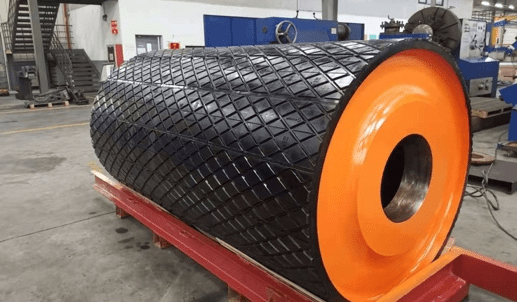
Elastotec: Reducing Downtime and Increasing Productivity in Mining
The main challenges of pulleys in contact with the carry side of the belt
In conveyor systems, pulleys play a critical role in ensuring smooth operation, proper belt tracking, and effective material transportation. Among these, pulleys that come into contact with the carry side of the belt—often referred to as the “dirty side”—face unique and demanding challenges. Unlike the return side of the belt, which is relatively clean, the carry side is in direct contact with the bulk material being transported, introducing complexities that significantly impact the performance and longevity of conveyor components.
This article delves into the two primary challenges faced by these carry-side pulleys and examines their consequences on the overall conveyor system. Understanding these challenges is essential for designing and maintaining efficient and reliable conveyor operations.
1. Continuously changing belt cover wear profile
One of the most significant challenges for carry-side pulleys is the uneven belt wear profile. Over time, the carry side of the belt develops an uneven wear pattern, with the centre wearing down more than the edges. This wear disparity displaces the belt cords and introduces uneven tension, leading to localised stress and increased wear on the pulley lagging.
The constantly shifting belt cover wear profile has a number of consequences:
- Differential speed between cords produces a torsion effect introducing excessive shear stresses with the potential to damage the lagging and splices.
- Uneven lagging surfaces can reduce traction, leading to belt slippage.
Over time, this dynamic wear pattern compromises the performance of the pulley, necessitating frequent maintenance or replacement of the lagging to maintain optimal conveyor performance.
2. Material build-up risks
The carry side of the belt is exposed to the transported material, making pulleys in contact with this side especially prone to material build-up. This issue arises from:
- Adhesion of Fine Particles: Dust, mud, and fine particles can adhere to the lagging, forming layers that interfere with the pulley’s grip on the belt. These are non driven pulleys so grip is not that important as there is no traction. The two problems are
- 1) material build up on pulley surface changing the roundness of the pulley and pushing belt cords and overstressing them
- 2) rocks trapped at the interface (even if not stuck to the pulley surface) will push the cord of the belt with the potential of belt damage.
- Accumulation of Bulk Material: Larger particles or chunks of material can lodge between the lagging and the belt, creating high points on the pulley surface.
Material build-up on the pulley introduces a range of operational challenges:
- Reduced traction between the pulley and belt can lead to belt slippage and inefficiencies in material handling.
- Uneven build-up creates localised pressure points, accelerating wear on both the lagging and the belt.
- Excessive build-up can disrupt belt tracking, leading to alignment issues and potential damage to the belt edges.
If left unaddressed, material build-up can lead to premature lagging failure, increased wear on the belt, and costly system downtime.
The consequences for conveyor systems
The unique challenges faced by carry-side pulleys have direct implications for the performance and durability of critical conveyor components, including:
1. Pulley lagging longevity
The constantly changing belt cover and risk of material build-up on the pulley surface significantly reduce the lifespan of pulley lagging. Frequent wear and tear of lagging requires more regular maintenance, increasing operational costs and downtime.
2. Belt splice and cord durability
The stress introduced by uneven pulley surfaces or material accumulation can over-stress belt splices and cords over time. This not only shortens the belt’s service life but also increases the likelihood of unexpected belt failures, disrupting operations and causing costly delays.
Addressing the challenges with engineered solutions
To mitigate these challenges, engineered solutions tailored to the specific operating conditions of carry-side pulleys are essential. Key strategies include:
1. Hot Vulcanised Ceramic Lagging
In many applications, and after doing a proper engineering analysis, Elastotec’s Hot Vulcanised Ceramic Lagging offers superior performance by addressing the unique wear and build-up challenges of carry-side pulleys. Key benefits include:
- Enhanced Abrasion Resistance: Ceramic tiles provide a hard, durable surface that resists wear from abrasive materials.
- Self-Cleaning Properties: The design of the ceramic lagging minimises material build-up, ensuring consistent traction and reducing maintenance requirements.
2. Routine maintenance and monitoring
Regular inspection and cleaning of carry-side pulleys can prevent material build-up and identify wear issues before they escalate. Proactive maintenance extends the service life of both the lagging and the belt.
3. Custom solutions for specific applications
Each conveyor system operates under unique conditions, and the choice of lagging material and design should be tailored accordingly. Elastotec’s expertise in engineered pulley lagging ensures solutions that are optimised for specific operating environments.
The key to optimising carry-side pulley performance
Pulleys in contact with the carry side of the belt face a combination of dynamic wear profiles and material build-up risks, making their maintenance and design critical to conveyor system efficiency. By understanding these challenges and implementing engineered solutions like hot vulcanised ceramic lagging, operators can enhance the longevity and performance of their conveyor systems while minimising downtime and maintenance costs.
For more information on how Elastotec’s innovative solutions can help address these challenges, contact our team of experts today.