Essential lagging specifications are necessary to comprehend the factors involved in selecting premium pulley lagging.
These specifications are sought after while drafting tender documents to ensure premium quality lagging selection. These represent the fundamental lagging requirements or the baseline criteria that must be taken into account before finalising a purchase choice.
At the bottom of the page is the information as a download package for easy reference.
- Lagging for both Drive and Non-Drive pulleys needs to be selected via an engineering analysis.
- Lagging engineering analysis must provide justification that the lagging will prevent or minimise slip, and have sufficient fatigue resistance to provide the required service life.
- *** Performance Critical specifications relate directly to the performance and life expectancy of the lagging. These should be included within every specification
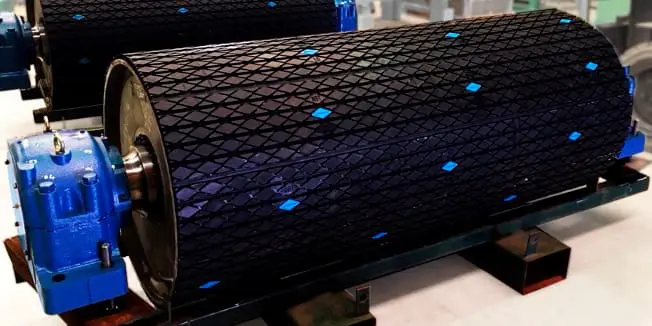
Rubber Specifications | NATURAL/SBR | FRAS | OIL RESISTANT | EXTREME CERAMIC | NOTE | PERFORMANCE CRITICAL |
---|---|---|---|---|---|---|
Tensile strength (MPa) ISO37 (min) | > 20 | > 18 | > 17 | > 20 | ||
Elongation ISO37 (min) | > 550% | > 500% | > 500% | > 550% | ||
Hardness (shore A) ISO868 | 65+/-5 | 65+/-5 | 65+/-5 | 60+/-5 | ||
Abrasion resistance max vol. loss ISO 4649 method A (non-rotating) | < 70mm3 | < 150mm3 | < 140mm3 | < 80mm3 | Abrasion resistance has a direct correlation to wear. The lower the number, the longer the wear service life | Yes |
Heat ageing Maximum Change (70hrs @ 70C) | Tensile strength +3% Elongation -15% Hardness +2 points | Tensile strength +3% Elongation -6% Hardness +3 points | Tensile strength +5% Elongation -1% Hardness +3 points | Tensile strength +2% Elongation -20% Hardness +7 points | Heat ageing determines the laggings ability to retain original physical properties | |
Oil resistance | NA | NA | Oil resistance as per table below | NA | Yes - in applications where oily materials are being conveyed | |
Continuous operating temperature range | -40/+70°C | -40/+70°C | -40/+70°C | -40/+70°C | ||
FRAS (Fire Resistant and Anti Static) MDG3608 and MSHA Certification | NA | Passed & Certificates provided | NA | NA | Yes - in applications where FRAS products are a legislative requirement | |
Lagging Application Method | Hot Vulcanised | Hot Vulcanised | Hot Vulcanised | Hot Vulcanised Only (No Cold Bond option) | Mandatory requirement for maximum service life. HV eliminates laggigng debonding from pulley shell, edge lifting, and joint separation. | Yes |
Lagging Manufacturing process | Press moulded | Press moulded | Press moulded | Press moulded | Eliminates lagging internal delamination | |
Application Procedure and Testing | Lagging Manufacturer to provide a Lagging Application Procedure which includes a QA Checklist and adhesion test for each pulley | Lagging Manufacturer to provide a Lagging Application Procedure which includes a QA Checklist and adhesion test for each pulley | Lagging Manufacturer to provide a Lagging Application Procedure which includes a QA Checklist and adhesion test for each pulley | Lagging Manufacturer to provide a Lagging Application Procedure which includes a QA Checklist and adhesion test for each pulley | Yes | |
Lagging Adhesion to Steel | >20N/mm + 100% rubber tear | >20N/mm + 100% rubber tear | >20N/mm + 100% rubber tear | >20N/mm + 100% rubber tear | Adhesion test is mandatory for each pulley. Refer to Hot Vulcanised Lagging Test Procedure for the process to follow. | Yes |
Lagging Adhesion to Steel Guarantee | No debonding from the pulley shell for the service life of the pulley | No debonding from the pulley shell for the service life of the pulley | No debonding from the pulley shell for the service life of the pulley | No debonding from the pulley shell for the service life of the pulley | Yes |
OIL TYPE | OIL RESISTANT |
---|---|
Volume Swell% | |
Corn Oil | 10-20 |
Cotton Seed Oil | 10-20 |
Linseed Oil | 5-10 |
Olive Oil | 5-10 |
Peanut Oil | 10-20 |
Pinene | 10-20 |
Pine Oil | >100 |
Rapeseed Oil | 5-10 |
Soybean Oil | 5-10 |
Terpineol | >100 |
Tung Oil | 5-10 |
Terpentine | >100 |
Vegetable Oil | 10-20 |
White Pine Oil | >100 |
White Oil | 5-10 |
Wood Oil | 5-10 |
Asphalt | 5-10 |
* Elastotec Oil Resistant lagging is not recommended for use with oils where volume swell exceeds 20%.
- Lagging for both Drive and Non-Drive pulleys needs to be selected via an engineering analysis.
- Lagging engineering analysis must provide justification that the lagging will prevent or minimise slip, and have sufficient fatigue resistance to provide the required service life.
- *** Performance Critical specifications relate directly to the performance and life expectancy of the lagging. These should be included within every specification.
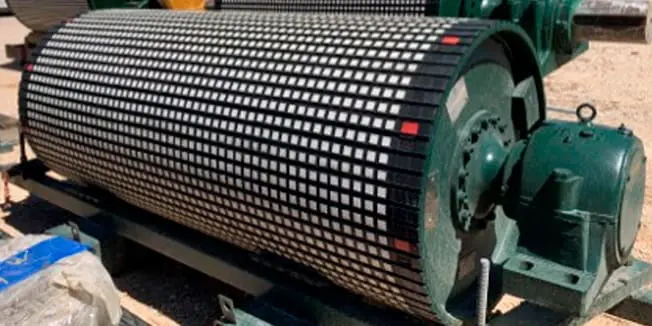
Rubber Specifications | NATURAL/SBR | FRAS | OIL RESISTANT | EXTREME CERAMIC | NOTE | PERFORMANCE CRITICAL |
---|---|---|---|---|---|---|
Tensile strength (MPa) ISO37 (min) | > 20 | > 18 | > 17 | > 20 | ||
Elongation ISO37 (min) | > 550% | > 500% | > 500% | > 550% | ||
Hardness (shore A) ISO868 | 65+/-5 | 65+/-5 | 65+/-5 | 60+/-5 | ||
Abrasion resistance max vol. loss ISO 4649 method A (non-rotating) | < 70mm3 | < 150mm3 | < 140mm3 | < 80mm3 | Abrasion resistance has a direct correlation to wear. The lower the number, the longer the wear service life | Yes |
Oil resistance | NA | NA | Oil resistance as per table below | NA | Yes - in applications where oily materials are being conveyed | |
Continuous operating temperature range | -40/+70°C | -40/+70°C | -40/+70°C | -40/+70°C | ||
FRAS (Fire Resistant and Anti Static) MDG3608 and MSHA Certification | NA | Passed & Certificates provided | NA | NA | Yes - in applications where FRAS products are a legislative requirement | |
Lagging Application Method | Hot Vulcanised | Hot Vulcanised | Hot Vulcanised | Hot Vulcanised Only (No Cold Bond option) | Mandatory requirement for maximum service life. HV eliminates laggigng debonding from pulley shell, edge lifting, and joint separation. | Yes |
Lagging Manufacturing process | Press moulded | Press moulded | Press moulded | Press moulded | Eliminates lagging internal delamination | |
Application Procedure and Testing | Lagging Manufacturer to provide a Lagging Application Procedure which includes a QA Checklist and adhesion test for each pulley | Lagging Manufacturer to provide a Lagging Application Procedure which includes a QA Checklist and adhesion test for each pulley | Lagging Manufacturer to provide a Lagging Application Procedure which includes a QA Checklist and adhesion test for each pulley | Lagging Manufacturer to provide a Lagging Application Procedure which includes a QA Checklist and adhesion test for each pulley | Yes | |
Lagging Adhesion to Steel | >20N/mm + 100% rubber tear | >20N/mm + 100% rubber tear | >20N/mm + 100% rubber tear | >20N/mm + 100% rubber tear | Adhesion test is mandatory for each pulley. Refer to Hot Vulcanised Lagging Test Procedure for the process to follow. | Yes |
Lagging Adhesion to Steel Guarantee | No debonding from the pulley shell for the service life of the pulley | No debonding from the pulley shell for the service life of the pulley | No debonding from the pulley shell for the service life of the pulley | No debonding from the pulley shell for the service life of the pulley | Yes |
Ceramic Specifications | NATURAL/SBR | FRAS | OIL RESISTANT | EXTREME CERAMIC | PERFORMANCE CRITICAL |
---|---|---|---|---|---|
Aluminium oxide | >95% | >95% | >95% | >95% | Yes |
Specific gravity g/cm3 | >3.7 | >3.7 | >3.7 | >3.7 | |
Vickers hardness HV (10) | >1000 | >1000 | >1000 | >1000 | Yes |
Fracture Toughness (Mpa m1/2) | >3.5 | >3.5 | >3.5 | >3.5 | Yes |
Tile Cracking Force (min) | >2000N | >2000N | >2000N | >10,000N | |
Tile Body Thickness Exc dimple (min) | 4mm | 4mm | 4mm | 8mm | |
Tile surfaces bonded to rubber | 5 sides of each tile | 5 sides of each tile | 5 sides of each tile | 5 sides of each tile | Yes |
Force to remove ceramic tile from rubber (min) | >200kg per tile and 100% rubber tear failure after a minimum of 12 months outdoor environmental exposure | >200kg per tile and 100% rubber tear failure after a minimum of 12 months outdoor exposure | >200kg per tile and 100% rubber tear failure | >400kg per tile and 100% rubber tear failure | Yes |
Ceramic Tile Adhesion Guarantee | No debonding from rubber for the service life of the lagging | No debonding from rubber for the service life of the lagging | No debonding from rubber for the service life of the lagging | No debonding from rubber for the service life of the lagging | Yes |
OIL TYPE | OIL RESISTANT |
---|---|
Volume Swell% | |
Corn Oil | 10-20 |
Cotton Seed Oil | 10-20 |
Linseed Oil | 5-10 |
Olive Oil | 5-10 |
Peanut Oil | 10-20 |
Pinene | 10-20 |
Pine Oil | >100 |
Rapeseed Oil | 5-10 |
Soybean Oil | 5-10 |
Terpineol | >100 |
Tung Oil | 5-10 |
Terpentine | >100 |
Vegetable Oil | 10-20 |
White Pine Oil | >100 |
White Oil | 5-10 |
Wood Oil | 5-10 |
Asphalt | 5-10 |
* Elastotec Oil Resistant lagging is not recommended for use with oils where volume swell exceeds 20%.
- Lagging for both Drive and Non-Drive pulleys needs to be selected via an engineering analysis.
- Lagging engineering analysis must provide justification that the lagging will prevent or minimise slip, and have sufficient fatigue resistance to provide the required service life.
- Due to the low coefficient of friction, polyurethane lagging should only be used on Non-Drive pulleys.
- *** Performance Critical specifications relate directly to the performance and life expectancy of the lagging. These should be included within every specification
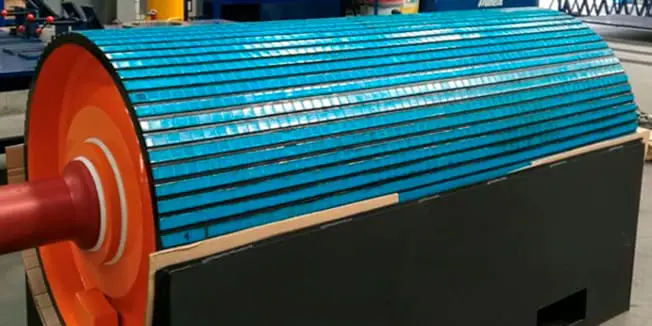
Polyurethane Specifications | NATURAL/SBR | NOTES | PERFORMANCE CRITICAL |
---|---|---|---|
Hardness (shore A) ASTM D2240 | 85 +/-5 | ||
Tensile Strength DIN53504 | > 40 Mpa | ||
Elongation at break ASTM D412 | > 500% | ||
Abrasion resistance max vol. loss DIN 53516 method A (non-rotating) | < 30 mm3 | Abrasion resistance has a direct correlation to wear. The lower the number, the longer the wear service life | Yes |
Continuous operating temperature range | -40/+70°C | ||
Recommended Lagging Application Method | Hot Vulcanised | Mandatory requirement for maximum service life. HV eliminates laggigng debonding from pulley shell, edge lifting, and joint separation. | Yes |
Lagging Manufacturing process | Press moulded | Eliminates lagging internal delamination | |
Application Procedure and Testing | QA Checklist and adhesion test for each pulley | Yes | |
Lagging Adhesion to Steel | >20N/mm + 100% rubber tear | Adhesion test is mandatory for each pulley. Refer to Hot Vulcanised Lagging Test Procedure for the process to follow. | Yes |
Lagging Adhesion to Steel Guarantee | No debonding from the pulley shell for the service life of the pulley | Yes |
- Lagging for both Drive and Non-Drive pulleys needs to be selected via an engineering analysis.
- Lagging engineering analysis must provide justification that the lagging will prevent or minimise slip, and have sufficient fatigue resistance to provide the required service life.
- *** Performance Critical specifications relate directly to the performance and life expectancy of the lagging. These should be included within every specification.
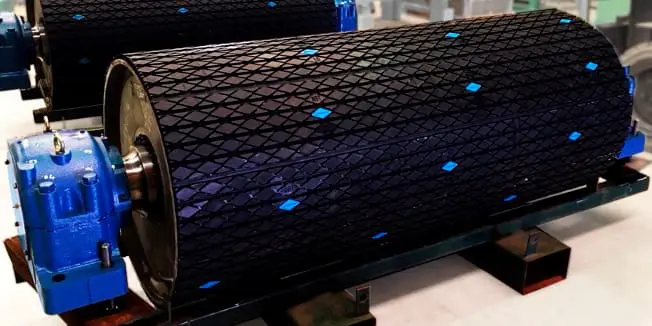
Rubber Specifications | NATURAL/SBR | FRAS | OIL RESISTANT | NOTE | PERFORMANCE CRITICAL |
---|---|---|---|---|---|
Tensile strength (MPa) ISO37 (min) | > 20 | > 18 | > 17 | ||
Elongation ISO37 (min) | > 550% | > 500% | > 500% | ||
Hardness (shore A) ISO868 | 65+/-5 | 65+/-5 | 65+/-5 | ||
Abrasion resistance max vol. loss ISO 4649 method A (non-rotating) | < 70mm3 | < 150mm3 | < 140mm3 | Abrasion resistance has a direct correlation to wear. The lower the number, the longer the wear service life | Yes |
Heat ageing Maximum Change (70hrs @ 70C) | Tensile strength +3% Elongation -15% Hardness +2 points | Tensile strength +3% Elongation -6% Hardness +3 points | Tensile strength +5% Elongation -1% Hardness +3 points | Heat ageing determines the laggings ability to retain original physical properties | |
Oil Resistance | NA | NA | Oil resistance as per table below | Yes - in applications where oily materials are being conveyed | |
Continuous operating temperature range | -40/+70°C | -40/+70°C | -40/+70°C | ||
Lagging Application Method | Cold Bond | Cold Bond | Cold Bond | Hot Vulcanised lagging provides much higher levels of adhesion and sealing compared to Cold Bond. Cold Bond application should only be used when Hot Vulcanising is not an option. | Yes |
Lagging Manufacturing process | Press moulded | Press moulded | Press moulded | Eliminates lagging internal delamination | |
Application Procedure and Testing | Lagging Manufacturer to provide a Lagging Application Procedure which includes a QA Checklist and adhesion test for each pulley | Lagging Manufacturer to provide a Lagging Application Procedure which includes a QA Checklist and adhesion test for each pulley | Lagging Manufacturer to provide a Lagging Application Procedure which includes a QA Checklist and adhesion test for each pulley | Yes | |
Lagging Adhesion to Steel | >12N/mm | >12N/mm | >12N/mm | Adhesion test is mandatory for each pulley. Refer to Cold Bond Lagging Test Procedure for the process to follow. | Yes |
OIL TYPE | OIL RESISTANT |
---|---|
Volume Swell% | |
Corn Oil | 10-20 |
Cotton Seed Oil | 10-20 |
Linseed Oil | 5-10 |
Olive Oil | 5-10 |
Peanut Oil | 10-20 |
Pinene | 10-20 |
Pine Oil | >100 |
Rapeseed Oil | 5-10 |
Soybean Oil | 5-10 |
Terpineol | >100 |
Tung Oil | 5-10 |
Terpentine | >100 |
Vegetable Oil | 10-20 |
White Pine Oil | >100 |
White Oil | 5-10 |
Wood Oil | 5-10 |
Asphalt | 5-10 |
* Elastotec Oil Resistant lagging is not recommended for use with oils where volume swell exceeds 20%.
- Lagging for both Drive and Non-Drive pulleys needs to be selected via an engineering analysis.
- Lagging engineering analysis must provide justification that the lagging will prevent or minimise slip, and have sufficient fatigue resistance to provide the required service life.
- *** Performance Critical specifications relate directly to the performance and life expectancy of the lagging. These should be included within every specification
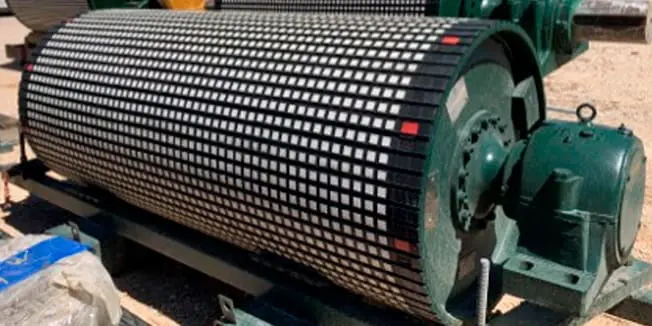
Rubber Specifications | NATURAL/SBR | FRAS | OIL RESISTANT | NOTE | PERFORMANCE CRITICAL |
---|---|---|---|---|---|
Tensile strength (MPa) ISO37 (min) | > 20 | > 18 | > 17 | ||
Elongation ISO37 (min) | > 550% | > 500% | > 500% | ||
Hardness (shore A) ISO868 | 65+/-5 | 65+/-5 | 65+/-5 | ||
Abrasion resistance max vol. loss ISO 4649 method A (non-rotating) | < 70mm3 | < 150mm3 | < 140mm3 | Abrasion resistance has a direct correlation to wear. The lower the number, the longer the wear service life | Yes |
Heat ageing Maximum Change (70hrs @ 70C) | Tensile strength +3% Elongation -15% Hardness +2 points | Tensile strength +3% Elongation -6% Hardness +3 points | Tensile strength +5% Elongation -1% Hardness +3 points | Heat ageing determines the laggings ability to retain original physical properties | |
Oil resistance | NA | NA | Oil resistance as per table below | Yes - in applications where oily materials are being conveyed | |
Continuous operating temperature range | -40/+70°C | -40/+70°C | -40/+70°C | ||
FRAS (Fire Resistant and Anti Static) MDG3608 and MSHA Certification | NA | Passed & Certificates provided | NA | Yes - in applications where FRAS products are a legislative requirement | |
Lagging Application Method | Cold Bond | Cold Bond | Cold Bond | Hot Vulcanised lagging provides much higher levels of adhesion and sealing compared to Cold Bond. Cold Bond application should only be used when Hot Vulcanising is not an option. | Yes |
Lagging Manufacturing process | Press moulded | Press moulded | Press moulded | Eliminates lagging internal delamination | |
Application Procedure and Testing | Lagging Manufacturer to provide a Lagging Application Procedure which includes a QA Checklist and adhesion test for each pulley | Lagging Manufacturer to provide a Lagging Application Procedure which includes a QA Checklist and adhesion test for each pulley | Lagging Manufacturer to provide a Lagging Application Procedure which includes a QA Checklist and adhesion test for each pulley | Yes | |
Lagging Adhesion to Steel | >12N/mm | >12N/mm | >12N/mm | Adhesion test is mandatory for each pulley. Refer to Cold Bond Lagging Test Procedure for the process to follow. | Yes |
Ceramic Specifications | NATURAL/SBR | FRAS | OIL RESISTANT | PERFORMANCE CRITICAL |
---|---|---|---|---|
Aluminium oxide | >95% | >95% | >95% | Yes |
Specific gravity g/cm3 | >3.7 | >3.7 | >3.7 | |
Vickers hardness HV (10) | >1000 | >1000 | >1000 | Yes |
Fracture Toughness (Mpa m1/2) | >3.5 | >3.5 | >3.5 | Yes |
Tile Cracking Force (min) | >2000N | >2000N | >2000N | |
Tile Body Thickness exc dimple (min) | 4mm | 4mm | 4mm | |
Tile surfaces bonded to rubber | 5 sides of each tile | 5 sides of each tile | 5 sides of each tile | Yes |
Force to remove ceramic tile from rubber (min) | >200kg per tile and 100% rubber tear failure after a minimum of 12 months outdoor environmental exposure | >200kg per tile and 100% rubber tear failure after a minimum of 12 months outdoor exposure | >200kg per tile and 100% rubber tear failure | Yes |
Ceramic Tile Adhesion Guarantee | No debonding from rubber for the service life of the lagging | No debonding from rubber for the service life of the lagging | No debonding from rubber for the service life of the lagging | Yes |
OIL TYPE | OIL RESISTANT |
---|---|
Volume Swell% | |
Corn Oil | 10-20 |
Cotton Seed Oil | 10-20 |
Linseed Oil | 5-10 |
Olive Oil | 5-10 |
Peanut Oil | 10-20 |
Pinene | 10-20 |
Pine Oil | >100 |
Rapeseed Oil | 5-10 |
Soybean Oil | 5-10 |
Terpineol | >100 |
Tung Oil | 5-10 |
Terpentine | >100 |
Vegetable Oil | 10-20 |
White Pine Oil | >100 |
White Oil | 5-10 |
Wood Oil | 5-10 |
Asphalt | 5-10 |
- Lagging for both Drive and Non-Drive pulleys needs to be selected via an engineering analysis.
- Lagging engineering analysis must provide justification that the lagging will prevent or minimise slip, and have sufficient fatigue resistance to provide the required service life.
- Due to the low coefficient of friction, polyurethane lagging should only be used on Non-Drive pulleys.
- *** Performance Critical specifications relate directly to the performance and life expectancy of the lagging. These should be included within every specification.
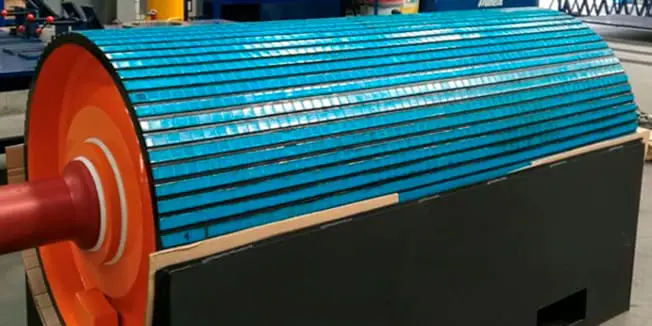
Polyurethane Specifications | NATURAL/SBR | NOTES | PERFORMANCE CRITICAL |
---|---|---|---|
Hardness (shore A) ASTM D2240 | 85 +/-5 | ||
Tensile Strength DIN53504 | > 40 Mpa | ||
Elongation at break ASTM D412 | > 500% | ||
Abrasion resistance max vol. loss DIN 53516 method A (non-rotating) | < 30mm3 | Abrasion resistance has a direct correlation to wear. The lower the number, the longer the wear service life | Yes |
Continuous operating temperature range | -40/+70°C | ||
Recommended Lagging Application Method | Cold Bond | Hot Vulcanised lagging provides much higher levels of adhesion and sealing compared to Cold Bond. Cold Bond application should only be used when Hot Vulcanising is not an option. | Yes |
Lagging Manufacturing process | Press moulded | Eliminates lagging internal delamination | |
Application Procedure and Testing | Lagging Manufacturer to provide a Lagging Application Procedure which includes a QA Checklist and adhesion test for each pulley | Yes | |
Lagging Adhesion to Steel | >12N/mm | Adhesion test is mandatory for each pulley. Refer to Cold Bond Lagging Test Procedure for the process to follow. | Yes |
- Lagging for both Drive and Non-Drive pulleys needs to be selected via an engineering analysis.
- Lagging engineering analysis must provide justification that the lagging will prevent or minimise slip, and have sufficient fatigue resistance to provide the required service life.
- *** Performance Critical specifications relate directly to the performance and life expectancy of the lagging. These should be included within every specification.
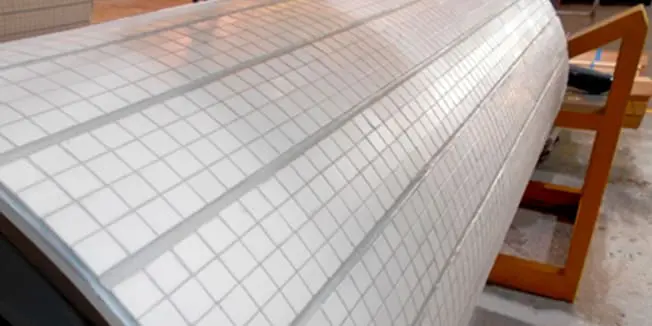
Direct Bond Ceramic Specifications | Non-Drive | Drive | Notes | PERFORMANCE CRITICAL |
---|---|---|---|---|
Aluminium oxide | 92% | 95% | Yes | |
Specific gravity g/cm3 | 3.6 | 3.7 | ||
Vickers hardness (HV10) | >1000 | >1200 | Yes | |
Fracture Toughness (Mpa m1/2) | 3-4 | 3-4 | Yes | |
Continuous operating temperature range | -20/+70°C | -20/+70°C | ||
Lagging Application Method | Direct Bond - Two Part Epoxy | Direct Bond - Two Part Epoxy | ||
Application Procedure and Testing | Lagging Manufacturer to provide a Lagging Application Procedure which includes a QA Checklist and adhesion test for each pulley | Lagging Manufacturer to provide a Lagging Application Procedure which includes a QA Checklist and adhesion test for each pulley | Yes | |
Lagging Adhesion to Steel (Shear test) | >20 Mpa | >20 Mpa | Adhesion test is mandatory for each pulley. Refer to Direct Bond Ceramic Lagging Test Procedure for the process to follow. | Yes |
Lagging Adhesion to Steel Guarantee | No debonding from the pulley shell for the service life of the pulley | No debonding from the pulley shell for the service life of the pulley | Yes |