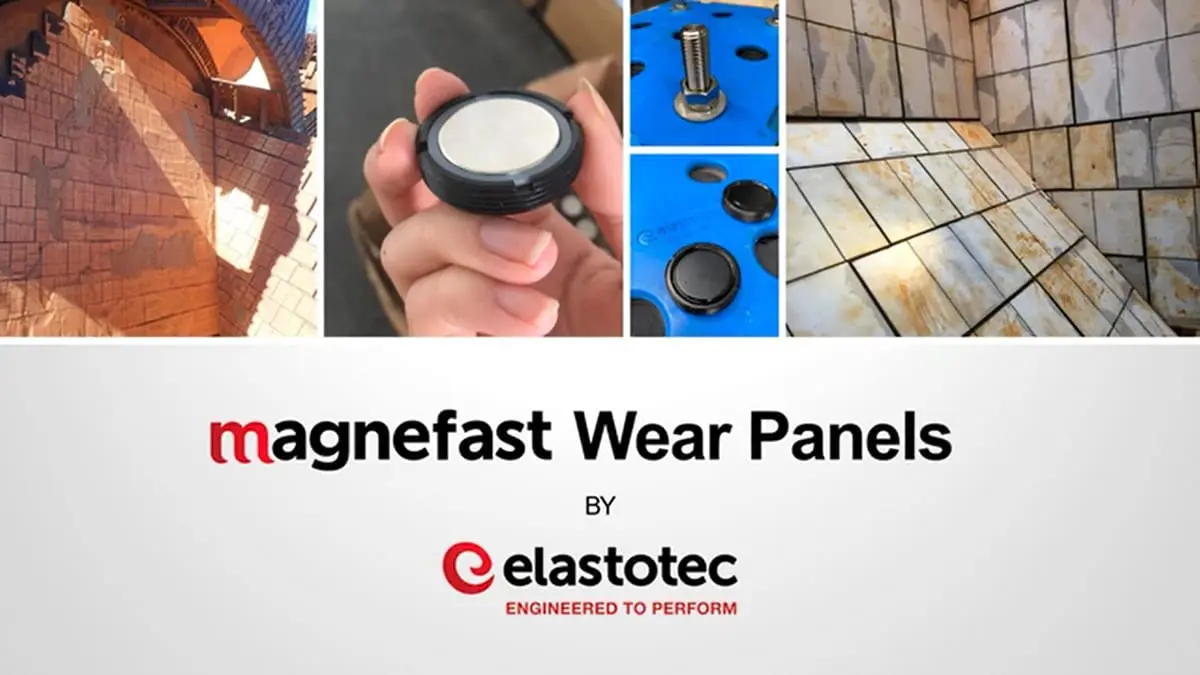
Introduction to Magnefast
Magnefast is a patented single sided attachment system for wear panels that uses high strength neodymium magnets to hold the panels in place.
Magnefast has been developed in Australia by Elastotec
Why use Magnefast?
There are a number of benefits from using Magnefast wear panels:
- Magnefast panels are Quick to install, replace, rotate
- Using Magnefast panels can increase your conveyor operating time. In a recent direct comparison where studded steel liners were replaced with Magnefast Ceramic Wear Liners the total install/removal time reduced from 35 hours of down time to 7 hours – a saving of 28 hours that can be available for conveyor operation.
- Magnefast panels are designed for applications where access to the back of the wear surface is difficult
There are a number of OH & S benefits that result in reduced risk when using Magnefast panels:
- Only simple tools are required to remove/install Magnefast (no electrical, hydraulic or pneumatic tools are required)
- Single sided application when using Magnefast panels means there is no requirement for working at height outside the chute.
- Risks associated with drop from height for tools, nuts, bolts etc are eliminated
- Reduced weight makes handling easier and lowers the risk of strain injuries
One final benefit from the Magnefast single sided attachment is that the Wear Panels do not require gaps to be left to allow for stud/hole alignment. When installed there are no gaps between Magnefast Wear Panels – this provides improved wear performance.
Within the video we show you how the Magnefast Wear Panel system works.
The Magnefast Wear Panel system can be applied to:
- Steel or Ceramic Wear Panels
- Magnefast is available in a range of wear material thicknesses and can be manufactured as a kit with panels cut to suit your chute design
- Magnets have been engineered to operate up to 120 C in all weather conditions and the standard magnet holding force is more than 50 kg/magnet
- The Magnefast panel design allows the magnet location and strength can be varied according to end use requirements
- Stainless steel stud fixing is available where mechanical fastening is required
There are a number of chute installations with Magnefast Wear Panels that have been in service for over 12 months – these include a large iron ore export facility and the Springvale colliery located just outside Lithgow.
The iron ore export facility is one of the world’s largest bulk export ports. This port handles shipments of iron ore, lithium concentrates and salt. In October 2019 a trial installation of the Elastotec Magnefast ceramic wear panels was put in place. In December 2020 the existing studded steel wear liners were replaced with Magnefast ceramic wear liners. The Magnefast Ceramic Liners were individually numbered and were supplied as a kit. The Magnefast Ceramic Liners were individually numbered and were supplied as a kit.
A second installation has been in service for over 12 months at the Springvale colliery on a transfer chute diverter flap. In this installation coal can be diverted to two separate conveyors by mechanical diverter. Magnefast ceramic panels were chosen for this application because the diverter flap had just been replaced due to wear and it was difficult to fit studded wear liners. The Magnefast installation time for all panels, excluding set up was 45 minutes. Inspection after 12 months service showed no visible signs of wear in the panels
Magnefast Wear Panels provide an opportunity to
- reduce conveyor down time,
- increase production out put
- reduce OH & S risk
For more information please contact us.
Reduce maintenance time
80% less replacement time with Magnefast. Increase conveyor operating time. Do more during shutdown.
Large Quarry – Train Loadout Deflector
Located in southwest of Sydney this hard rock quarry can produce up to 5 million tonnes per annum of
Magnefast is safe
Keep your staff safe with no external scaffolding, no electrical, hydraulic or pneumatic tools - no