Description
Application
Elastotec Extreme 42% Ceramic Lagging is designed for use in the following demanding applications:
- Large drive and non-drive pulleys on high power belt conveyors that are in contact with the clean side of the belt. This includes gearless drive conveyors of all power ratings.
- Pulley in locations that are difficult to access and where pulley change out is difficult.
- Critical locations where unplanned conveyor down time due to lagging failure must be eliminated.
- Conveyors that operate across a wide temperature range.
- Conveyors that operate in wet conditions.
Key features and benefits
- Proven Hot Vulcanised bonding system to provide 100% rubber tear adhesion to the pulley shell. This bonding system eliminates the chance of the lagging debonding from the pulley shell, edge lifting and the chance of separation of the lagging of the joins between strips.
- 60 Shore A rubber backing developed in conjunction with ARDL (Akron Rubber Development Laboratory) to handle hot vulcanised application without degradation, retain flexibility at low temperature (-40°C) and to also have excellent resistance to outdoor ageing.
- Proven bonding system between the aluminium oxide tiles and the backing rubber. Elastotec has run long term ageing tests since 2012 and based on these text results and field service of over 700 pulleys, provides a guarantee that there will no debonding of tiles from Elastotec Extreme 42% Ceramic Lagging.
- High performance 96% Aluminium Oxide tiles with high levels of hardness, abrasion resistance and crack resistance. This greatly reduces the likelihood of tile cracking when carry back is present.
- Modified dimple profile to increase durability and to also be kinder to the bottom cover of the belt. Dimple diameter has been increased and profile has been tapered to increase dimple strength. Addition of radii to all corners has been done to increase resistance to cracking and breakage of the dimples.
-
Tile thickness increased to 8mm + 1.5mm dimples to improve the resistance to cracking. Flex crack resistance results:
- Standard 4mm thick body tile 2-3,000N
- Extreme 8mm thick body tile > 10,000N - The increase in bonded surface area of the Extreme tile results in the tile pull out force doubling, when compared to the standard tile.
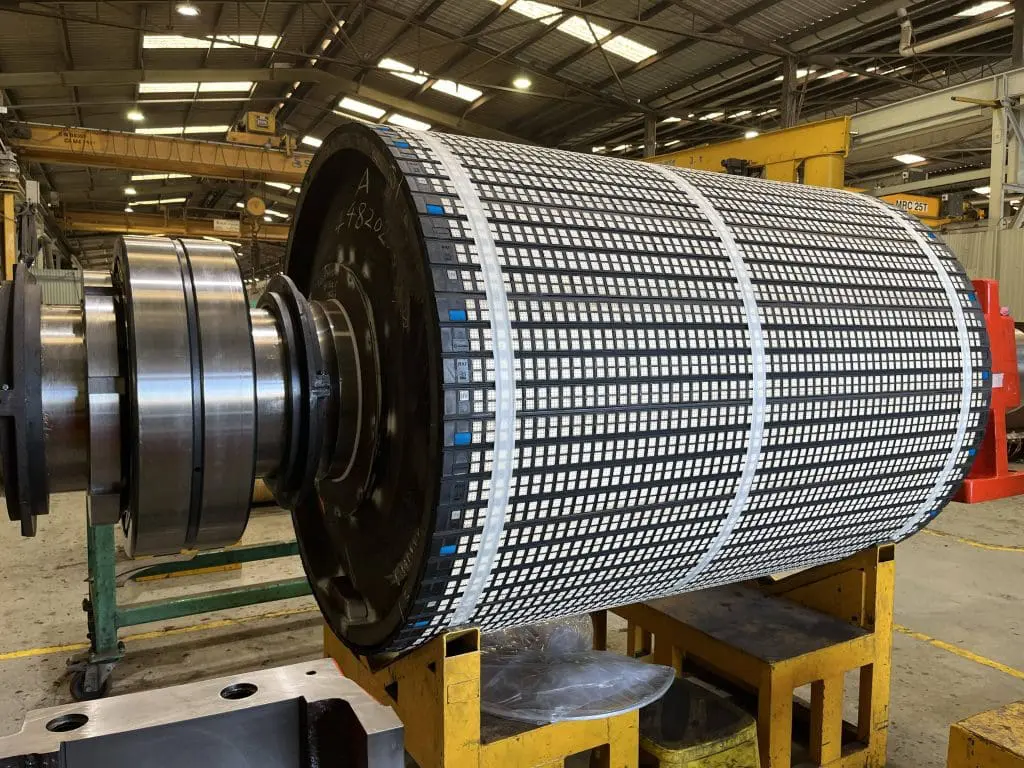
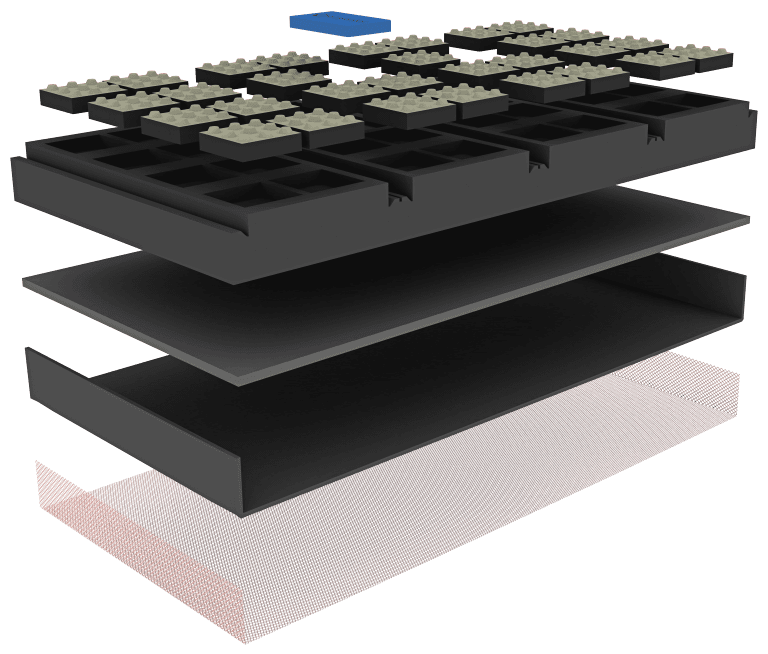
Coloured Logo
Premium finish
Elastotec 100% rubber tear
Edge sipe
3 cutting location sipe
CN buffed adhesion layer
Uncured bonding layer
Plastic release liner
Design
Tile design for the Elastotec Extreme 42% Ceramic Lagging has been modified to increase the resistance to tile cracking and dimple loss.
Rubber Specifications
NAT | |
---|---|
Polymer | SBR |
Tensile strength (Mpa) min ISO37 | 17.0 |
% Elongation min ISO37 | 550% |
Hardness (shore A) ISO868 | 60+/-5 |
Abrasion resistance max vol. loss ISO 4649 method A (non-rotating) | 80mm3 |
Heat ageing (Property change after 70°C 168hs) | Tensile strength +2% Elongation -20% Hardness 7 points |
Continuous operating temperature | -40/+70°C |
- Tile body thickness has been increased to 8mm to increase resistance to cracking.
THE CRACKING FORCE (N) | |
---|---|
Standard 20 x 20 x 4mm tile (+1mm dimple) | 2000 - 3000 |
Extreme 20 x 20 x 8mm tile (+1.5mm dimple) | > 10,000 |
TILE PULL OUT FORCE (KGF) | |
---|---|
Standard 20 x 20 x 4mm tile (+1mm dimple) | 200 - 220 |
Extreme 20 x 20 x 8mm tile (+1.5mm dimple) | 400 - 440 |
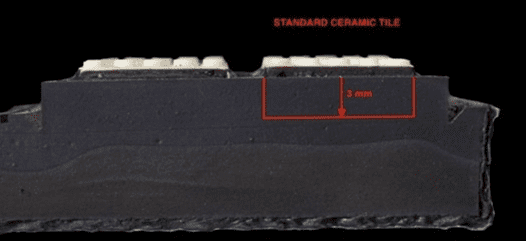
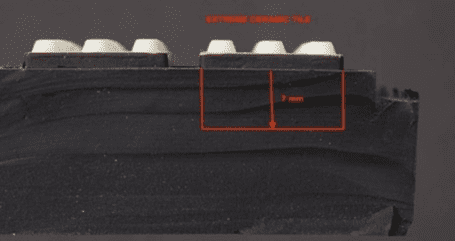
FLEX CRACK TESTING OF CERAMIC TILES
- Dimple diameter has been increased and the profile has been tapered to increase resistance to breakage (see photo above).
- Radii have been added to all corners to resist breakage.
- Larger tile increases the bonded surface area from 7.2cm2 for the “Standard” ceramic tile to 9.6cm2 for the “Extreme” ceramic tile. The resulting tile pull out force increases as a result.
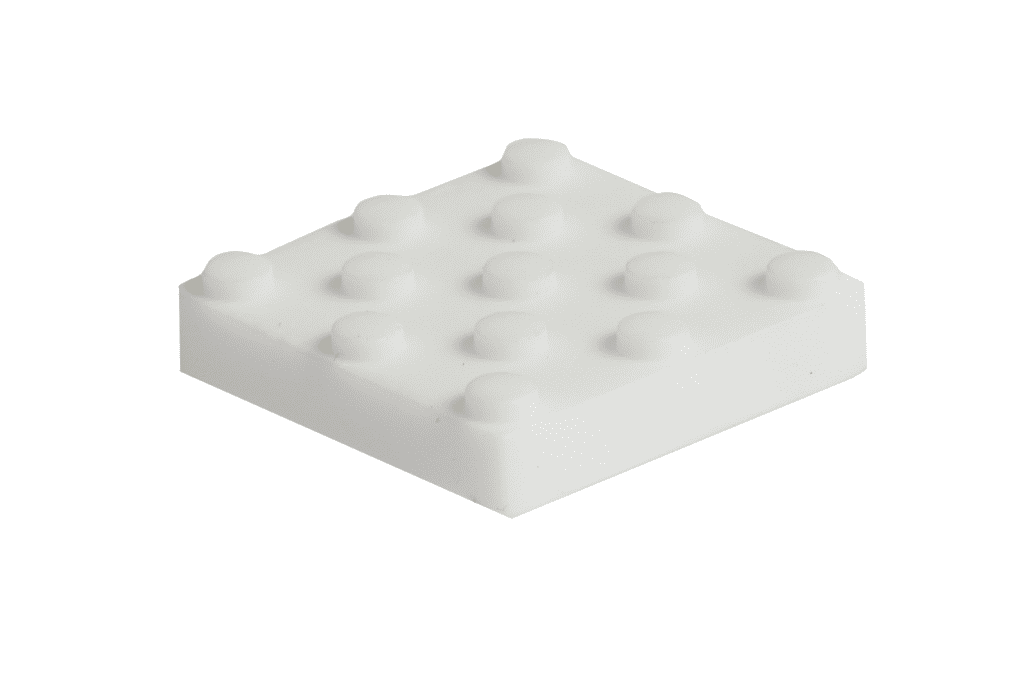

Ceramic Specifications
Typical values
Aluminium oxide | 96% |
Specific gravity g/cm3 | 3.7 |
Vickers hardness HV (10) | 1000 plus |
Flexural strength (Mpa) | 300 |
Compressive strength (Mpa) | 1800 |
Fracture Toughness (Mpa m1/2) | 3.5 |
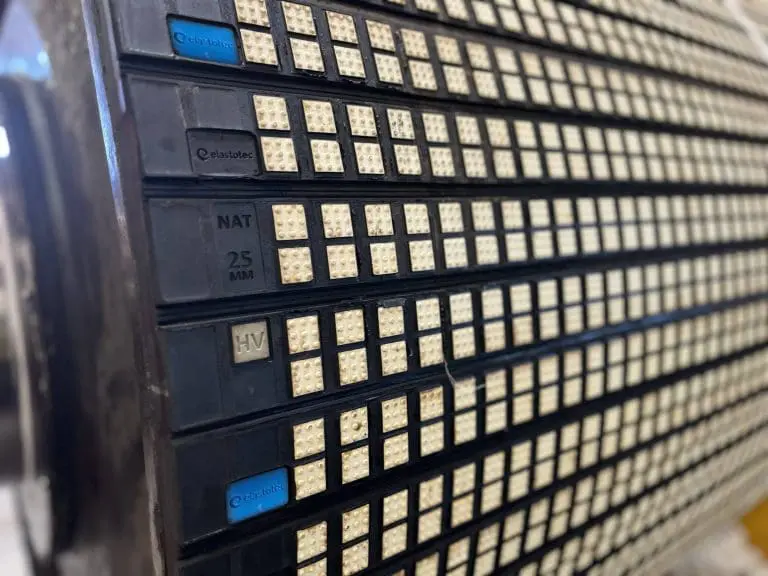
Lagging Specifications – Extreme 42% Ceramic Lagging
COLD BONDED - NAT
Product | Code | Width | Thickness | Length | WEIGHT/lm |
---|---|---|---|---|---|
Extreme 42% Ceramic Lagging 20mm | ELA-DRC42-N60-20E | 250mm-252mm | 19mm-20mm | 38.8m | 7.20kg |
Extreme 42% Ceramic Lagging 25mm | ELA-DRC80-N60-25E | 250mm-252mm | 24mm-25mm | 20.0m | 7.60kg |
COLD BONDED - FRAS
Product | Code | Width | Thickness | Length | WEIGHT/lm |
---|---|---|---|---|---|
Extreme 42% Ceramic Lagging 20mm | ELA-DRC42-F-20E | 250mm-252mm | 19mm-20mm | 38.8m | 7.40kg |
Extreme 42% Ceramic Lagging 25mm | ELA-DRC80-F-25E | 250mm-252mm | 24mm-25mm | 20.0m | 7.80kg |
HOT VULCANISED - NAT
Product | Code | Width | Thickness | Length | WEIGHT/lm |
---|---|---|---|---|---|
Extreme 42% Ceramic Lagging 20mm | ELA-DRC42-N60-20EV | 251mm-255mm | 20mm-21.2mm | 9.7m | 7.40kg |
Extreme 42% Ceramic Lagging 25mm | ELA-DRC42-N60-25EV | 251mm-255mm | 25mm-26.2mm | 9.7m | 7.80kg |
HOT VULCANISED - FRAS
Product | Code | Width | Thickness | Length | WEIGHT/lm |
---|---|---|---|---|---|
Extreme 42% Ceramic Lagging 20mm | ELA-DRC42-F-20EV | 251mm-255mm | 20mm-21.2mm | 9.7m | 7.60kg |
Extreme 42% Ceramic Lagging 25mm | ELA-DRC42-F-25EV | 251mm-255mm | 25mm-26.2mm | 9.7m | 7.80kg |
Product code for different strip lengths: Add 5-digit number indicating ceramic length in mm.
Strip: 25mm thick hot vulcanising, Nat 1.8m ceramic length product code: ELA-DRC80-N60-20EV-SQ-01800
Thickness variation (all strips/pulley) +/-0.5mm
NAT AND FRAS
Elastotec Rubber and Ceramic Laggings are available in both SBR (NAT) and FRAS approved compounds. FRAS lagging is MDG3608 certified and MSHA accepted, made of a fire resistant and antistatic compound that is primarily used in applications where there is a risk of fire and/or explosion as a safety precaution. These applications include underground coal mines, power stations, grain handling facilities and sugar terminals. Elastotec uses blue coloured inserts to identify SBR (NAT) rubber products and red coloured inserts to identify FRAS rubber products.
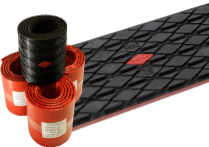
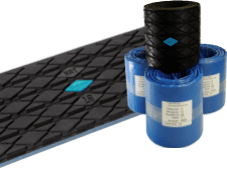
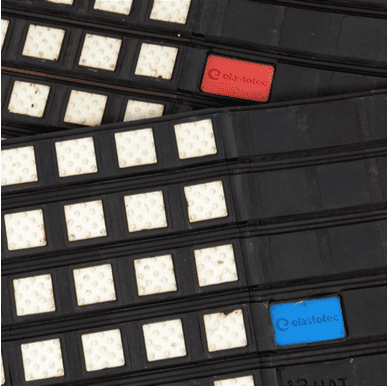
Elastotec lagging can be applied to pulleys by cold bonding or by hot vulcanisation.
ELASTOTEC COLD BONDING
RUBBER LAGGING
Elastotec Cold Bonding Rubber Lagging has the CN buffed bonding layer packed in plastic to protect and keep it fresh and free from contamination until application to the pulley.
A rubber tear bond is achieved by using Elastotec Metal Primer 2205 and Elastotec Cold Bonding Adhesive to chemically interlock with the CN bonding layer, making a strong interface between the layers.
An Elastotec approved applicator using the Elastotec application procedure will achieve reliable adhesion levels that exceed the 9 N/mm industry standard and are typically at 12 N/mm.
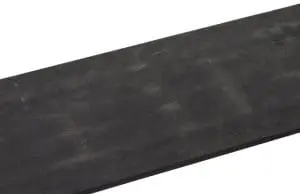
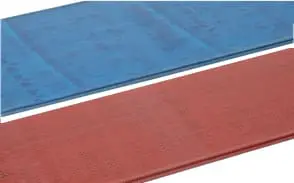
ELASTOTEC HOT VULCANISING RUBBER LAGGING
Elastotec Hot Vulcanising Rubber Lagging has a 1.2mm thick uncured rubber layer applied to the back and sides of the lagging.
Hot Vulcanising Lagging is supplied packed in plastic to protect and keep the uncured bonding layer fresh and free from contamination until application to the pulley.
Application by a trained Elastotec approved applicator using the Elastotec application procedures will guarantee a 100% rubber tear bond between the lagging and the pulley shell with typical adhesion values exceeding 20 N/mm.
How to store lagging:
- Stock usage based on a first-in first-out method (FIFO).
- The storage room for lagging must be cool, dry and dust-free.
- Avoid storage places near sources of ozone generating equipment.
- Do not store outside.
- Avoid storage in direct sunlight and strong artificial light as UV light can damage the products and may lead to a premature ageing.
- Under no circumstances should fuels, lubricants, acids, disinfectants, solvents or other chemicals be stored in the same storage area.
- Keep the storage place clean. Protect the material from dust, water etc. with suitable coverings.
- Allow 24 hours before use when lagging is removed from cold storage.
Shelf life:
COLD BONDING LAGGING AND WEAR PANELS
- Stored <25°C 3 years shelf life
- Light buffing of bonding surfaces is recommended if over 4 months from production date
HOT VULCANISED LAGGING AND WEAR PANELS
- <7°C and away from UV and ozone generating equipment 12 months. Products stored for longer than 6 months will need to be re-tested for adhesion before being used, and the recommended shelf life is 12 months.
ADHESIVES AND PRIMERS
- Store in flammable goods cabinet
- Stored <25°C
- Shelf life:
- Primers 2 years
- Cold bonding adhesive 2 years
- Hot vulcanising adhesive 12 months
- Direct bond adhesive 2 years
Products stored under the above conditions for longer periods of time than recommended need to be re-tested for adhesion before being used. If any doubts on storage recommendations, contact Elastotec.