenscheibenbeschichtung und dem Riemen ist ein entscheidender Parameter bei der Förderbandkonstruktion, der den Halt des Riemens auf der Riemenscheibe und seine Fähigkeit zur Drehmomentübertragung bestimmt.
Ein höherer Reibungskoeffizient sorgt für besseren Halt und ermöglicht den Betrieb des Förderers mit höheren Lasten, weniger Schlupf und höherer Effizienz, während ein niedrigerer Reibungskoeffizient zu Schlupf und Leistungsverlust führen kann. Derzeit verwenden Fördererkonstrukteure allgemeine Reibungskoeffizienten, die in Konstruktionsnormen (CEMA, ISO5048, DIN22101) festgelegt sind. Diese Werte sind vergleichsweise niedriger als herkömmliche Werte und werden pauschal auf Beläge unterschiedlicher Konstruktion und Herkunft angewendet. Dies führt zu einem konservativen Fördererdesign, das höhere Bandspannungen, überdimensionierte Bandleistungen, größere Fördererstrukturen und geringere Effizienz zur Folge hat.
Derzeit verwenden Förderanlagenkonstrukteure generische Reibungskoeffizienten, die in Konstruktionsnormen (CEMA, ISO5048, DIN22101) festgelegt sind. Diese Werte sind vergleichsweise niedriger als herkömmliche Werte und werden pauschal auf Beläge unterschiedlicher Konstruktion und Herkunft angewendet. Dies führt zu einer konservativen Förderanlagenkonstruktion, die höhere Bandspannungen, überdimensionierte Bandleistung, größere Förderanlagenstrukturen und eine geringere Effizienz zur Folge hat.
Da immer mehr Förderbänder auf den Markt kommen, die größer und leistungsstärker werden, bedarf es eines besseren Verständnisses des Verhaltens der Reibungselemente unter realen Bedingungen, um effizientere Konstruktionen entwickeln zu können.
Aus mehreren Gründen ist es wichtig, den Reibungskoeffizienten zwischen Riemenscheibenbelag und Band bei der Konstruktion von Förderanlagen zu kennen:
- Designoptimierung: Der Reibungskoeffizient zwischen der Riemenscheibenbeschichtung und dem Riemen beeinflusst das Drehmoment und den Leistungsbedarf des Fördersystems, was für die Optimierung des Förderdesigns entscheidend ist. Ein besseres Verständnis des Reibungskoeffizienten ermöglicht es den Förderdesignern, den richtigen Riemenscheibenbelag und das richtige Bandmaterial auszuwählen und den Leistungsbedarf des Fördersystems genau zu berechnen.
- Verbesserte Leistung: Der Reibungskoeffizient zwischen der Trommelbeläge und dem Band beeinflusst auch die Leistung und Effizienz des Fördersystems. Ein besseres Verständnis des Reibungskoeffizienten ermöglicht es den Konstrukteuren von Förderanlagen, den richtigen Trommelbelag auszuwählen, der die Belastung von Band und Infrastruktur minimiert.
- Kosteneinsparungen: Durch die Optimierung der Konstruktion und Leistung des Fördersystems kann ein besseres Verständnis des Reibungskoeffizienten zu erheblichen Kosteneinsparungen führen, indem der Wartungsbedarf verringert, die Größe der Antriebskomponenten reduziert und die Gesamteffizienz des Fördersystems verbessert wird. Dies entspricht weniger Ausfallzeiten.
- Erhöhte Sicherheit: Ein besseres Verständnis des Reibungskoeffizienten kann auch die Sicherheit erhöhen, indem es das Risiko eines Schlupfs oder Bandversagens verringert, das zu Schäden am Fördersystem oder Verletzungen der Arbeiter führen kann.
Im Gegensatz zum klassischen Reibungsverhalten ermöglicht die viskoelastische Natur des Gummibands und/oder der Gummiummantelung, dass es sich unter Belastung verformt und zurückbildet. Dies führt zu einem dynamischen Reibungsverhalten, wobei der Koeffizient auf Änderungen des normalen (Oberflächen-)Drucks, der Gleitgeschwindigkeit, der Gleitzeit und der Temperatur reagiert. Das resultierende Reibungsverhalten ist komplex, sodass ein pauschaler oder allgemeingültiger Ansatz beim Design nicht möglich ist. Die Conveyor Equipment Manufacturers Association (CEMA), ein primärer Förderbanddesignstandard, gibt die Reibungskoeffizienten für das Förderbanddesign basierend auf den Ergebnissen von Labortests und Feldbeobachtungen an. Die von der CEMA bereitgestellten Reibungskoeffizienten sollen als allgemeine Referenz für Förderbanddesigner verwendet werden, sind jedoch möglicherweise nicht in allen Fällen anwendbar. Beispielsweise wird für unterschiedliche Verschmutzungsgrade ein unterschiedlicher Reibungskoeffizient angegeben, es werden jedoch keine Informationen zu Änderungen der Bandspannung (Oberflächendruck), der Gleitgeschwindigkeit oder der Temperatur bereitgestellt. Die Standardwerte sind in Abbildung 1 dargestellt.
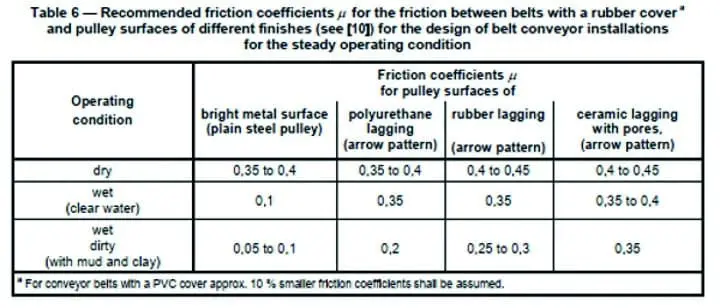
Elastotec hat mit der University of Newcastle zusammengearbeitet, um das Reibungsverhalten zwischen Riemenscheibenbelag und Riemenabdeckung besser zu verstehen und die Abhängigkeit von Schlupfgeschwindigkeit, Flächendruck und Temperatur zu ermitteln.
Prüfmittel und Prüfverfahren
Die University of Newcastle und TUNRA Bulk Solids haben einen Reibungsprüfstand für Beläge entworfen und gebaut (Abbildung 2). Das System besteht aus zwei gegenüberliegenden U-förmigen Abschnitten, die von linearen Schienen getragen werden, wobei an jeder Seite Beläge angebracht sind. In einer Ultimate Testing Machine (Shimadzu Autograph 50 kN) installierte Förderbandproben werden mit dem oberen Querhaupt mit einer Stahlplattenrückseite verbunden, so dass die untere Abdeckung nach außen zur Belagplatte zeigt. Das Band wird oben an der Zugplatte festgeklemmt, damit es sich dehnen kann und die Wechselwirkung zwischen Band und Riemenscheibe besser simuliert werden kann. Das System kann Riemenscheibenbelagproben bis zu 300 mm x 300 mm und jede beliebige Kombination aus Band und Belag mit einer Dicke von bis zu 80 mm auf jeder Seite testen.
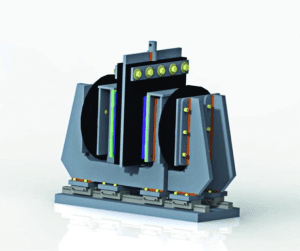
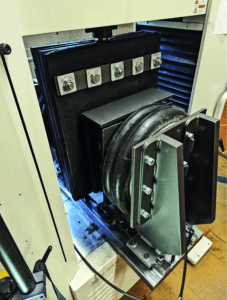
Um einen Test durchzuführen, wird über pneumatische Bälge konstanter Flächendruck auf den Kontakt zwischen Belag und Riemen ausgeübt. Das Vorhandensein von Bälgen auf beiden Seiten der Probe ermöglicht das Testen höherer Flächendrücke und erleichtert ein „selbstzentrierendes“ Design, falls während des Tests eine Kompression des Riemens oder der Proben auftreten sollte. Der obere Querträger wird auf die angegebene Schlupfgeschwindigkeit eingestellt und die resultierende Reibungskraft gemessen. Dies wird anschließend bei unterschiedlichen Flächendrücken, Geschwindigkeiten und in den folgenden Monaten bei unterschiedlichen Temperaturen wiederholt.
Erste Tests der Reibungsabhängigkeit von der Geschwindigkeit
Es wurden vorläufige Tests an mehreren Riemenscheibenbelägen durchgeführt, um zu verstehen, wie sich Änderungen des Normaldrucks und der Geschwindigkeit auf den Reibungskoeffizienten auswirken. Die Tests wurden an Diamant-Naturkautschuk und direkt gebundener Keramik (siehe Abbildung 3) bei verschiedenen Geschwindigkeiten (0.05 mm/s – 10 mm/s) und Flächendrücken (300 kPa – 1200 kPa) durchgeführt. Die Ergebnisse sind in den Oberflächendiagrammen unten dargestellt. Die Testtemperatur betrug ungefähr 23 °C. Diese Bereiche umfassen die in typischen Anwendungen erwarteten. Die Beläge stellen tatsächlich in der Industrie verwendete Materialien und Profile dar, wobei jedes ein einzigartiges Profildesign aufweist.
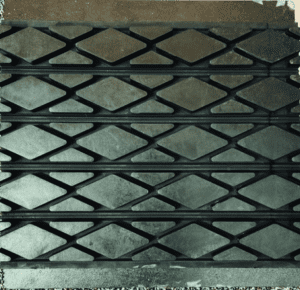
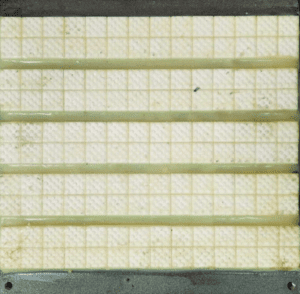
Es wird darauf hingewiesen, dass die unten dargestellten Ergebnisse einen Reibungskoeffizienten darstellen, der mit dem Isolierprofil in Zusammenhang steht, und anders wären, wenn die identischen Materialien mit einer flachen Oberfläche getestet würden.
Belag aus Naturkautschuk
Das Oberflächen- und Konturdiagramm in Abbildung 4 veranschaulicht, wie sich der Reibungskoeffizient über den Bereich der Flächendrücke und Geschwindigkeiten ändert. Wie man sieht, entsprechen höhere Flächendrücke einem niedrigeren Reibungskoeffizienten, ebenso wie eine niedrigere Gleitgeschwindigkeit. Die Geschwindigkeits- und Lastabhängigkeit führt zu einem sich ändernden Reibungskoeffizienten von weniger als 0.3 bis über 1.0.
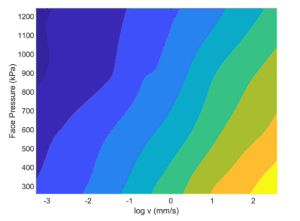
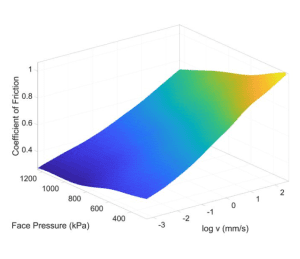
Direktverbundene Keramikummantelung
Die Ergebnisse des Tests mit direkt gebundener Keramik zeigten ein ähnliches Verhalten, wobei die Abhängigkeit vom Flächendruck etwas geringer war als bei den anderen getesteten Belägen. Dies ist wahrscheinlich auf die starre Natur des Belags zurückzuführen, im Vergleich zur viskoelastischen Natur des Gummibelags. Bei diesen Ergebnissen änderte sich der Reibungskoeffizient von ungefähr 0.3 auf fast 1.0.
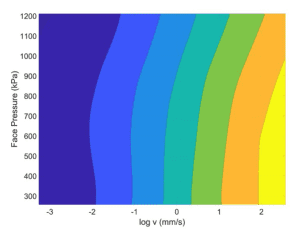
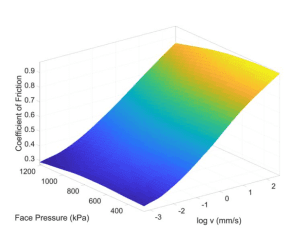
Schlussfolgerungen
Die Reibung zwischen der Riemenscheibenbeschichtung und der unteren Abdeckung des Förderbands hängt sowohl von der Schlupfgeschwindigkeit als auch vom Flächendruck ab. Die Beziehung zwischen Reibungskoeffizient, Flächendruck und Geschwindigkeit hilft dabei, den Kontakt zwischen Band und Riemenscheibe und damit die Belastungen, denen die Beschichtung ausgesetzt ist, besser zu definieren. Ein besseres Verständnis der Reibungsmechanik zwischen der Riemenscheibenbeschichtung und der unteren Abdeckung des Förderbands hilft dabei, Design und Effizienz zu verbessern und sicherzustellen, dass die Auswahl der Beschichtung auf einer technischen Analyse für eine bestimmte Anwendung basiert. Die nächste Arbeitsphase dieser Forschung besteht darin, die Tests auf andere Beschichtungstypen auszuweiten und den Einfluss der Temperatur auf die Ergebnisse zu untersuchen.
Große Goldmine in Australien – erhöhte Lebensdauer der Seilrollen mit Elastotec/PROK HVCL
Eine der größten Goldminen Australiens, im Südosten von Perth gelegen, produziert rund 750,000 o
T&T Peru 2023
Vielen Dank an den peruanischen Bergbausektor. Vielen Dank für den Raum, um Ihre Herausforderungen zu diskutieren. Vielen Dank
Vorbeugung von Blasenbildung in dampfbeheizten Autoklaven
Dieses technische Bulletin beschreibt die Ursachen der Blasenbildung und beschreibt eine Reihe von