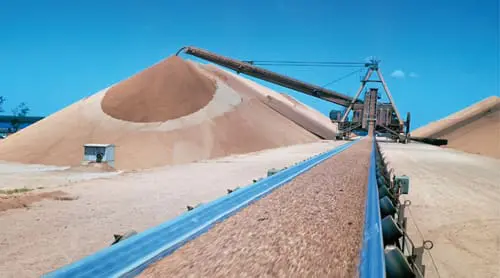
New Technology Improves Service Life of Ceramic Pulley Lagging
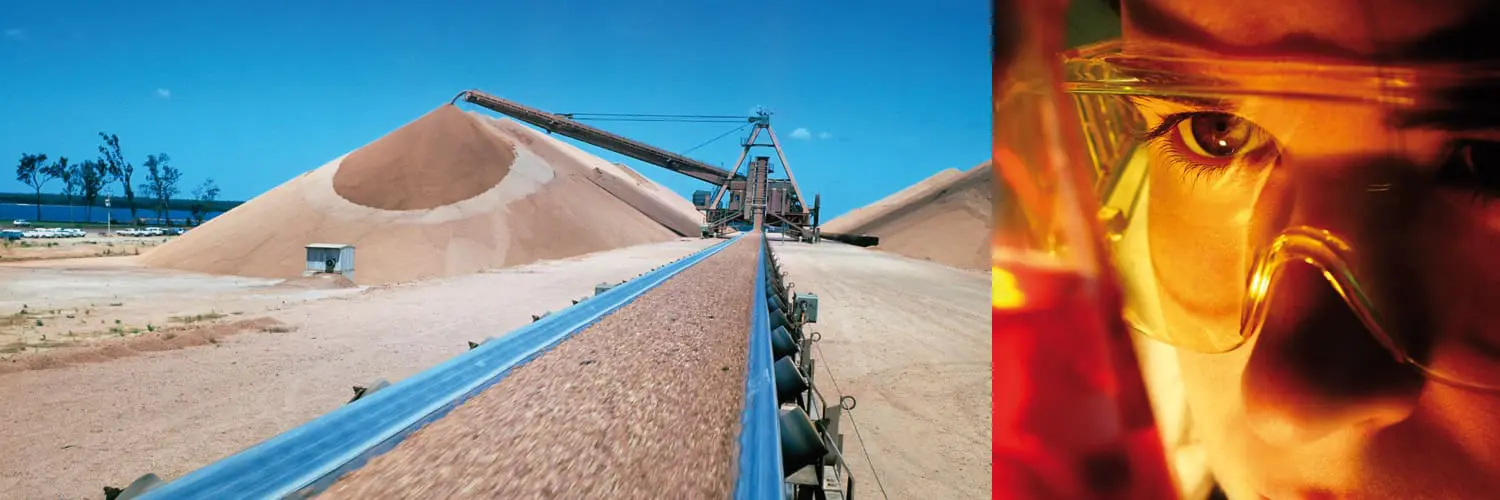
Elastotec has developed an innovative ceramic pulley lagging system with superior bond strength and outstanding durability, eradicating traditional issues associated with ceramic lagging and making it a unique offering in the market.
Ceramic pulley lagging is ideal for pulley applications that require increased wear resistance, as well as increased levels of drive. Capable of delivering an extended service life of more than 10 years, Elastotec’s ceramic pulley lagging system is significantly more cost-effective than rubber lagging over the long term. Through extensive research and development, Elastotec has addressed the common causes of failure for ceramic pulley lagging, including:- debonding of the lagging from the pulley shell
- ceramic tile loss due to tile pullout
- ceramic tile loss due to tile cracking/fracture
Debonding of ceramic lagging
Until recently, ceramic lagging was applied to pulleys using two-part neoprene contact cements in a process generally known as ‘cold bonding’. Although this is a convenient system there are a number of limitations that can adversely impact the reliability and service life of the ceramic lagging, including
- Bond strength between the rubber backing on the ceramic lagging and the steel pulley shell is limited and it does not achieve a 100% rubber tear bond. A generally accepted minimum bond strength for lagging adhesion in the conveyor industry is 9 kN/m – this is well below the level required for a 100% rubber tear bond. 100% rubber tear is where the bond strength is greater than the rubber, causing the test samples to fail in the rubber and leaving rubber adhered to the substrate
- In an application with a high tension belt, where the shear forces applied by the pulley to the conveyor belt exceed the bond strength between the ceramic lagging and the pulley shell, the lagging can be ripped off the pulley shell (see Image#1).
Graph#1 illustrates how increased belt tension at the drive pulley increases the required lagging bond strengths, which can be well above the adhesion value of 9 kN/m, currently used as a requirement for cold bonded ceramic lagging.
Other considerations when using cold bonded lagging systems include:
- Bond strength can be adversely affected by moisture during application. High humidity during application of cold bonding adhesives can reduce the final bond strength by as much as 50%.
- The application of ceramic lagging using cold bonding adhesives relies on the skill of the operator and the method of application being used.
- Ceramic lagging applied with cold bonding adhesives has multiple joins between the lagging strips. These joins are a weak point that often allows water to pass through to the pulley shell and cause shell corrosion. In the worst case scenario, this can lead to failure of the bond from the edge of the lagging strip, with the resultant lagging failure. For pulleys that are being refurbished, the shell corrosion may require machining of the shell with the resulting loss of shell thickness requiring a de-rating of the pulley service load or, in the worst case, scrapping of the pulley.
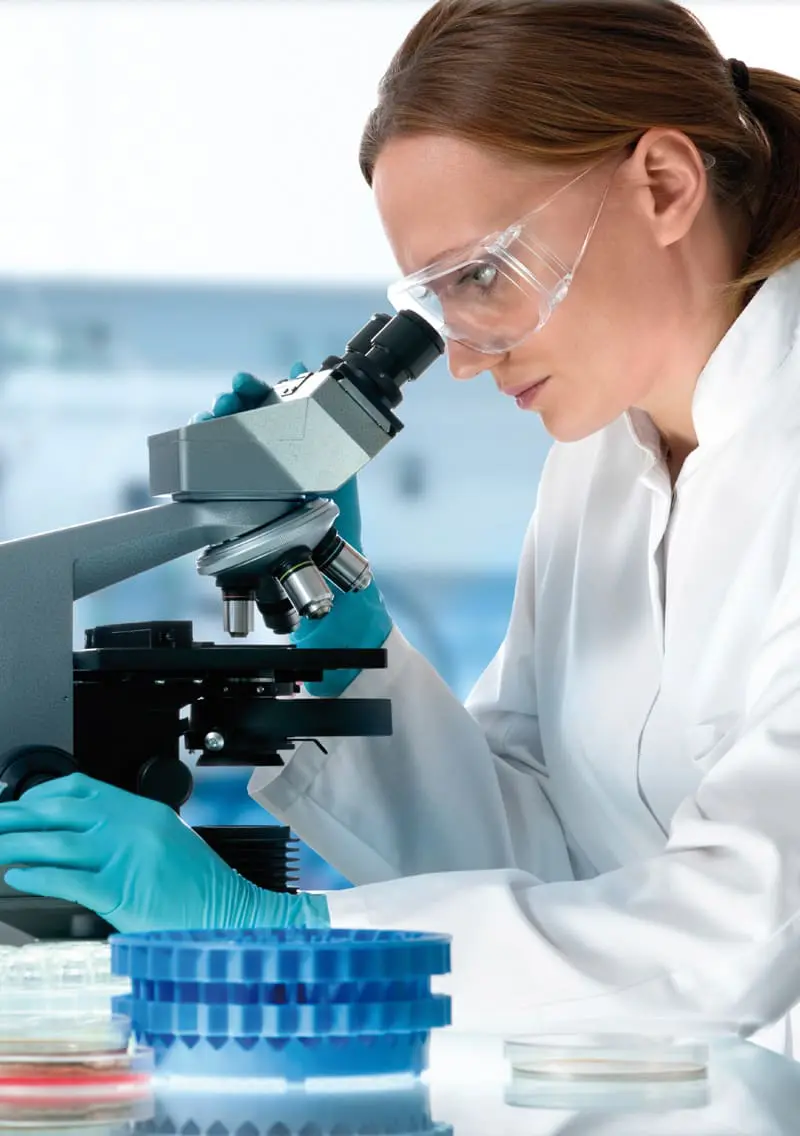
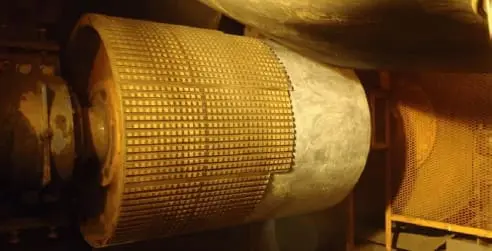
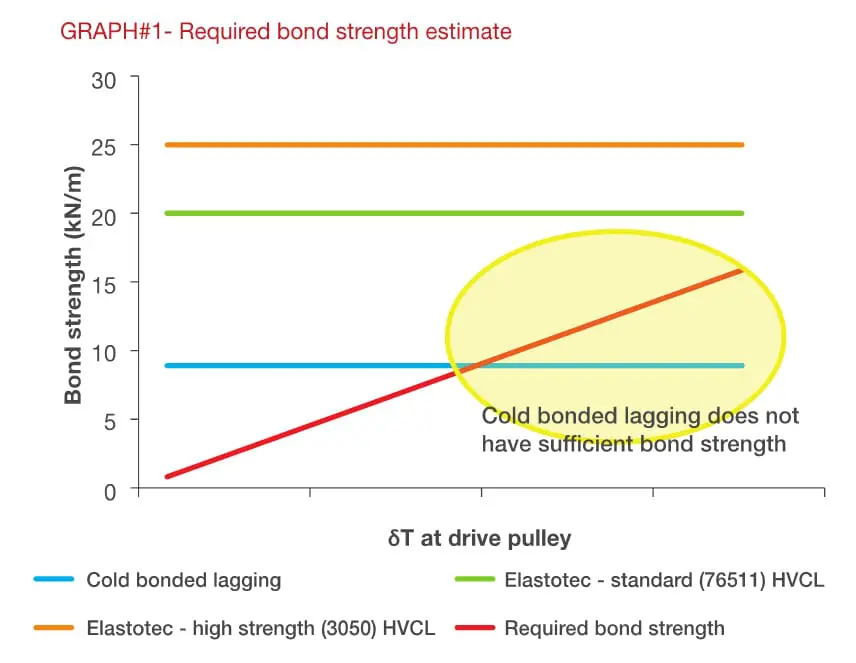
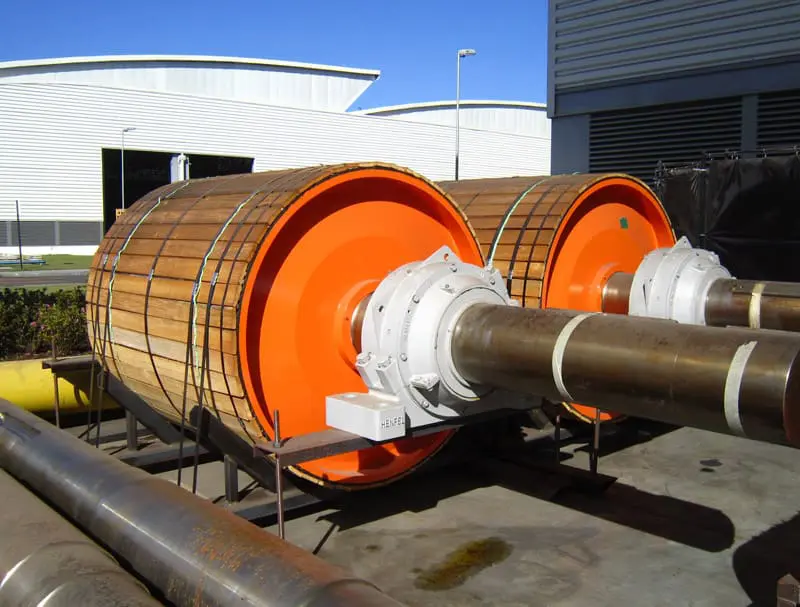
Ceramic tile bond failure
There are a number of causes of ceramic tile bond failure, including the following:
- Common primer and adhesive systems that are used by most manufacturers of ceramic lagging provide a good initial bond when applied at the specified coating weight, but field experience attests to bond failure as service time extends. Laboratory testing has also identified that some bonding systems deteriorate with exposure to moisture
- An effective bond between ceramic tiles and rubber requires a minimum coating weight of primer and adhesive. A number of ceramic lagging manufacturers apply primer and adhesive using a spray application, making it difficult to ensure that the required minimum primer/adhesive coating weight is obtained on all tile surfaces and leading to tile/rubber bond failures.
- Lagging design that only bond the ceramic tile on the back of the tile results in less of the tile surface area bonded, leaving the edge of the tile exposed as a potential weak point for bond failure (see Image#2).
- Bond strengths between the ceramic tile and the rubber backing have been lower than the applied shear forces from high tension conveyor belts, resulting in tile pull out.
Ceramic tile cracking
Tile cracking leads to tile loss and may lead to premature failure of the ceramic lagging, with a number of causes leading to this issue:
- Lagging design that has the ceramic tiles butted up against one another can result in cracking from impact between the tiles when subjected to shock loads, which can occur when material becomes caught between the conveyor belt and the ceramic lagging (see Image#3).
- Poor quality aluminium oxide tiles are prone to cracking and breakage/wear of the raised dimples. Eighty percent of the raw material cost of ceramic lagging is the aluminium oxide tiles and this offers the largest potential cost saving for manufacturers of lower cost ceramic lagging. Unfortunately, reducing the quality of the aluminium oxide tiles has a direct impact on the ceramic lagging performance.
- With the increase in aluminium oxide content, the vickers hardness, wear resistance and flex cracking resistance also increase. The tile cost also increases with aluminium oxide content (refer Table#2 below).
Table #2 – Al₂O₃ Properties
MATERIAL | UNITS | Al2O2 | Al2O2 | HVCL Al2O2 |
---|---|---|---|---|
85% | 92% | 96% | ||
Vickers Hardness | (Hv 10) | 600-800 | 1000-1100 | 1200-1300 |
Impact Resistance | (MPa m1/2) | 2.5 | 3.3 | 4.1 |
20x20x5 Tile Cost | ($US/pc) | $0.04 | $0.08 | $0.16 |
Tile Cost Increase | +200% | +200% |
DEVELOPMENT OF HOT VULCANISED CERAMIC PULLEY LAGGING
Elastotec is a well-regarded specialist manufacturer of pulley lagging and has developed a hot vulcanised ceramic lagging (HVCL) system to meet the requirements of PROK – a manufacturer of bulk materials handling equipment. This collaboration has resulted in a quality ceramic lagging system with increased reliability and an extended service life.
1.) LAGGING TO PULLEY ADHESION
Hot vulcanised application
Hot vulcanised rubber lagging is generally recognised as providing a number of advantages over pre-cured rubber sheets that are cold bonded to the steel pulley. The main advantage is the bond strength between the rubber and the pulley shell is significantly higher for hot vulcanised lagging. The second, often overlooked, advantage is that there is no join in the lagging when the rubber has been hot vulcanised. Using cold bonded lagging these joins can provide a starting point for shell corrosion, allowing the rubber to lift and be torn from the pulley.
A process for installing ceramic lagging using hot vulcanising has been developed and is available as PROK Hot Vulcanised Ceramic Lagging (HVCL). This solves any issues with lagging to shell bonding, providing a stronger and more reliable connection between not only the lagging and the pulley, but also, importantly, between the individual lagging strips. HVCL ensures a 100% rubber tear bond between the lagging and the pulley shell, resulting in considerably higher adhesion strength (refer to Table#3).
The HVCL is the subject of a current Australian patent application.
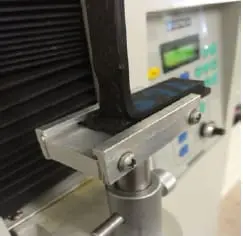
Table #3 – Adhesion Testing Hot Vulcanised Ceramic Lagging/Mild Steel
RUBBER COMPOUND | RUBBER TENSILE STRENGTH (MPa) | BONDING SYSTEM | ADHESION 90 DEGREE PEEL (kN/m) | |
---|---|---|---|---|
Conventional Rubber Backed Ceramic Lagging | 76511 | 15.0 min | COLD | 5.0 – 15.0 |
Elastotec HVCL (Standard) | 76511 | 15.0 min | HOT | 20.0 min |
Elastotec HVCL (High Strength Rubber) | 3050 | 30.0 min | HOT | 25.0 min |
Removal of joins
An additional significant advantage of HVCL is that there are no joins between the ceramic lagging strips (see image#5). When HVCL is vulcanised the uncured rubber at the edges of the lagging flows together and vulcanises to form a continuous layer that is strong and also impervious to water, preventing shell corrosion. This removes the potential weak points where the joins meet, which can lead to failure of the ceramic lagging.
Application of HVCL
HVCL is installed using a tightly controlled high pressure autoclave process, at elevated temperature and with skilled operators working in a factory environment, ensuring a reliable and consistent result.
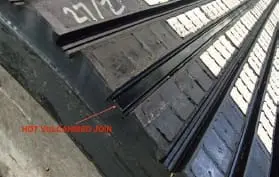
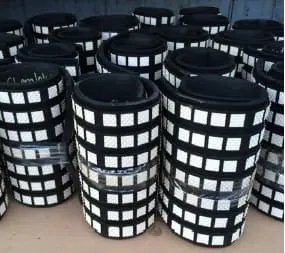
2.) CERAMIC TILE BOND FAILURE
Tile adhesion testing
Elastotec has undertaken extensive outdoor testing of ceramic/rubber bonds and has found that a number of primer/adhesive systems recommended by adhesive suppliers, provide bonds that initially offer rubber tear adhesion but, on prolonged exposure to moisture and UV, rapidly deteriorate.
Elastotec checks the integrity of the bonds throughout the outdoor testing process, where the tile/rubber bond is under constant stress. The testing is done by bending a strip of ceramic lagging into a tight circle, with the ceramic tiles on the outside of the circle. The sample is then held in this position during the outdoor exposure period. The results are recorded at regular intervals and have been used to identify the optimum primer/adhesive system for long-term adhesion performance (see Table#4).
Table #4 – Outdoor Ageing Tile Bond Testing
* Row in YELLOW background indicates Adhesive/primer system used for the Elastotec/PROK HVCL.
Bond After Ageing | |||||||||||||
Primer | Adhesive | Initial Bond as Manufactured | 1 Month | 2 Month | 3 Month | 4 Month | 5 Month | 3 Years | |||||
A1 | B1 | 0% | 25% | 27% | 27% | 29% | 29% | 29% | |||||
A1 | B2 | 0% | 33% | 39% | 42% | 43% | 43% | 45% | |||||
A2 | B1 | 0% | 0% | 1% | 1% | 1% | 1% | 1% | |||||
A2 | B2 | 0% | 10% | 19% | 26% | 30% | 33% | 36% | |||||
A3 | B1 | 0% | 0% | 0% | 0% | 0% | 0% | 0% | |||||
A3 | B2 | 0% | 0% | 0% | 0% | 0% | 0% | 0% | |||||
– | B2 | 1% | 6% | 9% | 11% | 14% | 16% | 17% | |||||
A4 | B1 | 0% | 0% | 0% | 0% | 0% | 0% | 0% | |||||
A4 | B2 | 0% | 0% | 0% | 0% | 0% | 0% | 0% |
Additional testing has been carried out to increase the adhesion strength between the rubber backing and the aluminium oxide tiles, as well as the steel for the pulley shell. This testing was undertaken using the tension pull method – (see Image#7 and Table#5)
Based on the results of the Outdoor Ageing Tile Bond Testing, the Tension Pull Adhesion Testing and production considerations the adhesive system of Primer A3 and Adhesive B2 was selected for HVCL, as this provided the best performance.
Importantly, the testing program has identified improvements in the ceramic/rubber bond strength, as well as eliminating the deterioration in bond strength due to moisture and UV exposure. This technology is an important and unique component of the HVCL product.
Tile coating – primer and adhesive
Elastotec uses a proprietary dipping process for the coating of the ceramic tiles with primer and adhesive, which ensures that all tile surfaces receive the necessary minimum coating weight of primer and adhesive. To date, more than 5,000,000 tiles have been coated using this method and there have been no reported bond failures.
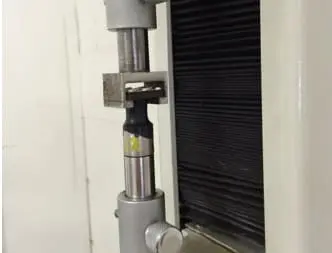
Table #5 – Tile Adhesion Testing – Tension Pull
Primer | Adhesive | Tension Pull | Failure Mode |
---|---|---|---|
(MPa) | |||
A3 | B1 | 4.31 | 90% R |
A3 | B2 | 6.87 | 100% R |
A4 | B1 | 6.42 | 100% R |
A4 | B2 | 3.26 | 50% $ |
3.) CERAMIC TILE CRACKING
Lagging design
The unique design of HVCL ensures that tiles are bonded with rubber on both sides and back, providing a more reliable layer of protection from impact and significantly reducing the risk of tile cracking.
An additional benefit of the lagging design is the increased area for bonding between the tile and the rubber. For typical 20 x 20mm-sized ceramic tiles used by many ceramic lagging manufacturers the bonding areas are:
- Tile bonding back only 400 mm2/tile
- Tile bonding back and sides 720 mm2/tile
This is an 80% increase in bonding area, resulting in increased force required to pull the tiles from the rubber.
Aluminium oxide tile quality
The key properties of ceramic tiles in terms of performance of ceramic lagging include vickers hardness, impact resistance and abrasion resistance. These properties are specified and checked for each production batch of tiles to ensure a consistent performance. Table 2 lists the properties of the 96% aluminium oxide tiles used in HVCL, with the 96% aluminium oxide tiles demonstrating high hardness and impact resistance, resulting in increased levels of abrasion resistance and longer life than obtained with lower grades.
Hot vulcanised ceramic lagging
Hot vulcanised ceramic lagging is the result of a coordinated research and development program over two years, with the combined resources of Elastotec and PROK. It represents a significant milestone in ceramic lagging technology available to bulk materials handling operators.
Wade Guelfi, General Manager Asia Pacific for PROK Conveyor Components, says:
Cold bonded systems from other suppliers are really only a solution when applying lagging in the field. Performance wise they compromise bond strength for convenience. We now have over 100 pulleys in the field, with the PROK HVCL in a range of applications and the results have been excellent.
For new build and factory re-build pulleys with rubber backed ceramic lagging we recommend the PROK Hot Vulcanised Ceramic Lagging because of the superior bond strength and durability of this product.
Prevention of blisters in steam heated autoclaves
This technical bulletin will outline the causes of blister formation and will detail a series of sim
Elastotec Expands Lagging Operations
Our dedicated teams in Australia and Vietnam working really hard to understand lagging performance,