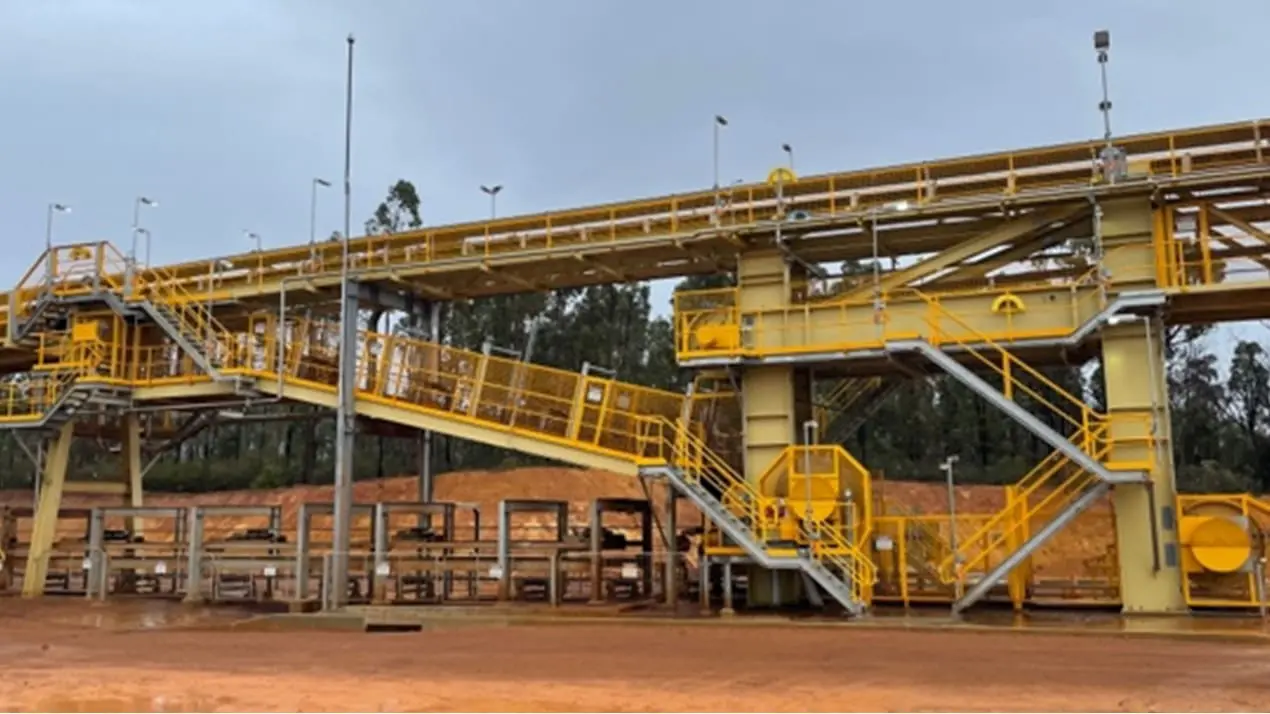
Hot Vulcanised Ceramic Lagging – the road to increased conveyor availability
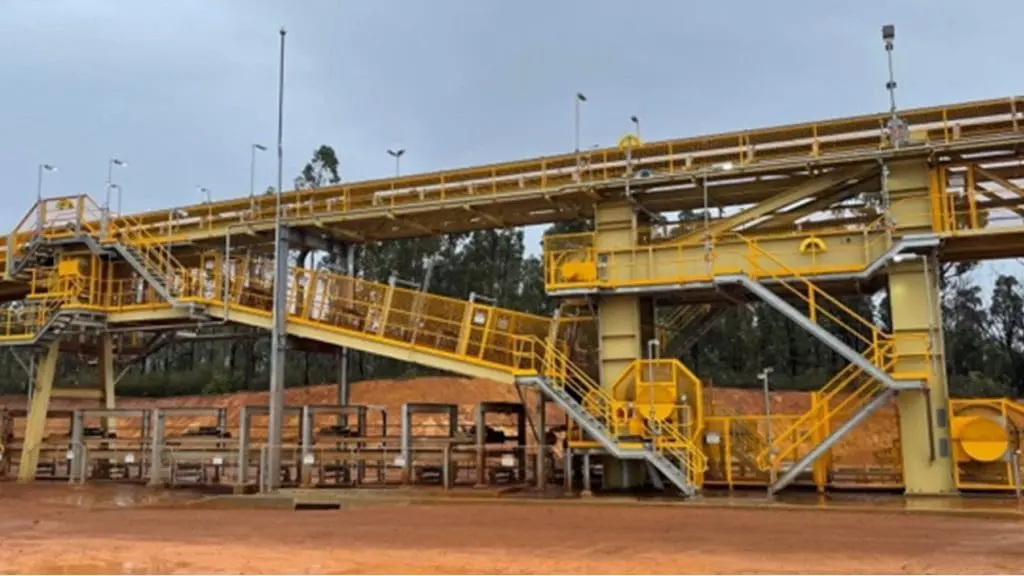
A large bauxite mine in Australia, running an overland conveyor with an ST3600 belt, 1050mm wide, has successfully introduced Hot Vulcanised Ceramic Pulley Lagging to one of its sites.
Why?
To address three critical production issues:
- Eliminate premature failure
- Increase conveyor availability
- Reduce production disruption on site

This mining company has historically used 12mm thick cold bond ceramic lagging on their conveyor pulleys.
However, production capacity demands mean the mining company will be upgrading from their current conveyor – 2400 tph to 3600 tph in the future. When the upgrade is complete, it will add a 2500 kw motor and increase the speed from 4.8 to 7.2m/s.
To ensure the increased production capacity is reliably achieved it is important to eliminate pulley failure due to lagging problems.
The challenge
Previously, cold bonded lagging used on pulleys has had recurrent failures, which caused disruption of production.
The following four failure modes have occurred multiple times:
- Debonding
- Edge lifting
- Separation at the joints resulting in premature corrosion on the pulley shell
- Tile loss resulting in loss of grip on drives and abrasion resistance
These failures translate into extra maintenance, extra downtime and less conveyor availability.
The Bauxite mine operates in wet conditions and cold bond lagging is affected by the opening of the joins, which results in water penetration through to the pulley shell. Bauxite is very abrasive and when mixed with caustic soda after the milling cycle, it becomes very corrosive.
The resulting corrosion of the pulley shell leads to debonding of the lagging and reduces the service life of the pulley.
The solution
PROK recommended the use of hot vulcanised ceramic lagging (HVCL) instead of cold bond ceramic lagging, as HVCL eliminates the four failure modes which occur with cold bond. HVCL provides a fully sealed protection of the pulley shell, preventing water penetration through the lagging joins and edges, which in turn eliminates lagging debonding and edge lifting.
Hot Vulcanised Ceramic Lagging process:
- HVCL is a composite of highly abrasion resistant 95% aluminium oxide tiles bonded into a rubber backing strip. HVCL guaranties no tile debonding.
- These strips are then applied to the pulley in a hot vulcanising process where the pulley is placed into an autoclave
- The lagging is cooked onto the pulley at 140°C under a pressure of 400kPa for 3 to 6 hours
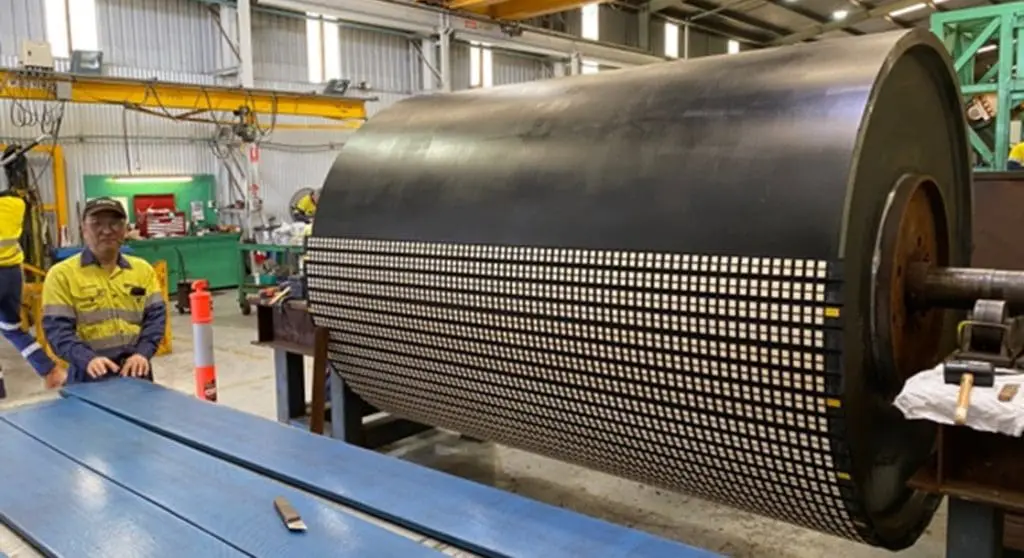
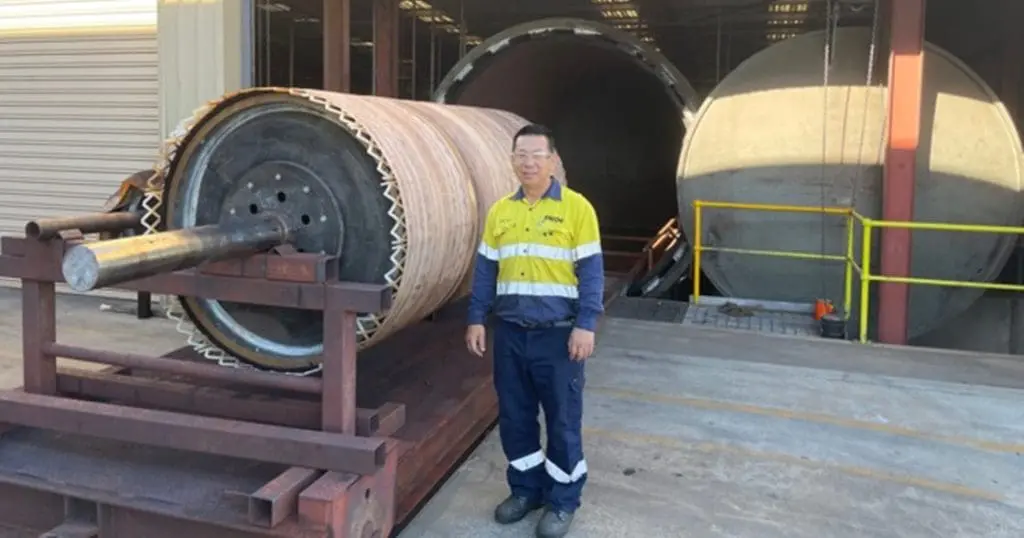
The HVCL process guarantees no tile loss due to debonding, a 100% rubber tear bond to the pulley which ensures there is no chance of the lagging debonding:
- Reducing maintenance
- Increasing conveyor availability
- Extended pulley service life and maximizing production output.
To find out more about how Elastotec Hot Vulcanised Ceramic Lagging can assist you with increased conveyor availability, please reach out to our team of experts.
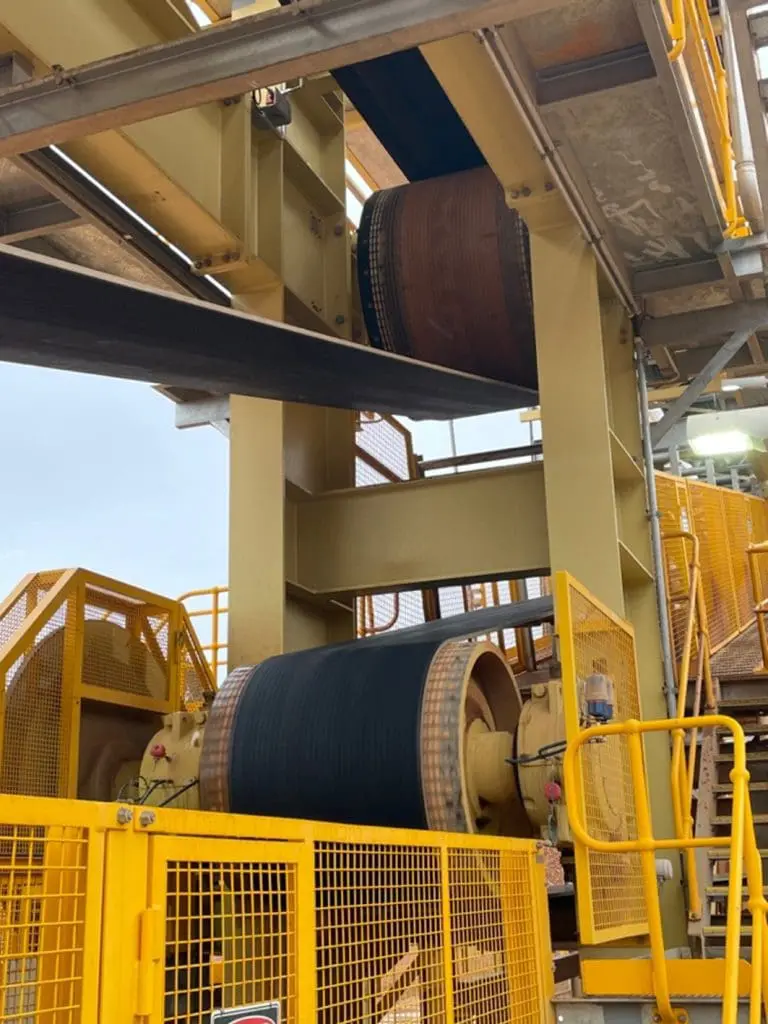
12mm Hot Vulcanised Ceramic Lagging
Large Gold Mine in Australia – increased service life of pulleys with Elastotec/PROK HVCL
One of the largest gold mines in Australia, located in southeast of Perth, produces around 750,000 o
T&T Perú 2023
Thank you to the Peruvian mining sector. Thank you for the space to discuss your challenges. Thank y
Prevention of blisters in steam heated autoclaves
This technical bulletin will outline the causes of blister formation and will detail a series of sim