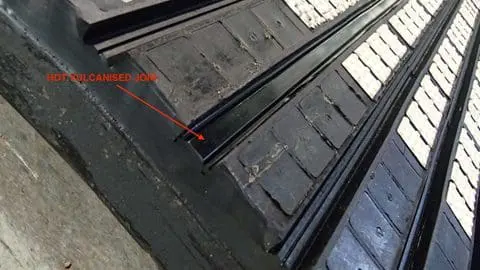
How to Maximise Your Pulley Lagging Service Life: Hot Vulcanised vs Cold Vulcanised Application

Overview
Mining technology is rapidly evolving to meet the challenges of extracting minerals in remote locations, often with extremes of weather and often from ore bodies located deep underground. To achieve production costs that are competitive and sustainable, a number of new technologies are being adopted by major mining companies. These include increasing use of automation and the use of high powered, gearless drive conveyors for their transportation requirements.
To maximise the effectiveness of these technologies, the reliability of the equipment becomes critical to ensure target production costs and production outputs are achieved. For conveyor pulleys, this has necessitated the use of pulley lagging that can handle the increased loads applied by high-power drive systems, extremes of temperature from -50°C to +75°C, and in many cases operation in extremely wet and corrosive environments.
Cost of lagging failure
Traditionally, many pulleys have been lagged with cold vulcanised bonding systems which were convenient to use and did not require the use of specialised equipment – effectively convenience was given priority over performance.
Today, the costs of conveyor downtime are enormous – for example, a conveyor transporting 12,000 tonnes/hour of ore, worth US$60.00/tonne, conveyor downtime costs the mining company US$720,000/hour.
For the past five years, Elastotec has collected data from our network of Approved Applicators on the modes of lagging failure that are seen on pulleys sent for refurbishment. Three of the most common modes of failure are:
- Debonding from the pulley shell.
- Edge lifting.
- Corrosion at the joints between lagging strips, leading to lagging debonding.
It has been well documented that cold vulcanised bonding of pulley lagging increases the likelihood of premature lagging failure due to debonding from the pulley shell, edge lifting, and corrosion of the shell at the joints between lagging strips. In many cases, these types of failures, require relagging on the conveyor, resulting in loss of production. Because the conditions for lagging on the conveyor are less than ideal, these problems often reoccur.
Three of the most common causes of failure with cold vulcanised bonding are:
1. Debonding of lagging from the pulley shell
Debonding from the pulley shell is a catastrophic failure that occurs most commonly on drive and high-tension bend pulleys; when the force applied to the lagging exceeds the adhesion strength of the bond between the lagging and the pulley shell. A common standard for cold vulcanised bonding is an adhesion of 9 N/mm – ideal conditions in factory application, with everything done correctly can provide adhesion from 9 to 15 N/mm. However, when lagging is cold vulcanised without OEM application procedures, or in poor conditions (on the conveyor), in many cases adhesion is below the standard of 9 N/mm.
All that is required for the lagging to debond is for the shear forces applied to the lagging to be greater than the adhesion of the lagging to the pulley shell.
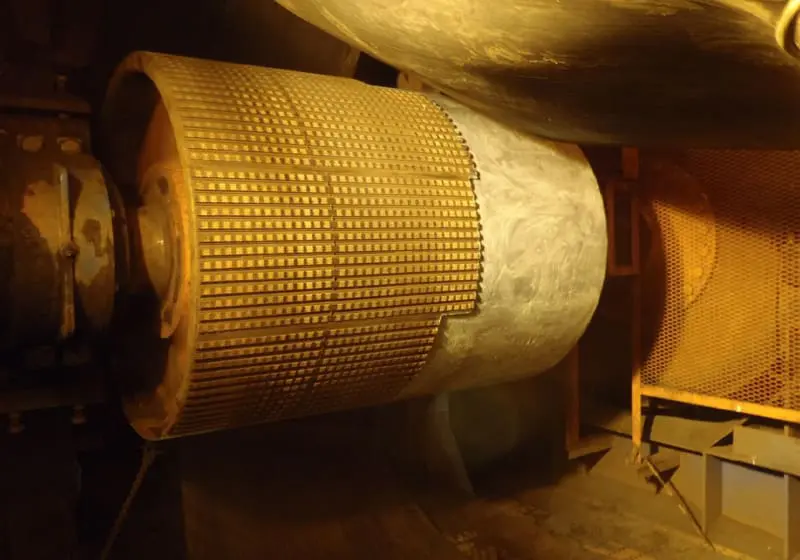
This type of debonding can also occur on non-drive pulleys – in particular high-tension bend pulleys. In many of these cases, the debonding that occurs is localised and not uniform across the
pulley face.
A number of factors combine to magnify the chance of a debonding failure – these include:
- The loads on pulley lagging are cyclic, and move from zero to full load multiple times a minute, dependent on the pulley rpm. This dynamic action is far more severe than an applied static load.
- Start up loads, particularly with a loaded conveyor belt, will be much higher than the normal running load.
- Low temperatures cause the rubber belt covers and the rubber component of any pulley lagging to become stiff and less flexible. The lower the temperature, the greater the extent to which this occurs. This loss of flexibility concentrates the applied loads on the weakest part of the cold vulcanised lagging – the bonding system.
Photos #2 and #3 show a pulley with cold vulcanised lagging that failed shortly after installation in operating conditions at -35°C. Note the raised rubber pips on the surface of the pulley are still intact and have not had time to be worn away.
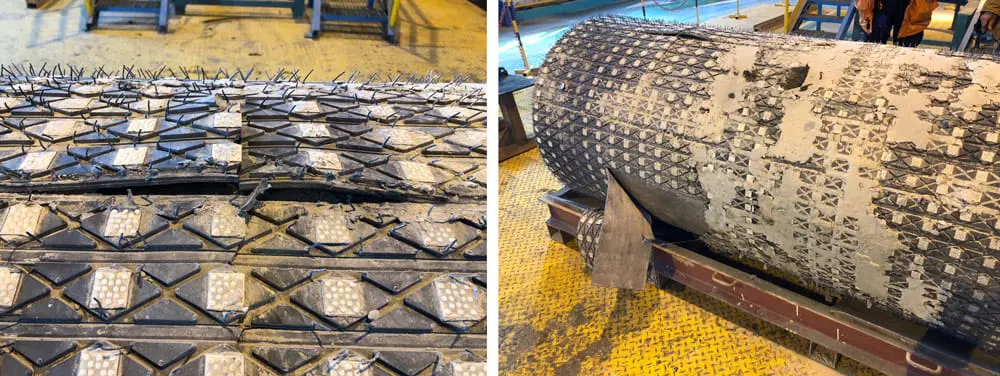
Many lagging applicators using the cold vulcanised application technique for applying pulley lagging do not measure the adhesion strength obtained on each pulley, and so have no idea as to the level of adhesion being achieved on each installation.
Elastotec Hot Vulcanised Ceramic Lagging (HVCL) provides a guaranteed 100% rubber tear bond between the lagging and the pulley shell that achieves 20-25 N/mm adhesion strengths – roughly double the very best adhesion that can be obtained through cold vulcanised lagging application under ideal conditions.
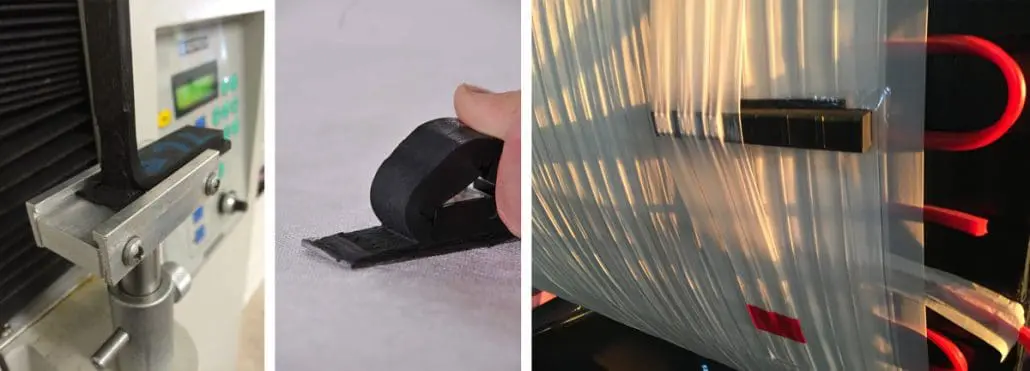
Photo #7 shows a common method of removing cold vulcanised lagging from the pulley shell by applying a load to the lagging at 90 degrees to the pulley.
For Elastotec Hot Vulcanised Ceramic Lagging, the bond is so strong that if this technique is tried the pulley can be lifted by the lagging or the lagging will tear – there is no debonding from the pulley shell.
With 100% rubber tear adhesion, debonding of the lagging from the pulley shell does not occur. Elastotec currently has more than 500 pulleys in the field with this bonding system, with a number of installations on conveyors running high-power gearless drives (up to 4,400 kW) and to date there have been no debonding failures.
Elastotec Hot Vulcanised Ceramic Lagging eliminates the chance of debonding from the pulley shell.

2. Edge Lifting
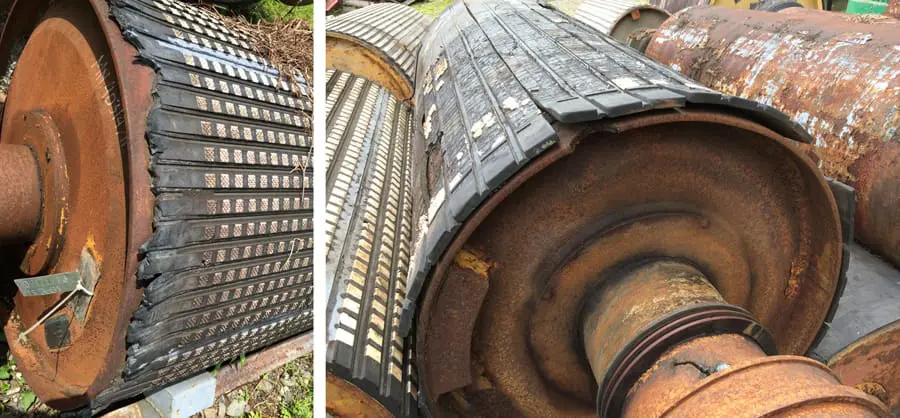
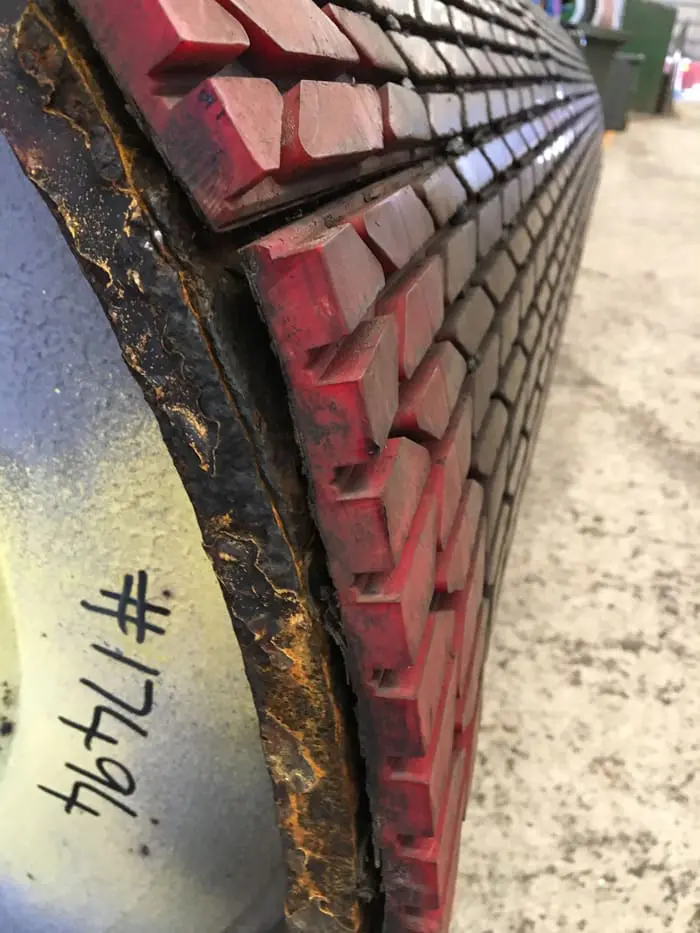
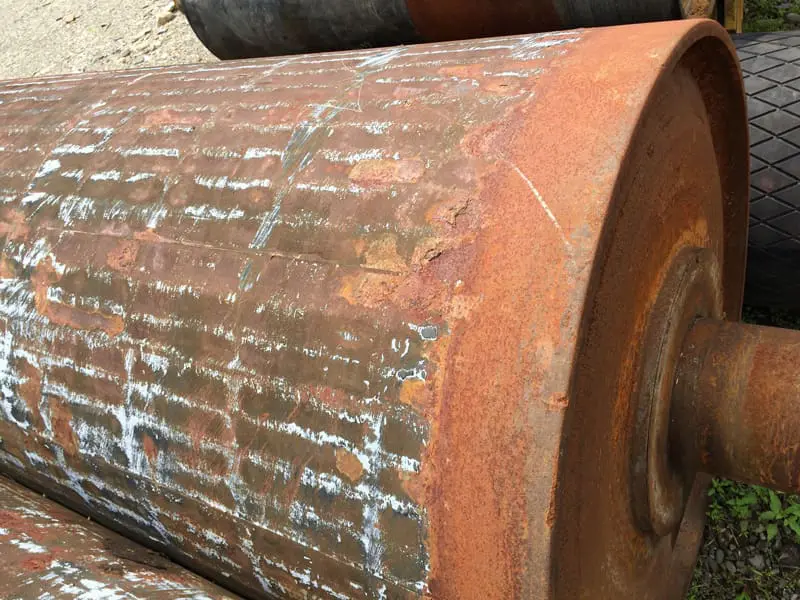
Photo #11 gives an indication of one of the mechanisms for this failure. The light grey pattern is where a layer of adhesive remains on the pulley shell after the lagging has been removed. This corresponds to recesses in the lagging profile. The areas that have no adhesive are the raised sections of the lagging which have been hammered down during the cold vulcanising application process.
This has resulted in greater contact and adhesion between the lagging and the pulley shell directly below the raised lagging areas, and lower contact and adhesion in the recessed lagging areas. When the pulley shell ends are exposed to wet conditions, the water is able to penetrate between the lagging and the pulley shell at the areas below the recessed lagging profile. Once shell corrosion begins, it quickly spreads around the shell end, the lagging lifts from the pulley shell, and is easily damaged (see photos below).
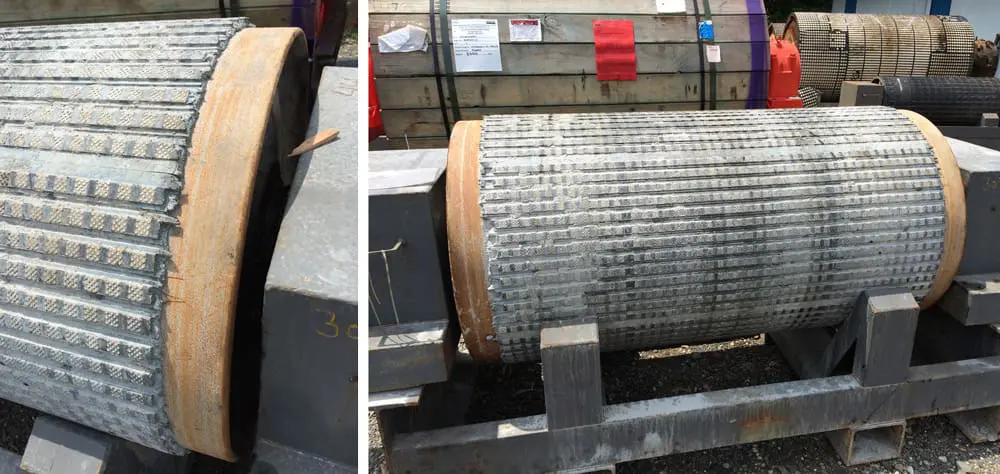
Photos #14 and #15 below show the results of operation at the same mine site of a pulley lagged with cold vulcanised ceramic lagging and one lagged with Elastotec Hot Vulcanised Ceramic Lagging. Both pulleys were installed at a large copper mine and operated in wet conditions where the water was acidic. There is corrosion evident on the end discs and locking elements of both pulleys. On the pulley with the cold vulcanised lagging there is severe edge lifting failure. The pulley with the Elastotec Hot Vulcanised Ceramic Lagging shows no sign of edge lifting and the lagging remains fully serviceable.
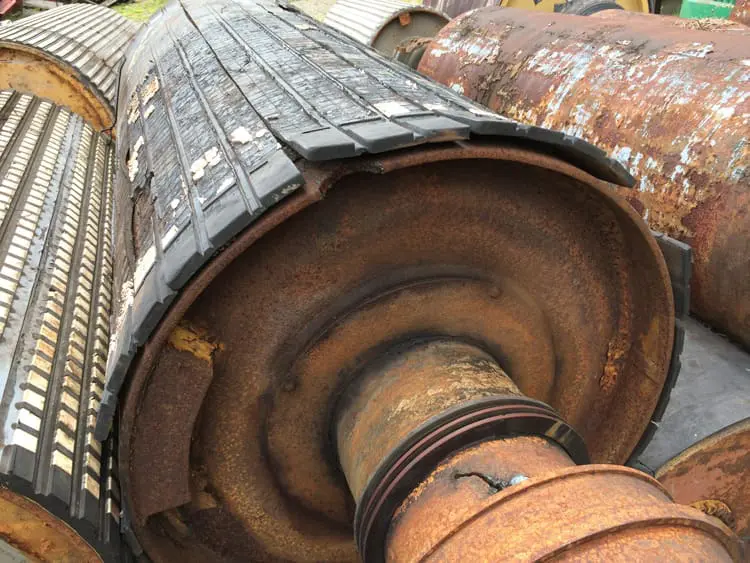
COLD VULCANISED APPLICATION
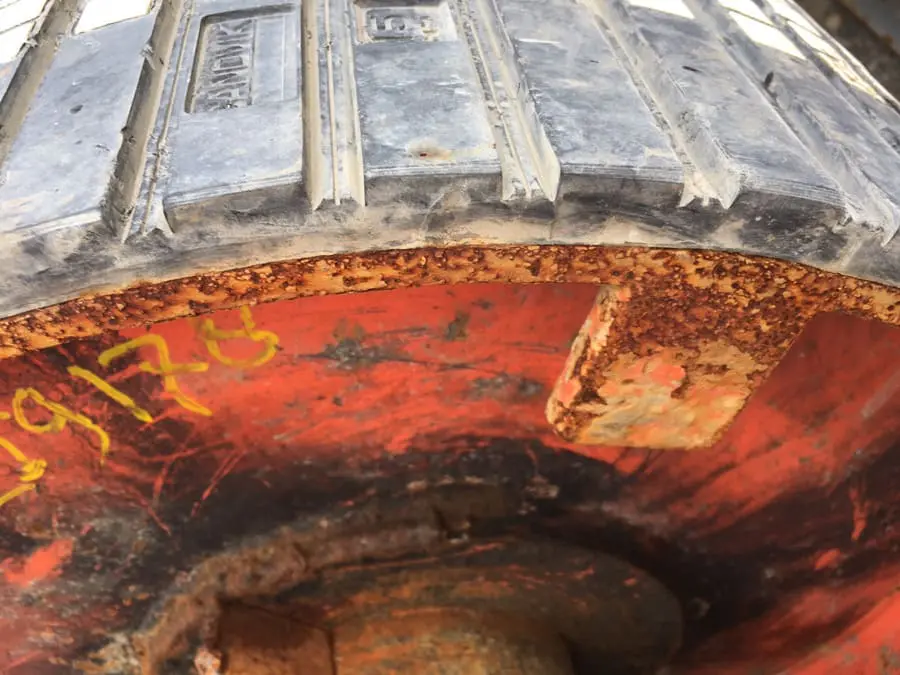
HOT VULCANISED APPLICATION
Elastotec Hot Vulcanised Ceramic Lagging eliminates the chance of lagging failure due to edge lifting.
3. Joint failure
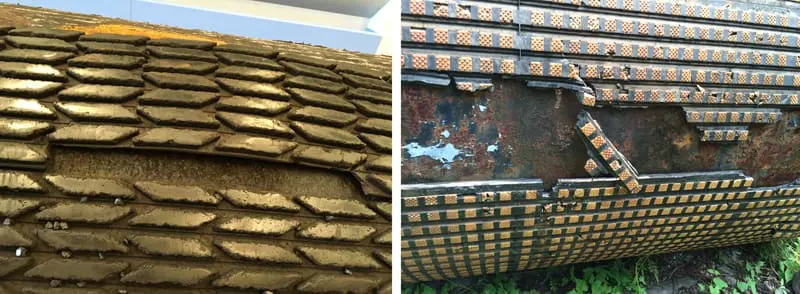
The joints between lagging strips are another weak point that regularly lead to lagging failure. There are two main contributors to joint failure with cold vulcanised lagging application:
- Application techniques and workmanship.
- Forces applied to the lagging joints by the belt during operation.
With regard to application techniques and workmanship, many lagging applicators use a technique called “butt” lagging where each lagging strip is ‘butted’ up against the previous strip. Depending on the skill and care of the operator, the result can vary from having no gap between strips to having a gap several millimetres wide (see photo #18). It is common for lagging applicators to use liquid sealants such as ‘Sikaflex’ to fill in gaps at the joins – the use of sealants to fill gaps will ensure lagging failure in wet conditions.
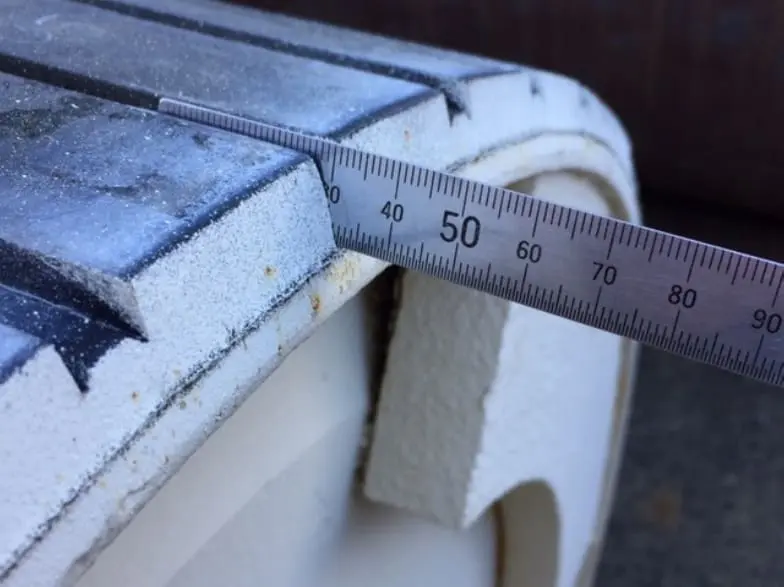
Even when the ‘butt’ application method is done perfectly, the sealing of the joint relies entirely on the cold vulcanised adhesive. When this method is used on pulleys with a ‘crown’, the lagging is stretched into place to close up the join. The resultant join has the lagging under tension with the lagging strips trying to pull away from one another. Eventually these joins will open up, allowing water to reach the pulley shell and corrosion to begin.
The ‘butt’ lagging method is commonly used because it is the quickest application method, and so gives the applicator the lowest cost. This low cost application method substantially compromises the lagging service life.
When we look at forces applied to the lagging joints by the belt during operation, we see that the belt applies a load to the lagging – the highest loads occur on drive pulleys and on high-tension bend pulleys. (See Fig#1.)
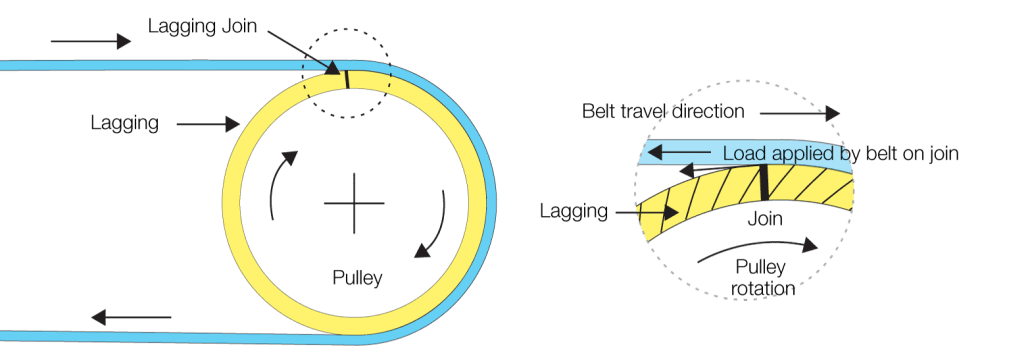
As the belt comes onto the pulley, these loads act in a way that wants to open up the joins between lagging strips. When the pulley is operating in a wet environment, this opening of the join, coupled with the hydraulic force generated by water caught between the belt and the pulley lagging, results in water reaching the pulley shell and causing corrosion. Eventually this corrosion leads to the debonding of the lagging along the joints – see photos #16 and #17.
For the corrosion failure at the joints between lagging strips, this can also result in additional, unnecessary expense when the depth of the corrosion reduces the shell thickness below what is required for the designed operating loads, and the pulley has to be scrapped.
See photo #19 and 20.
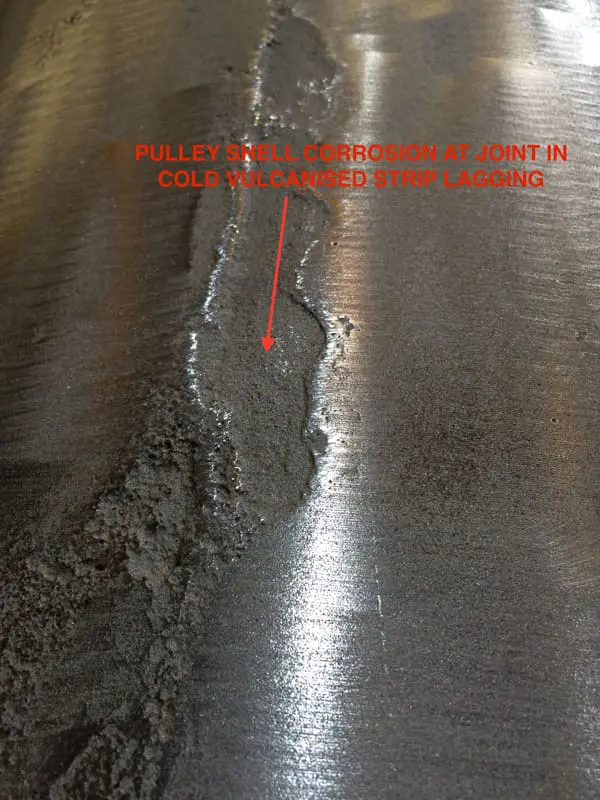
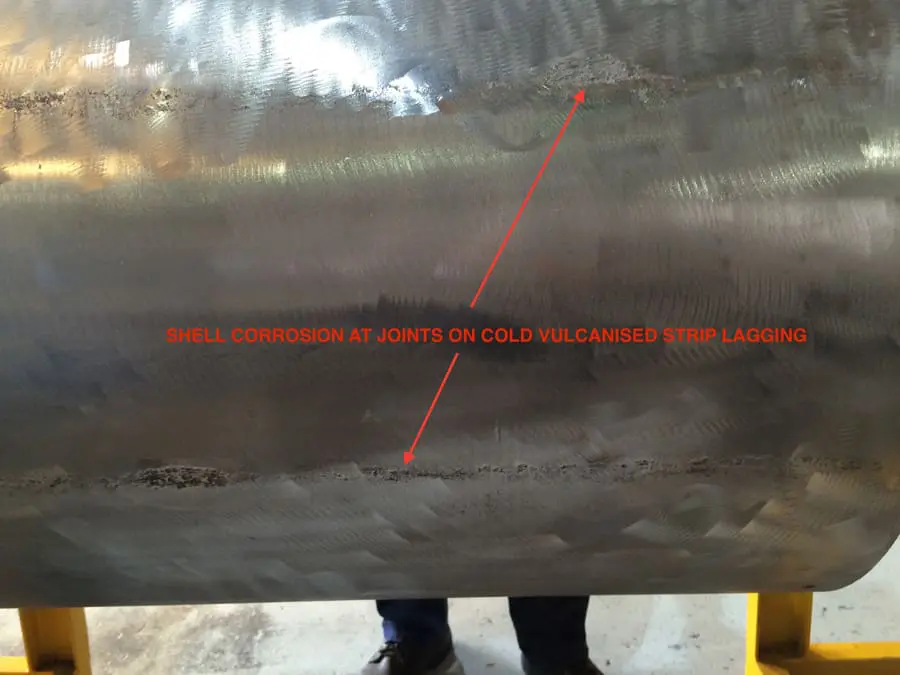
When Elastotec Hot Vulcanised Ceramic Lagging is applied to the pulley shell, there are no joints between the strips as the unvulcanised bonding layer along the edge of each strip fuses together to form a continuous lagging sheet, with no weak points between strips.
See Photos #21 and #22.
Elastotec Hot Vulcanised Lagging eliminates the chance of lagging failure at the joints between lagging strips.
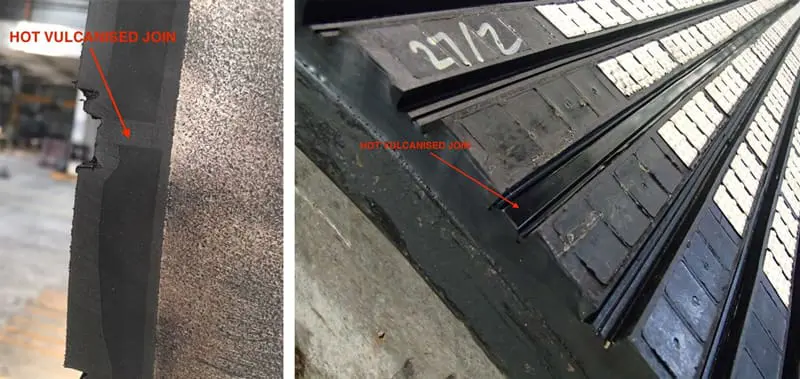
Hot vulcanised join completely sealed from the lagging surface to the pulley shell – no chance of separation or water penetration.
Additional performance considerations
To achieve reliable performance in all conditions, it is not sufficient to take lagging designed for cold vulcanised application and just apply an uncured bonding layer so that it can be hot vulcanised to the pulley. This is a compromise that carries significant risks.
These risks are:
- The rubber compounds used in the lagging have not been designed and tested to ensure they do not deteriorate during the hot vulcanised autoclave curing process.
- The bonding systems for the rubber/ceramic tile and rubber/PU insert adhesion have not been designed and tested to ensure they do not deteriorate during the hot vulcanised autoclave curing process.
- The bonding systems for ceramic tiles and polyurethane inserts have not been tested to ensure they can handle long-term outdoor exposure with no loss of adhesion.
- The bonding systems have not been tested to ensure they can handle the maximum cyclic loads that the lagging will be required to handle.
- All bonding systems can handle the maximum cyclic loads that the lagging will be applied to at the full range of operating temperatures.
In addition to having pulley lagging that is designed to eliminate or minimise the common lagging failure modes, the correct application techniques and checks are essential for the best result.
To facilitate this, Elastotec has developed detailed OEM Application Procedures for each different hot vulcanised lagging type. These procedures are focused on achieving the best possible lagging result. Included are detailed checklists for every part of the lagging application process, and culminate with a lagging adhesion test on every pulley.
The application of Elastotec Hot Vulcanised lagging is only done by Approved Applicators that have been trained by Elastotec. This allows the finished pulley lagging to be warranted by Elastotec – warranty details are available on request.
With a focus on providing the ‘longest service life’ possible for our lagging, Elastotec recommends the following:
Bonding System
Pulley | Elastotec Recommendation | Reason | Warranty |
---|---|---|---|
New pulleys | Hot Vulcanised Bonding | Eliminates three of the most common causes of lagging failure: – debonding from the pulley shell – edge lifting – separation, lifting and corrosion at the joints between lagging strips. | Elastotec warranty in place |
Refurbished pulleys | Hot Vulcanised Bonding | Eliminates three of the most common causes of lagging failure: – debonding from the pulley shell – edge lifting – separation, lifting and corrosion at the joints between lagging strips. | Elastotec warranty in place |
Pulley lagging repair on the conveyor | Cold Vulcanised Bonding | Only bonding system suitable for on site lagging application – emergency repairs only where pulley cannot be removed from the conveyor. | Not Applicable |
Lagging selection
Pulley | Elastotec Recommendation | Reason | Warranty |
---|---|---|---|
New pulleys | Hot Vulcanised Bonding | Elastotec warranty in place | |
Refurbished pulleys | Hot Vulcanised Bonding | Elastotec warranty in place | |
Pulley lagging repair on the conveyor | Cold Vulcanised Bonding | Not Applicable |
Important notes:
- Hot Vulcanised Bonding should be used when ever the pulley has been removed from the conveyor.
- Be cautious using Hot Vulcanised Ceramic or PU Lagging from suppliers that purchase Cold Vulcanised Lagging and then apply this to the pulley using their own Hot Vulcanising Techniques. Elastotec Hot Vulcanised Lagging uses rubber and PU compounds and tile bonding systems that are designed to handle autoclave curing with no degradation.
- Cold Vulcanised Bonding should only be used for emergency lagging repairs for pulleys on conveyors.
- Direct Bond Ceramic Lagging can be used for both Drive and Non-drive pulleys but requires detailed engineering analysis to ensure that there is no damage to the belt bottom cover and no debonding of the lagging due to flexing of the pulley shell. Contact Elastotec for specific design assistance.
- High tension pulleys require detailed evaluation of the operating conditions, belt condition, likelyhood of carry back etc. as any uneven tension across the pulley surface may accelerate lagging failure.
Large Gold Mine in Australia – increased service life of pulleys with Elastotec/PROK HVCL
One of the largest gold mines in Australia, located in southeast of Perth, produces around 750,000 o
T&T Perú 2023
Thank you to the Peruvian mining sector. Thank you for the space to discuss your challenges. Thank y
Prevention of blisters in steam heated autoclaves
This technical bulletin will outline the causes of blister formation and will detail a series of sim