
Vulcanisation à chaud ou collage à froid pour les applications de revêtement de poulies : quelles sont les différences ?
Introduction
Le revêtement collé à froid est utilisé depuis plus de cinquante ans, principalement en raison de sa facilité et de sa commodité d'application. Bien que le revêtement en caoutchouc vulcanisé à chaud soit également utilisé depuis de nombreuses années, le revêtement en céramique vulcanisé à chaud et le revêtement en polyuréthane sont des ajouts plus récents.
La sélection du retardateur est l’un des quatre piliers nécessaires à la performance du retardateur conçu.

Ce bulletin technique fournit des détails sur les différences entre le revêtement vulcanisé à chaud et le revêtement collé à froid, et sur l'impact de ces différences sur les performances d'utilisation finale.
Le calfeutrage collé à froid, comme son nom l'indique, est un système d'application de calfeutrage qui s'effectue à température ambiante. Cela signifie normalement des températures comprises entre +15°C et +40°C. Lorsque les températures ambiantes se situent en dehors de cette plage, les applicateurs prennent normalement des mesures pour ajuster la température de la zone de travail afin qu'elle se situe dans cette plage.
Le principal avantage du calorifugeage collé à froid est qu'il peut être réalisé aussi bien sur le terrain (c'est-à-dire sur le convoyeur) qu'en atelier et ne nécessite aucun équipement spécialisé.
L'application de revêtement vulcanisé à chaud implique le durcissement du revêtement à température élevée, généralement 140-160°C pendant 3 à 6 heures. Cela nécessite l'utilisation d'un équipement spécialisé appelé autoclave (PHOTO #1) et ne peut être effectué qu'en usine. Le revêtement vulcanisé à chaud ne peut pas être effectué dans le
champ ou avec la poulie installée sur le convoyeur.
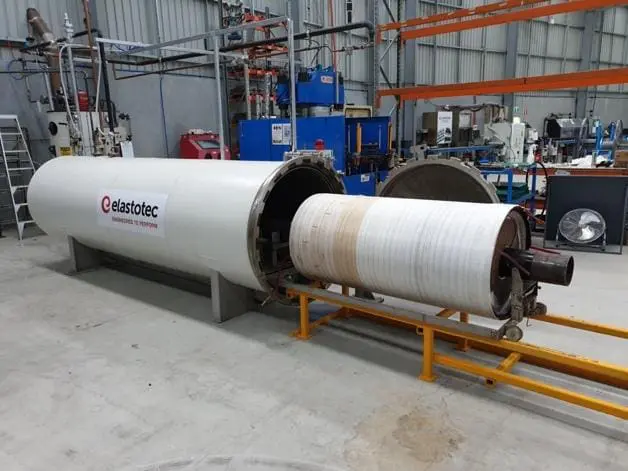
Le principal avantage du revêtement vulcanisé à chaud est que le processus est beaucoup plus robuste que le collage à froid et, par conséquent, l'adhérence du revêtement à la poulie est beaucoup plus forte, offrant ainsi des liaisons de déchirure du caoutchouc toujours plus solides.
Les différences entre les revêtements collés à froid et les revêtements vulcanisés à chaud
Les systèmes
Système de collage à froid
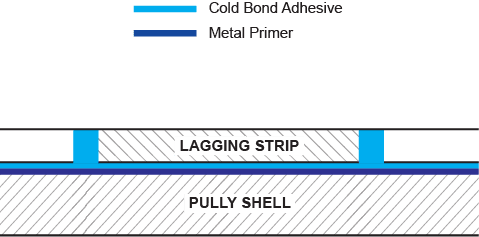
Système de collage calorifuge vulcanisé à chaud
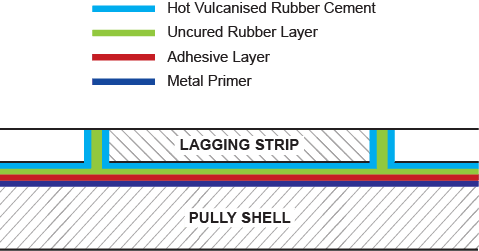
L'application
TEMPÉRATURE DE DURCISSEMENT
Collage à froid Vulcanisation à chaud
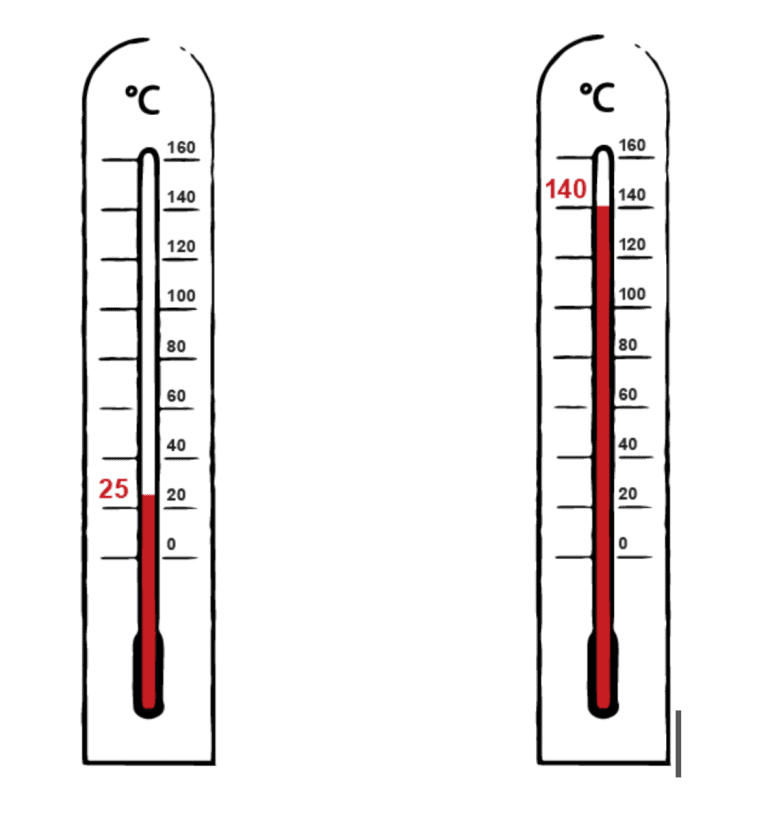
TEMPS DE DURCISSEMENT
Collage à froid Vulcanisation à chaud
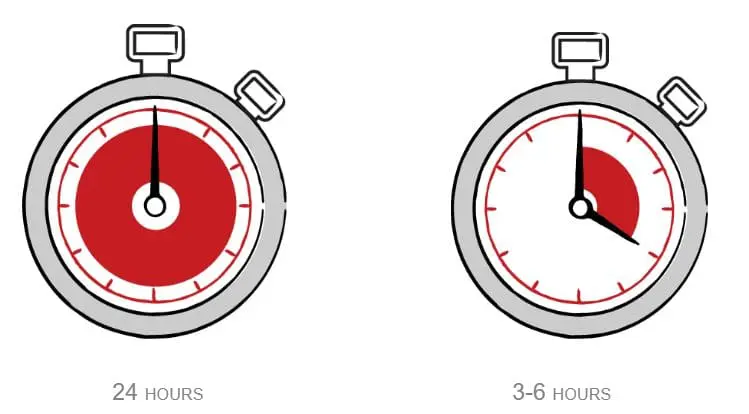
PRESSION DE DURCISSEMENT
Collage à froid Vulcanisation à chaud
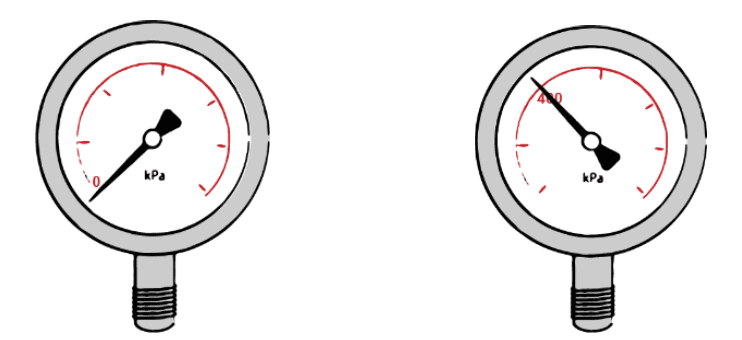
Application de revêtement collé à froid sur la coque de la poulie

Système de vulcanisation à chaud
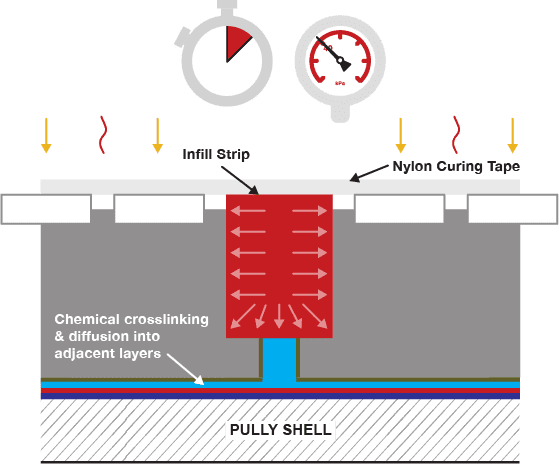
Revêtement collé à froid appliqué à la poulie
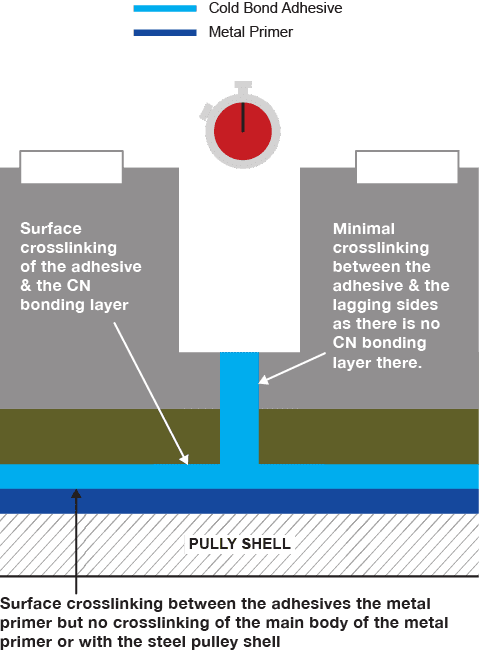
Système de vulcanisation à chaud
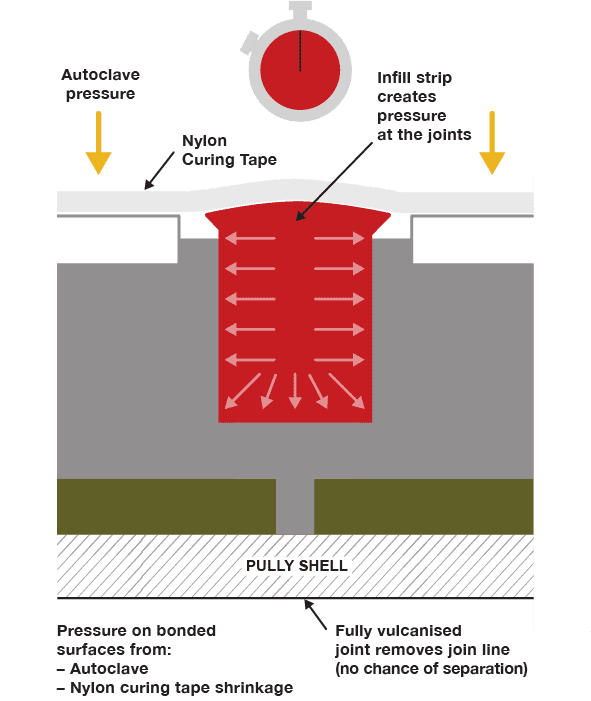
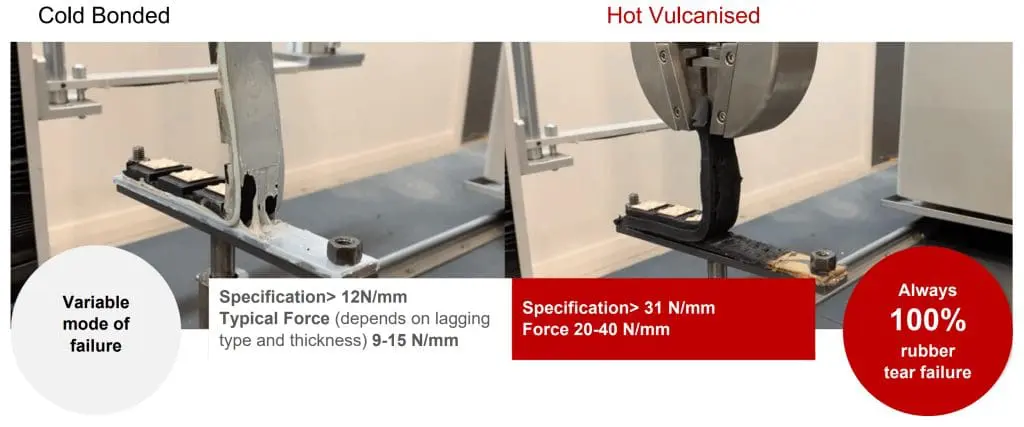
Résumé du collage à froid
L'adhérence à froid dépend en grande partie d'un processus appelé cristallisation qui se produit dans les deux couches adhésives (une appliquée sur la coque de la poulie et l'autre appliquée sur l'arrière du revêtement) immédiatement après l'application et le séchage de l'adhésif. La cristallisation est un processus physique au sein des couches adhésives qui convertit deux couches séparées en une seule couche continue. Le taux de cristallisation dépend du temps et de la température. La variabilité de ces deux facteurs, dans chaque application de revêtement à froid, contribue grandement à la variabilité de la force d'adhérence inhérente à ce processus. L'ajout d'un « durcisseur » chimique est conçu pour assurer une certaine fixation chimique à la couche de support en caoutchouc et à l'apprêt métallique. Étant donné que la couche de support en caoutchouc du revêtement est déjà vulcanisée et que le processus de collage est effectué à température ambiante et à pression ambiante, il n'est pas possible qu'une diffusion significative de l'adhésif, de l'apprêt métallique et du caoutchouc se produise. La figure 5 montre comment la cristallisation et la réaction chimique se produisent en grande partie dans les couches adhésives avec une réaction chimique et une diffusion minimales dans le support en caoutchouc du revêtement ou dans l'apprêt métallique de la coque de la poulie en acier.
C'est ce manque de diffusion entre les différentes couches du système de liaison qui constitue un facteur important dans les limites de la force et de la cohérence de l'adhérence à froid.
Les résultats des tests suivants donneront une indication de la variabilité de la force d’adhérence qui peut être introduite dans le processus de collage à froid :
FORCE D'ADHÉRENCE
1. Résistance d'adhérence – Temps de test depuis l'application du revêtement sur la coque de la poulie en fonction de la température ambiante
TEMP (°C) | TEMPS (heures) | ADHÉRENCE (N/mm) |
---|---|---|
10 | 4 | 4.0 |
10 | 8 | 6.9 |
10 | 12 | 8.9 |
10 | 24 | 11.8 |
10 | 96 | 15.9 |
TEMP (°C) | TEMPS (heures) | ADHÉRENCE (N/mm) |
---|---|---|
20 | 4 | 6.3 |
20 | 8 | 9.8 |
20 | 12 | 11.4 |
20 | 24 | 14.6 |
20 | 96 | 16.2 |
TEMP (°C) | TEMPS (heures) | ADHÉRENCE (N/mm) |
---|---|---|
35 | 4 | 8.0 |
35 | 8 | 11.4 |
35 | 12 | 14.4 |
35 | 24 | 16.1 |
35 | 96 | 16.5 |
2. Résistance à l'adhérence - Temps de test entre l'application de la dernière couche d'adhésif et l'application du revêtement sur la coque de la poulie
TEMP (°C) | TEMPS (heures) | ADHÉRENCE (N/mm) |
---|---|---|
25 | 5 | 3.8 |
25 | 7 | 15.5 |
25 | 10 | 15.2 |
25 | 15 | 12.1 |
25 | 20 | 11.5 |
3. Force d'adhérence avec l'âge de la couche de liaison CN en retard
ÂGE DE LA COUCHE DE LIAISON (mois) | ADHÉRENCE (N/mm) |
---|---|
> 24 | 6.4 |
1 | 15.8 |
4. Force d'adhérence - Méthode d'application de l'adhésif sur le revêtement - 1ère couche
ÂGE DE LA COUCHE DE LIAISON (mois) | PROCÉDÉ D'APPLICATION | ADHÉRENCE (N/mm) |
---|---|---|
10 | Vigoureux | 13.5 |
10 | Revenu | 10.5 |
1 | Vigoureux | 16.5 |
1 | Revenu | 16.9 |
5. Résistance d'adhérence par rapport à la finition de la surface de la coque de la poulie
ÂGE DE LA COUCHE DE LIAISON (mois) | ADHÉRENCE (N/mm) | MODE DE DÉFAILLANCE |
---|---|---|
7.8 | 100% PA | |
50-100 | 15.5 | 50-100% de temps de réaction |
6. Impact du point de rosée sur la force d'adhérence
TEMPÉRATURE DE LA POULIE/DU RECHERCHE PAR RAPPORT AU POINT DE ROSÉE (°C) | ADHÉRENCE (N/mm) |
---|---|
> 5 | > 12.0 |
<5 | 2 - 9 |
Résumé de la vulcanisation à chaud
- La température élevée (130-140°C) déclenche une série de réactions chimiques entre la coque de la poulie en acier et l'apprêt métallique, l'apprêt métallique et l'adhésif en caoutchouc, et l'adhésif et le revêtement. Il y a une diffusion et une réaction importantes des produits chimiques de durcissement entre toutes les couches de liaison (apprêt métallique, adhésif, colle en caoutchouc, couche de liaison non durcie et couche de support en caoutchouc pré-durcie). Ces réactions donnent lieu à des liaisons chimiques très fortes.
- La pression élevée dans l'autoclave pendant plusieurs heures maximise et assure un bon contact entre le revêtement et la coque de la poulie, ce qui augmente l'adhérence.
- Le ruban de durcissement en nylon humide rétrécit en séchant à la température élevée qui applique une pression importante sur toute la surface de la poulie et en particulier sur les joints.
Pression élevée sur le revêtement et sur toutes les surfaces de collage en raison de la pression de l'autoclave, rétrécissement du ruban de durcissement en nylon humide lors de son séchage et augmentation du volume du revêtement en raison de la dilatation thermique lorsque la température augmente de la température ambiante à 140°C.
Les déchirures du caoutchouc forment des liaisons chimiques sur toute la surface de la poulie et au niveau des joints entre les bandes – les joints entre les bandes disparaissent effectivement comme le montre la photo ci-dessous :
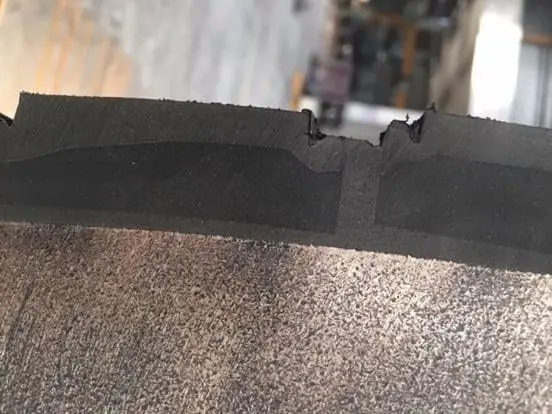
Qu'est-ce que cela signifie pour les performances de la poulie ?
La technologie minière évolue rapidement pour répondre aux défis de l'extraction de minéraux dans des endroits reculés, souvent dans des conditions climatiques extrêmes et à partir de gisements situés en profondeur. Pour atteindre des coûts de production compétitifs et durables, les grandes sociétés minières adoptent un certain nombre de nouvelles technologies, notamment l'utilisation croissante de l'automatisation et l'utilisation de convoyeurs à entraînement sans engrenage de grande puissance pour leurs besoins de transport.
Pour maximiser l'efficacité de ces technologies, la fiabilité de l'équipement devient essentielle pour garantir que les coûts de production et le rendement visés sont atteints. Pour les tambours de convoyeur, cela a nécessité l'utilisation de revêtements de tambour capables de supporter les charges accrues appliquées par les systèmes d'entraînement à haute puissance, les extrêmes de température de -50 °C à +75 °C et, dans de nombreux cas, le fonctionnement dans des environnements extrêmement humides et corrosifs.
Traditionnellement, de nombreuses poulies étaient équipées de systèmes de collage à froid qui étaient pratiques à utiliser et ne nécessitaient pas l'utilisation d'équipements spécialisés. En effet, la commodité était prioritaire sur les performances.
Aujourd’hui, les coûts des temps d’arrêt imprévus des convoyeurs sont énormes : par exemple, pour un convoyeur transportant 10,000 100.00 tonnes/heure de minerai d’une valeur de 24 $US la tonne et fonctionnant 7 heures sur 1,000,000, XNUMX jours sur XNUMX, les temps d’arrêt imprévus des convoyeurs coûtent à la société minière XNUMX XNUMX XNUMX $US par heure.
Depuis cinq ans, Elastotec collecte des données auprès de son réseau d'applicateurs agréés sur les modes de défaillance des garnitures qui sont observés sur les poulies envoyées en rénovation. Les modes de défaillance les plus courants sont les suivants :
- porter
- décollement de la coque de poulie
- levage des bords
- corrosion au niveau des joints entre les bandes de calorifugeage entraînant un décollement du calorifugeage
- perte de carreaux de céramique due au décollement
Il a été bien documenté que le collage à froid des bandes de calorifugeage des poulies augmente le risque de défaillance prématurée de la bande de calorifugeage en raison du décollement de la coque de la poulie, du soulèvement des bords et de la corrosion de la coque au niveau des joints entre les bandes de calorifugeage. Ces types de défaillances peuvent, dans de nombreux cas, nécessiter un nouveau calorifugeage sur le convoyeur, avec perte de production. Étant donné que les conditions de calorifugeage sur le convoyeur ne sont pas idéales, ces problèmes se reproduisent souvent.
En cas de défaillance due à la corrosion au niveau des joints entre les bandes de calorifugeage, cela peut également entraîner des dépenses supplémentaires inutiles lorsque la profondeur de la corrosion réduit l'épaisseur de la coque en dessous de ce qui est requis pour les charges de fonctionnement prévues, et la poulie doit être mise au rebut.
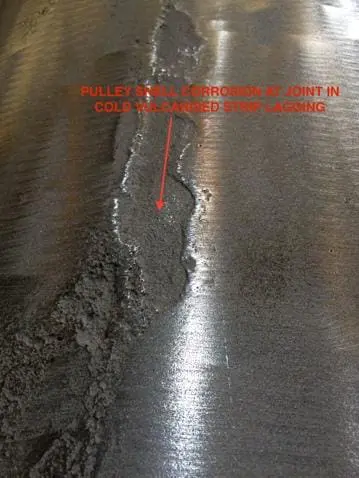
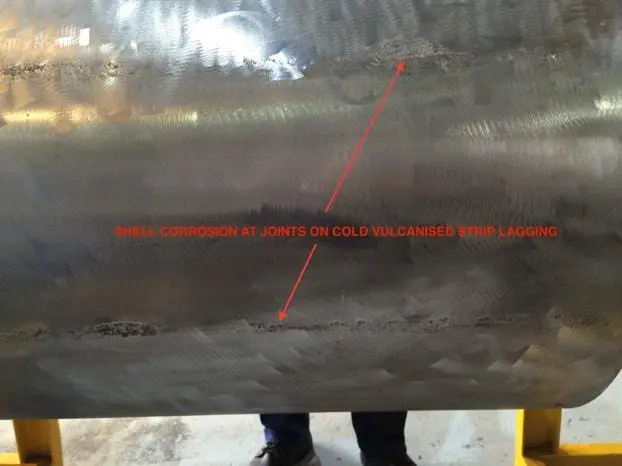
Les trois causes les plus courantes d’échec du collage à froid sont :
1. Décollement du revêtement de la coque de poulie
Le décollement de la coque de poulie est une défaillance catastrophique qui se produit le plus souvent sur les poulies motrices et les poulies de courbure à haute tension lorsque la force appliquée au revêtement dépasse la force d'adhérence de la liaison entre le revêtement et la coque de poulie.
La norme courante pour le collage par vulcanisation à froid est une adhérence de 9 N/mm – des conditions idéales dans une application en usine, si tout est fait correctement, peuvent fournir une adhérence de 9 à 15 N/mm. Cependant, lorsque le revêtement est vulcanisé à froid sans procédures d'application OEM, ou dans de mauvaises conditions (sur le convoyeur), dans de nombreux cas, l'adhérence est inférieure à la norme de 9 N/mm.
Pour que le revêtement se décolle, il suffit que les forces de cisaillement appliquées au revêtement soient supérieures à l'adhérence du revêtement à la coque de la poulie.
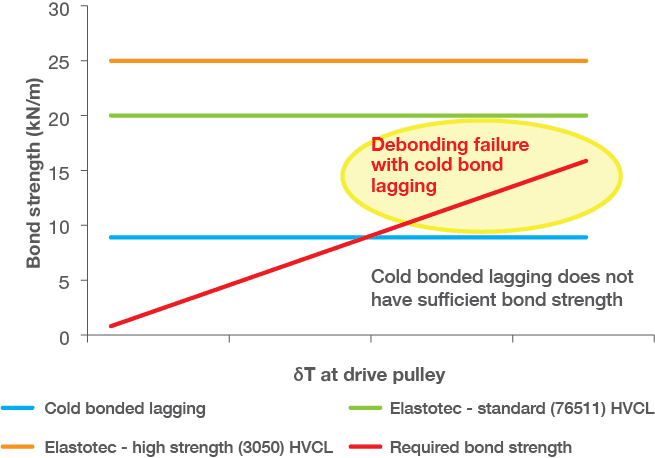
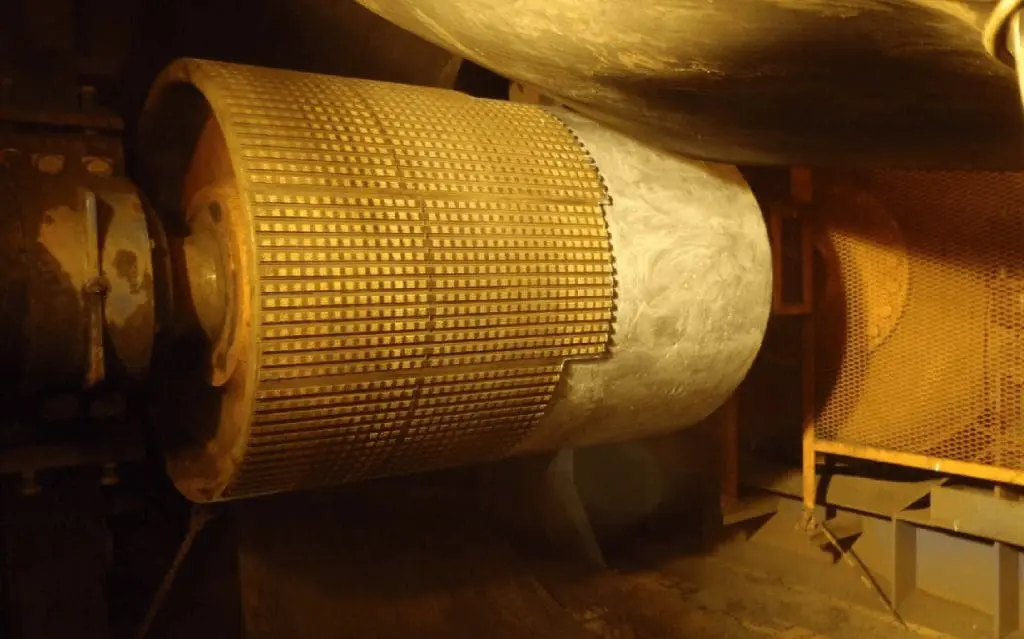
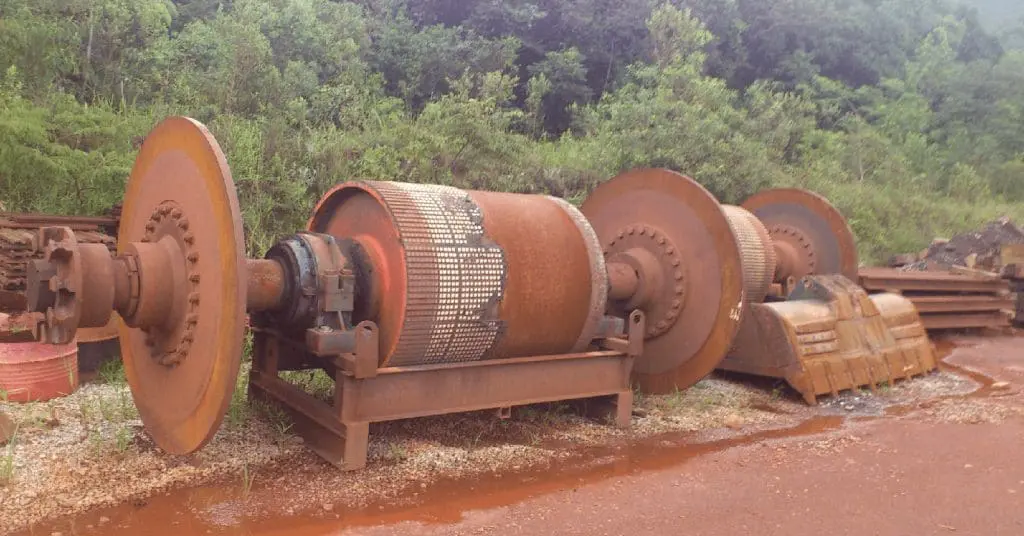
Un autre facteur qui augmente la probabilité de défaillance avec le revêtement collé à froid est la présence de forces de cisaillement localisées. Dans les poulies d'entraînement, à mesure que le rapport T1/T2 augmente, les forces de cisaillement cycliques auxquelles le revêtement est exposé augmentent. Le revêtement collé à froid a une tolérance plus faible à ces forces de cisaillement cycliques que le revêtement vulcanisé à chaud et donc les conditions de fonctionnement du convoyeur telles que le fonctionnement en arrêt/démarrage ou des charges plus élevées lorsque les tonnages de production sont augmentés peuvent entraîner un décollement qui ne se produirait pas avec le revêtement vulcanisé à chaud. Les photos ci-dessous montrent une poulie avec revêtement collé à froid qui a échoué dans les deux semaines suivant son installation sur un nouveau site. Le convoyeur était en cours d'installation de sorte qu'il y avait beaucoup d'arrêts/démarrages avec un rapport T1/T2 élevé (> 4).
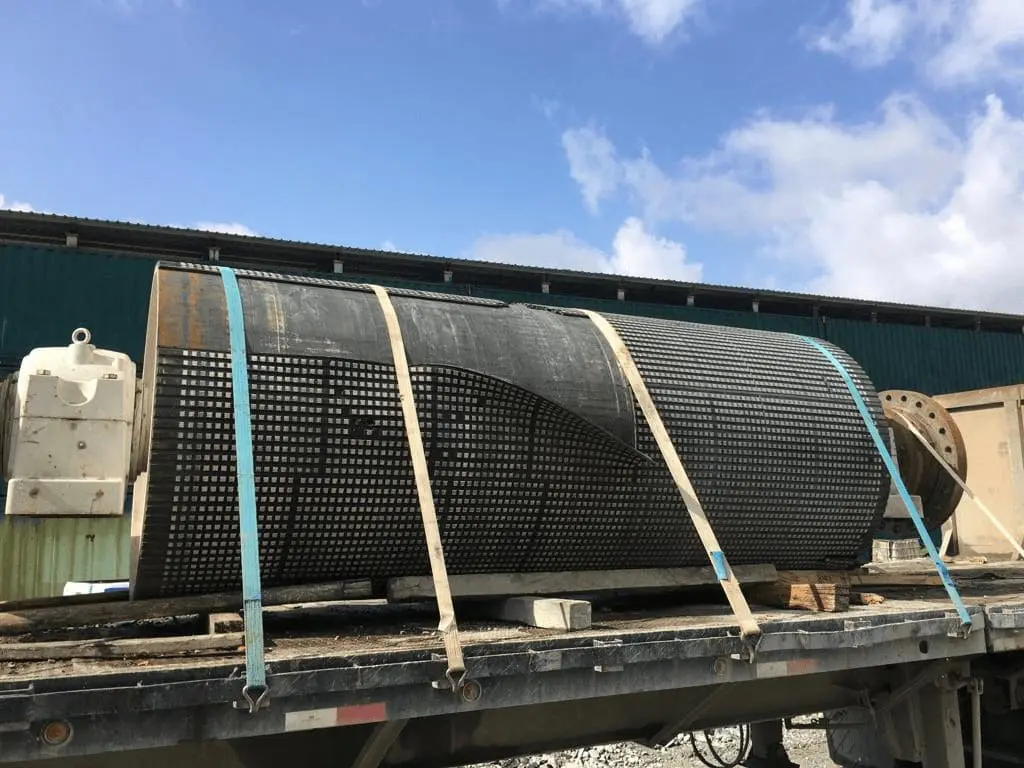
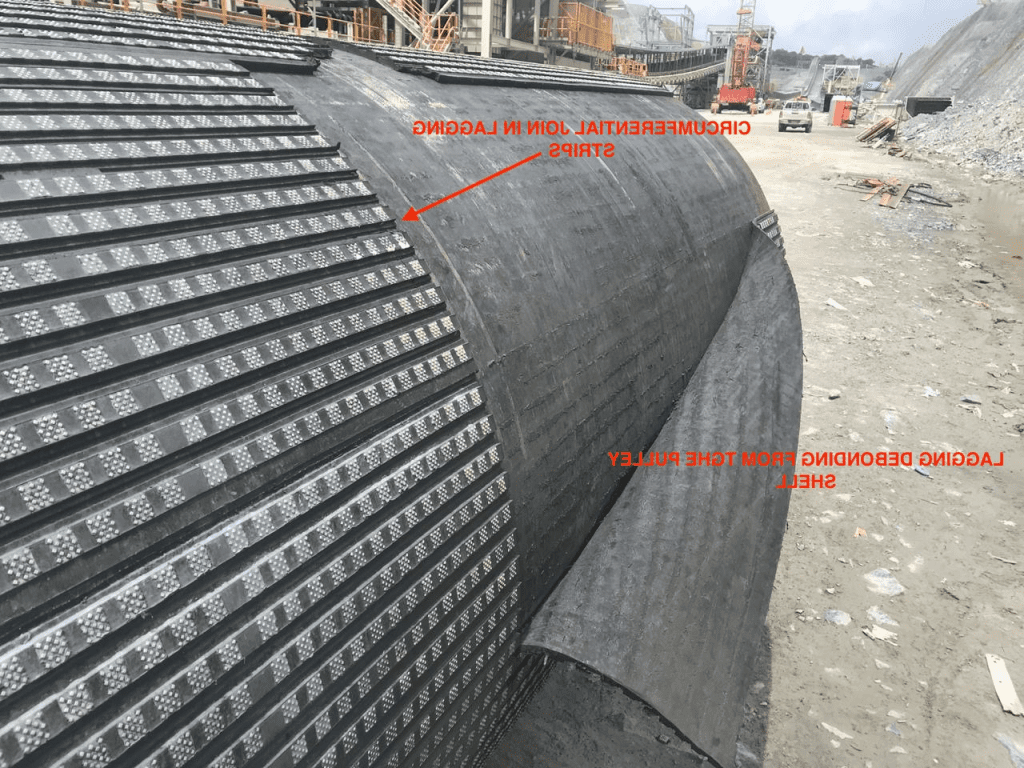
PHOTO #7 DÉFAILLANCE DU RETARDS DE COLLAGE À FROID DE LA POULIE D'ENTRAÎNEMENT APRÈS DEUX SEMAINES D'INSTALLATION SUR UN NOUVEAU CONVOYEUR AVEC APPLICATION STOP/START
Plusieurs facteurs se combinent pour amplifier le risque d’échec du décollement, notamment :
- Les charges sur les poulies en retard sont cycliques et passent de zéro à la pleine charge plusieurs fois par minute, en fonction du régime de la poulie. Cette action dynamique est bien plus sévère qu'une charge statique appliquée.
- Les charges de démarrage, en particulier avec une bande transporteuse chargée, seront bien supérieures à la charge de fonctionnement normale.
- Les basses températures provoquent une rigidité et une perte de souplesse des revêtements en caoutchouc des courroies et des composants en caoutchouc des garnitures de poulies. Plus la température est basse, plus ce phénomène est important. Cette perte de souplesse concentre les charges appliquées sur la partie la plus fragile de la garniture vulcanisée à froid, à savoir le système de liaison.
Les photos ci-dessous montrent une poulie avec revêtement vulcanisé à froid qui a cédé peu après son installation dans des conditions de fonctionnement à -35°C. Notez que les picots en caoutchouc surélevés à la surface de la poulie sont toujours intacts et n'ont pas eu le temps de s'user.
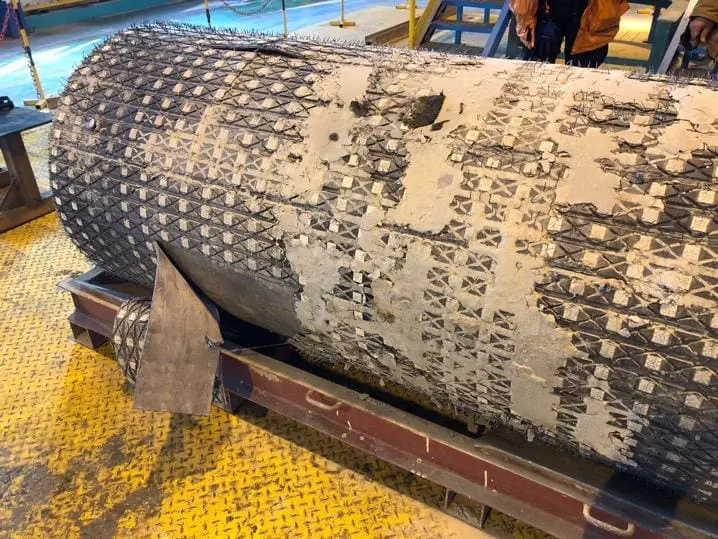
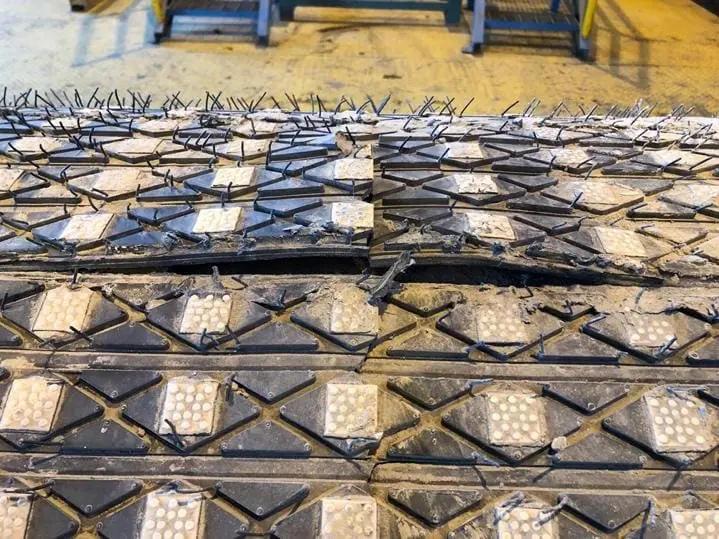
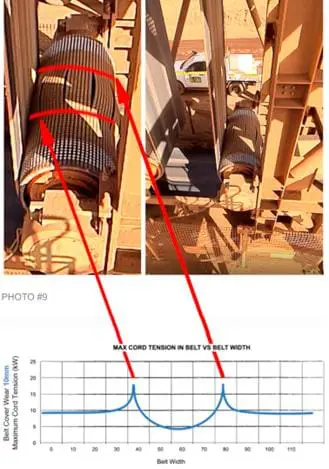
Une défaillance de décollement similaire peut se produire sur les poulies non motrices qui sont soumises à des forces de cisaillement localisées élevées - cela est le plus souvent observé sur les poulies qui entrent en contact avec le côté sale de la courroie, mais peut également être observé sur les poulies de rappel et les poulies de retournement (voir la photo ci-dessous).
Pour les poulies qui entrent en contact avec le côté sale de la courroie, les forces de cisaillement localisées sont générées par le profil irrégulier qui résulte de l'usure du revêtement de la courroie, les niveaux d'usure croissants conduisant à des forces de cisaillement localisées croissantes. Un document technique détaillé sur ce problème est disponible sur le site Elastotec ELA1220-High Tension Bend Pulleys.
Test d'adhérence sur le revêtement de poulie
De nombreux applicateurs de revêtements isolants utilisant la technique d'application par vulcanisation à froid pour appliquer les revêtements de poulies ne mesurent pas la force d'adhérence obtenue sur chaque poulie et n'ont donc aucune idée de l'adhérence obtenue sur chaque installation.
Le revêtement en céramique vulcanisé à chaud (HVCL) Elastotec offre une liaison au déchirement garantie à 100 % en caoutchouc entre le revêtement et la coque de la poulie qui atteint des forces d'adhérence de 20 à 25 N/mm, soit environ le double de l'adhérence qui peut être obtenue par une application de revêtement vulcanisé à froid dans des conditions idéales.
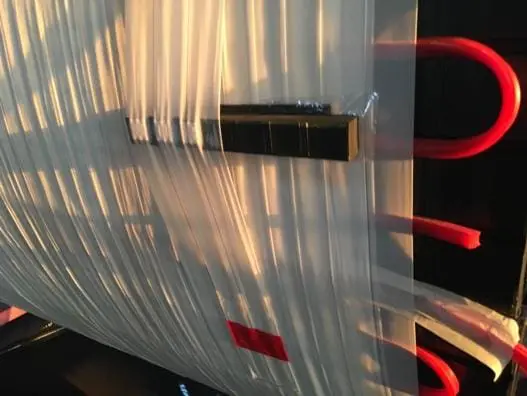
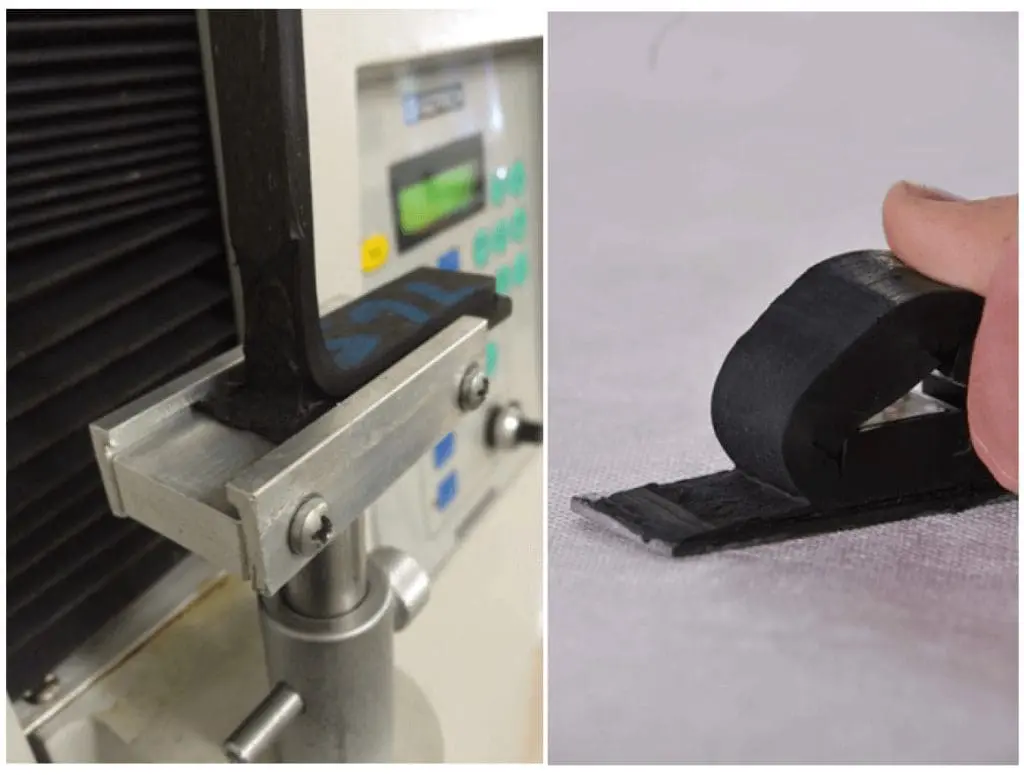
La photo suivante montre une méthode courante pour retirer le revêtement vulcanisé à froid de la coque de la poulie en appliquant une charge sur le revêtement à 90 degrés par rapport à la poulie.
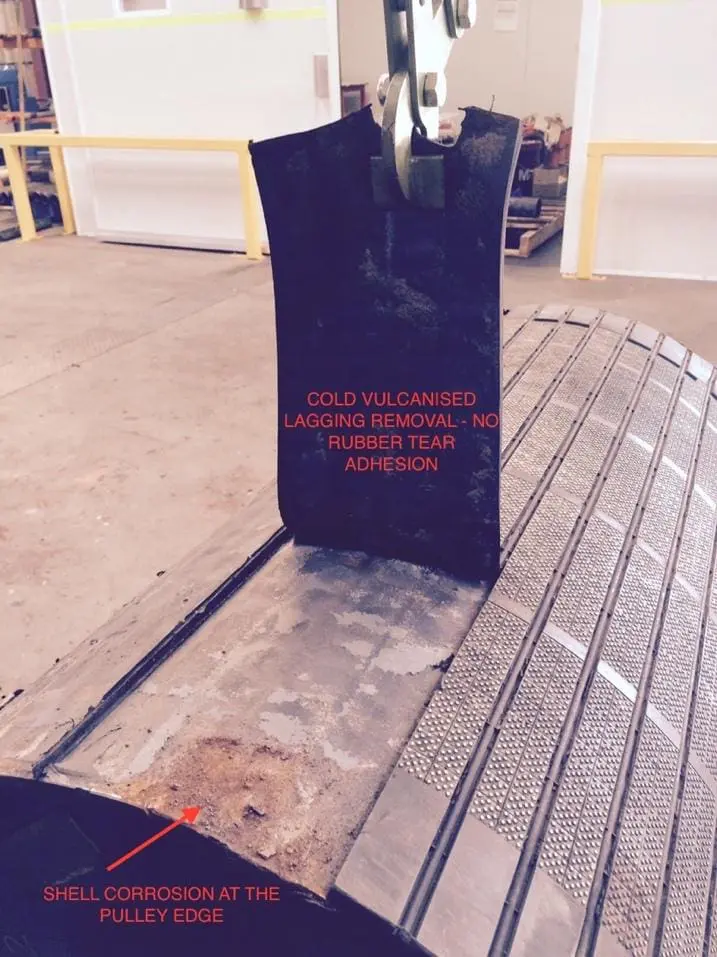
Pour Elastotec HVCL, la liaison est si forte que si cette technique est essayée, la poulie peut être soulevée par le revêtement ou le revêtement se déchirera – il n'y a pas de décollement de la coque de la poulie.
Grâce à l'adhérence à 100 % du caoutchouc, le revêtement ne se décolle pas de la coque de la poulie. Elastotec dispose actuellement de plus de 500 poulies équipées de ce système de collage sur un certain nombre d'installations de convoyeurs fonctionnant avec des entraînements sans engrenage de grande puissance (jusqu'à 6,000 XNUMX kW) et jusqu'à présent, aucun échec de décollement n'a été constaté.
2. Relevage des bords
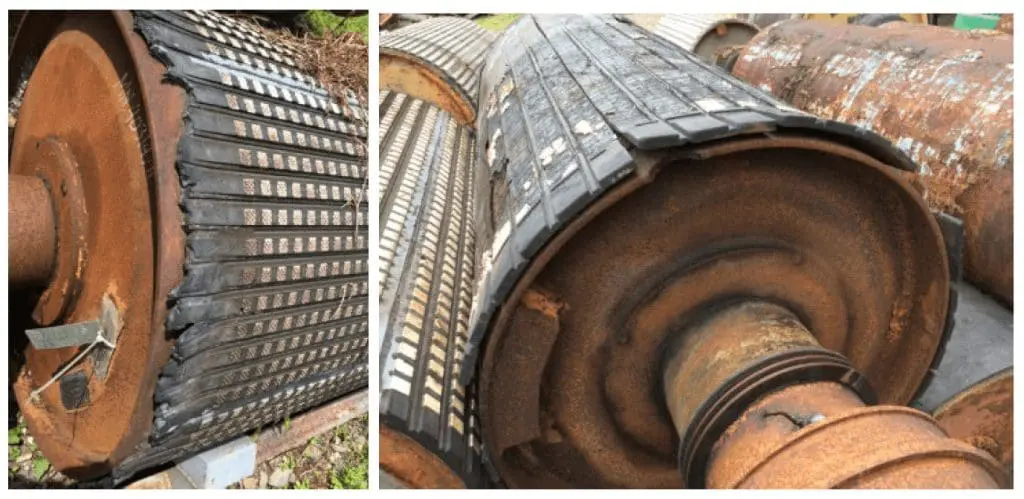
Dans de nombreux cas de défaillance du soulèvement des bords, le revêtement de la poulie est encore entièrement utilisable. La photo ci-dessous montre une poulie recouverte de polyuréthane vulcanisé à froid et mise en service dans une usine de lavage du charbon. La corrosion de la coque a commencé à l'extrémité de la coque et a entraîné la séparation du revêtement de la poulie dans cette zone. La photo montre également que le revêtement n'est pas usé et qu'il serait utilisable si le soulèvement des bords ne s'était pas produit.
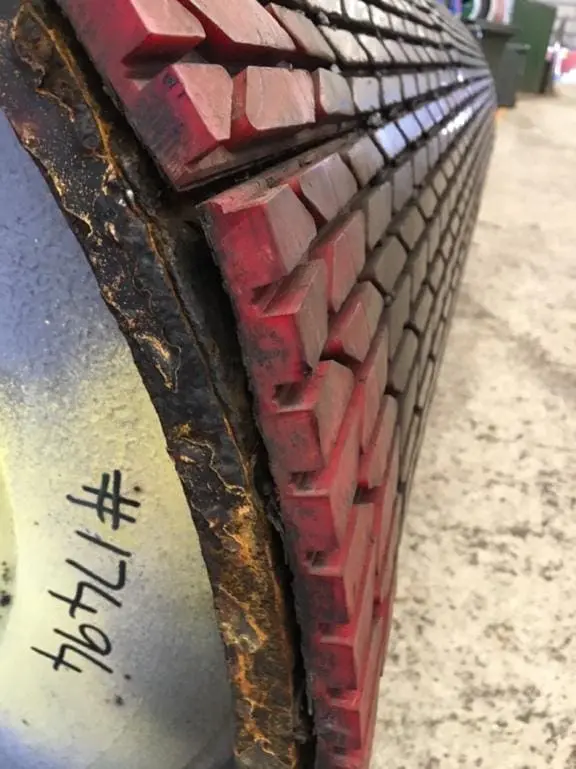
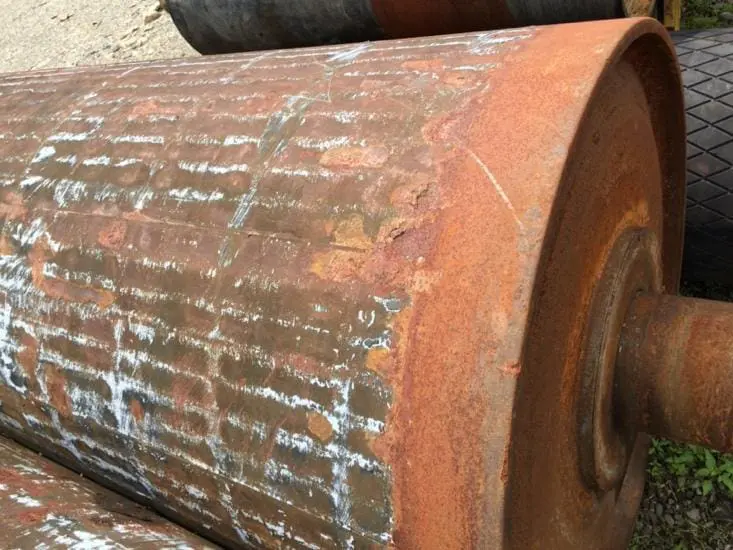
Le motif gris clair correspond aux endroits où une couche de colle reste sur la coque de la poulie après le retrait du revêtement. Cela correspond aux creux dans le profil du revêtement. Les zones dépourvues de colle sont les parties surélevées du revêtement qui ont été martelées lors du processus d'application par vulcanisation à froid.
Cela a permis d'obtenir un meilleur contact et une meilleure adhérence entre le revêtement et la coque de poulie directement sous les zones de revêtement surélevées, et un contact et une adhérence plus faibles dans les zones de revêtement encastrées. Lorsque les extrémités de la coque de poulie sont exposées à des conditions humides, l'eau peut pénétrer entre le revêtement et la coque de poulie dans les zones situées sous le profil de revêtement encastré. Une fois que la corrosion de la coque commence, elle se propage rapidement autour de l'extrémité de la coque et le revêtement se soulève de la coque de poulie et est facilement endommagé (voir photos ci-dessous).
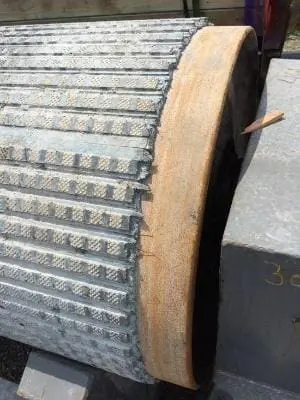
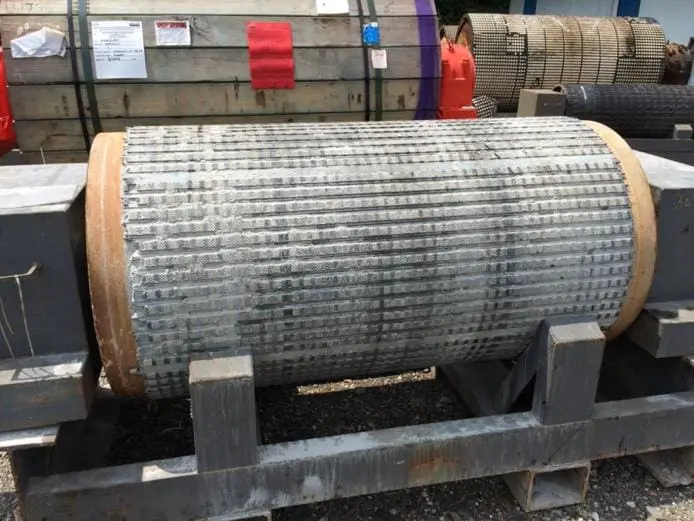
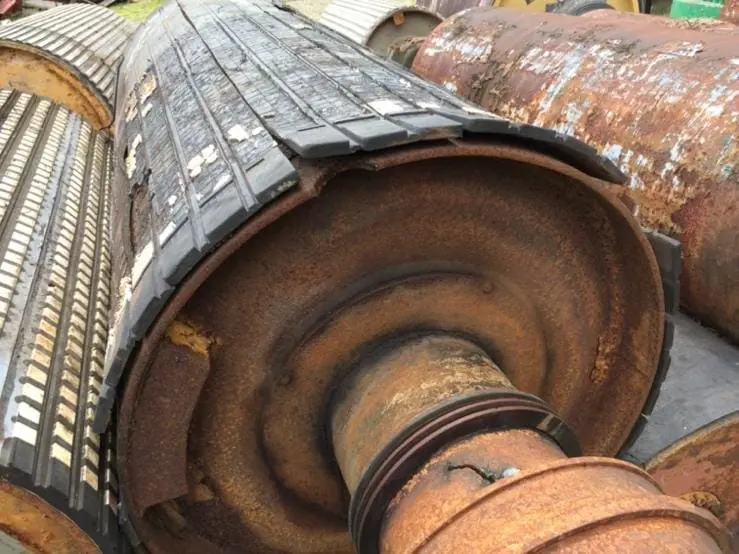
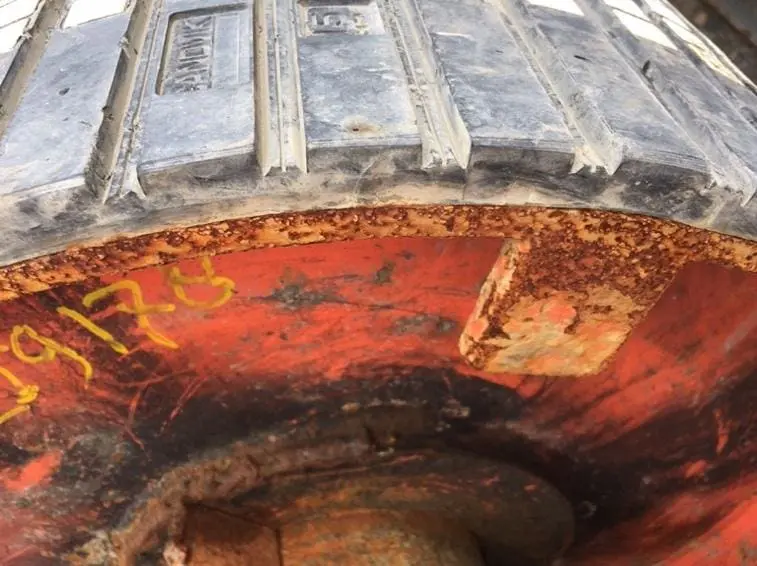
L'application de revêtement vulcanisé à chaud élimine le risque de défaillance du revêtement en raison du soulèvement des bords.
3. Défaillance articulaire
Les joints entre les bandes de calorifugeage constituent un autre point faible qui conduit régulièrement à la défaillance du calorifugeage. Deux facteurs principaux contribuent à la défaillance des joints lors de l'application de calorifugeage vulcanisé à froid :
- Techniques d'application et de fabrication
- Forces appliquées aux joints en retard par la courroie pendant le fonctionnement.
En ce qui concerne les techniques d'application et la qualité de fabrication, de nombreux applicateurs de calorifuges utilisent une technique appelée calorifugeage « bout à bout », où chaque bande de calorifugeage est « collée » contre la bande précédente. Selon les compétences et le soin apportés par l'opérateur, le résultat peut varier d'une absence d'espace entre les bandes à un espace de plusieurs millimètres de large (voir photo). Il est courant que les applicateurs de calorifuges utilisent des produits d'étanchéité liquides tels que « Sikaflex » pour combler les espaces au niveau des joints. L'utilisation de produits d'étanchéité pour combler les espaces entraînera la défaillance du calorifugeage dans des conditions humides.
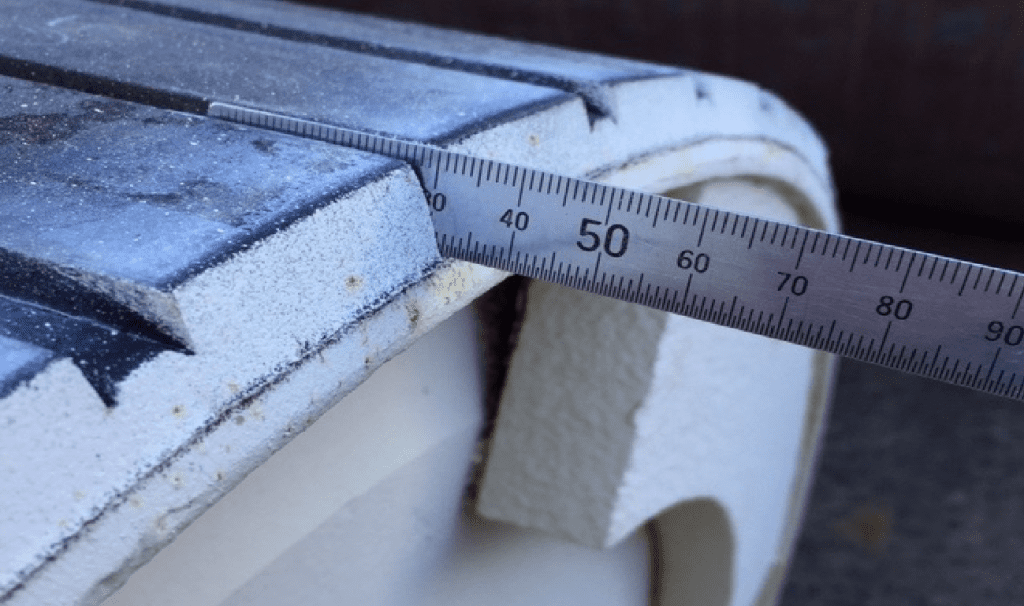
Même lorsque la méthode d'application « bout à bout » est parfaitement réalisée, l'étanchéité du joint repose entièrement sur l'adhésif vulcanisé à froid. Lorsque cette méthode est utilisée sur des poulies avec une « couronne », le revêtement est étiré en place pour fermer le joint. Le joint résultant a le revêtement sous tension, les bandes de revêtement essayant de s'éloigner les unes des autres. Finalement, ces joints s'ouvrent, permettant à l'eau d'atteindre la coque de la poulie et à la corrosion de commencer.
La méthode de calfeutrage « bout à bout » est couramment utilisée car elle constitue la méthode d'application la plus rapide et offre donc le coût le plus bas à l'applicateur. Cette méthode d'application à faible coût compromet considérablement la durée de vie du calfeutrage.
Lorsque nous observons les forces appliquées aux joints de calage par la courroie pendant le fonctionnement, nous constatons que la courroie applique une charge sur le calage – les charges les plus élevées se produisent sur les poulies d'entraînement et sur les poulies de courbure à haute tension.
Lorsque la courroie passe sur la poulie, ces charges agissent de manière à ouvrir les joints entre les bandes de calorifugeage. Lorsque la poulie fonctionne dans un environnement humide, cette ouverture du joint, couplée à la force hydraulique générée par l'eau emprisonnée entre la courroie et le calorifugeage de la poulie, fait que l'eau atteint la coque de la poulie et provoque de la corrosion.
Cette corrosion finit par entraîner un décollement du revêtement le long des joints – voir photos ci-dessous.
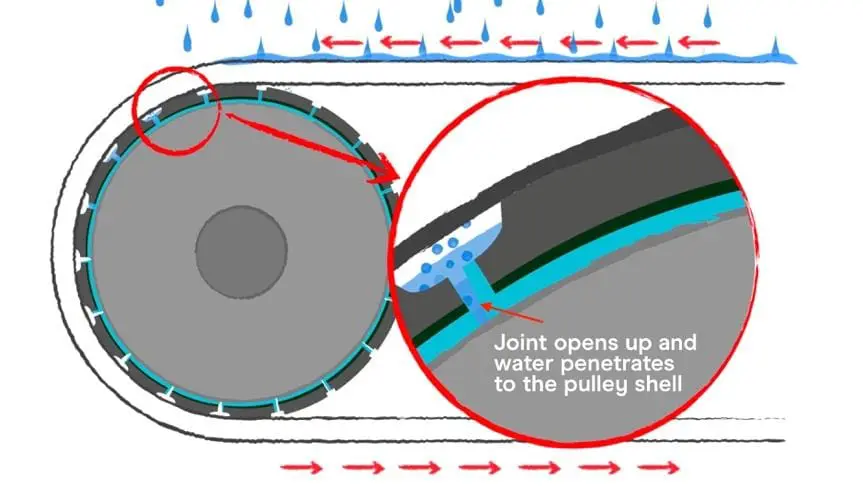
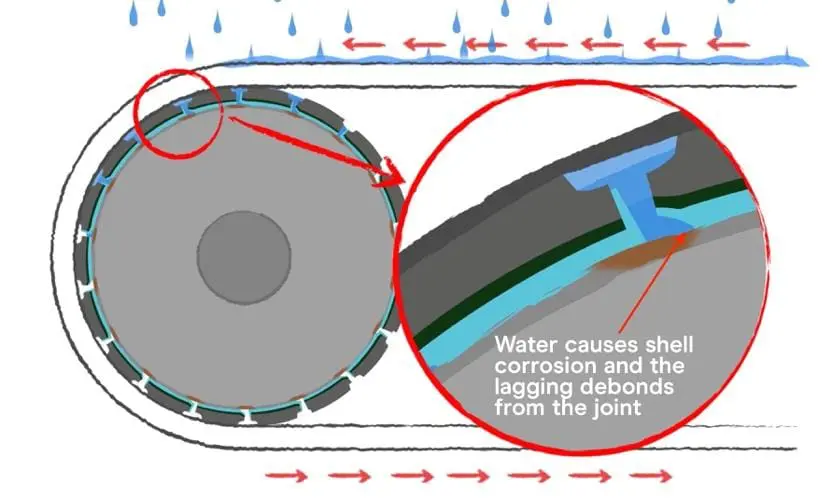

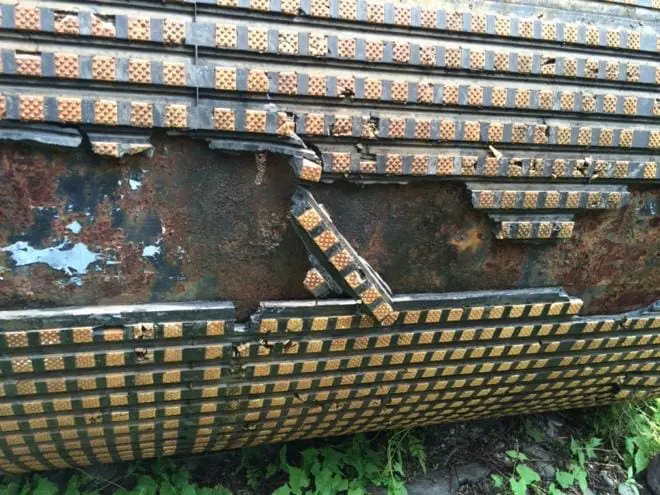
Lorsqu'un revêtement vulcanisé à chaud est appliqué sur la coque de la poulie, il n'y a pas de joints entre les bandes car la couche de liaison non vulcanisée le long du bord de chaque bande fusionne pour former une feuille de revêtement continue sans joints ni points faibles entre les bandes.
Cela élimine le risque de défaillance du retardateur au niveau des joints entre les bandes de retardateur.
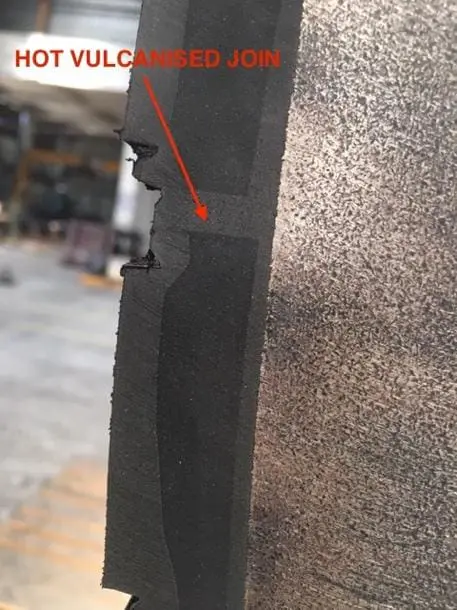
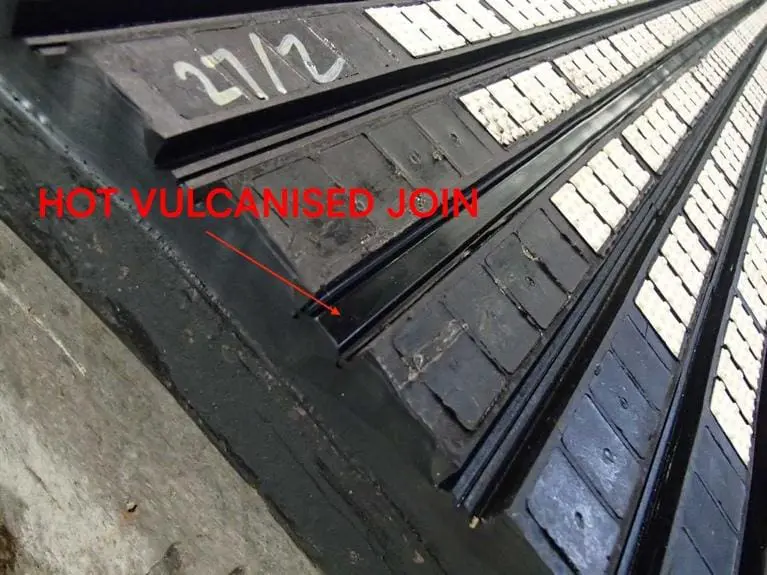
Le revêtement vulcanisé à chaud élimine les défaillances des joints et le décollement du revêtement qui en résulte ainsi que les dommages dus à la corrosion sur la coque de la poulie.
Pour de plus amples renseignements, contactez
David Molesworth
Elastotec Pty Ltd
Courriel : david@elastotec.com.au
Mobile: + 61 0423 200 178
Poulies en contact avec le côté porteur de la courroie
Les poulies en contact avec le côté porteur (sale) de la courroie ont un défi différent de toutes les autres p
Défaillance du couvercle inférieur de la bande transporteuse due aux galets tendeurs et aux poulies
Usure excessive du couvercle inférieur de la courroie résultant d'une mauvaise disposition du galet tendeur et de la poulie en céramique
Modèle théorique pour évaluer les effets de l'usure de la courroie sur la contrainte de calage
Overland Conveyor Company a été mandatée par Elastotec Pty Ltd pour développer un modèle théorique pour étudier