
Lagging Selection – One of the 4 Pillars of Lagging Performance
Lagging can be of good quality and application can be correct, but pulley lagging can still fail and does. Everything seems right but the lagging still doesn’t perform to expectations.
So why does this happen?
It’s because the pulley lagging selection is not right for the application.
What contributes to poor lagging performance?
- Lack of understanding of pulley application requirements.
- Failure to understand conveyor system requirements I.E. Spare pulleys that can be used in multiple conveyor locations.
- Lack of understanding of lagging engineering and lagging types available.
- Failure to understand lagging application methods.
- Resistance from mine company staff to change lagging from existing specification/drawing requirements.


Imagine the consequences of making the wrong lagging selection that results in the lagging not lasting as long as the bearings and locking elements.

Understanding the pulley operation takes time and specialist experience. It’s important to dig deepper to fully understand the application requirements.
At Elastotec we do take the time with our customers to ensure the right lagging selection. We achieve this by factoring in the the conveyor system, past lagging performances, pulley operating conditions and the various locations in the conveyor that spare pulleys may have to operate in.
The best outcome is when your experience in the field and the understanding of the everyday conveyor operation is combined with our lagging engineering expertise.
Dig deeper

Your conveyor operation/ maintenance expertise
Elastotec Lagging expertise
Better lagging performance
The team at Elastotec would like to work with you to ensure you have the correct pulley lagging selection. We have developed a number of tools to assist in evaluating individual pulley requirements, and to help narrow the choice of the best lagging for each application.
These include:
1.
Lagging operation checklist.
To check what conditions is the lagging operating at? Temperature, tension, belt cover condition, presence of carryback, wrap angle, type of belt, type of belt splices, build-up on the pulleys.
It also is important to understand what type of lagging has been used before and how did each lagging type perform.
2.
Lagging Analyst.
To calculate T1/T2 ratio and risk of localised slippage with belt retraction.

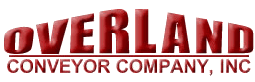
3.
Lagging performance envelopes.
Lagging Performance Envelopes calculate if the shear and normal stresses that the conveyor performance will impart on the lagging, are higher than what the lagging is designed to operate with. This tool helps reduce the risk of catastrophic lagging failure by identifying when lagging operational limits are being reached.
At Elastotec we believe lagging solutions should cover each and every one of the Four Pillars of Lagging Performance.
Selecting the correct lagging for the application is one of the most important.
Lagging Selection related case studies:
Large Gold Mine in Australia – increased service life of pulleys with Elastotec/PROK HVCL
One of the largest gold mines in Australia, located in southeast of Perth, produces around 750,000 o
T&T Perú 2023
Thank you to the Peruvian mining sector. Thank you for the space to discuss your challenges. Thank y
Prevention of blisters in steam heated autoclaves
This technical bulletin will outline the causes of blister formation and will detail a series of sim