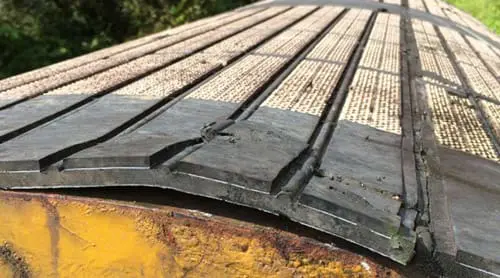
Spare Pulleys – Hot Vulcanised vs Cold Bonded Lagging
Spare pulleys are held so that in the event that an operational pulley requires replacement this can be done quickly and efficiently at the timing dictated by the mine maintenance personnel. The reason for changing a pulley broadly falls into two categories:
- Change out during a planned maintenance shut
- Emergency change out due to catastrophic pulley failure.
In both cases it is essential that the spare pulley is completely serviceable and ready to be used – any deterioration of the lagging in storage presents a major problem if the spare pulley cannot be put into service.
Spare pulleys are usually held on site where storage conditions can vary substantially from mine to mine. Spare pulleys should be packaged in such a way that the lagging is protected from direct exposure to sunlight as this will degrade any rubber portion of the lagging over time. Additionally packaging should be designed so that the pulley will not “sweat” due to moisture/condensation developing inside the packaging – this increases the risk of corrosion and lagging adhesion problems. Ideally spare pulleys are stored inside a warehouse in dry conditions but this is not always possible.
A major QLD coal terminal with typical service life for their operational pulleys of 5-10 years reported spending more of their maintenance budget on spare pulleys than on the operational pulleys due to the deterioration of the spare pulleys during the typical storage times of 5 -10 years. Replacement of the cold bonded lagging on the spare pulleys was a significant part of this cost.
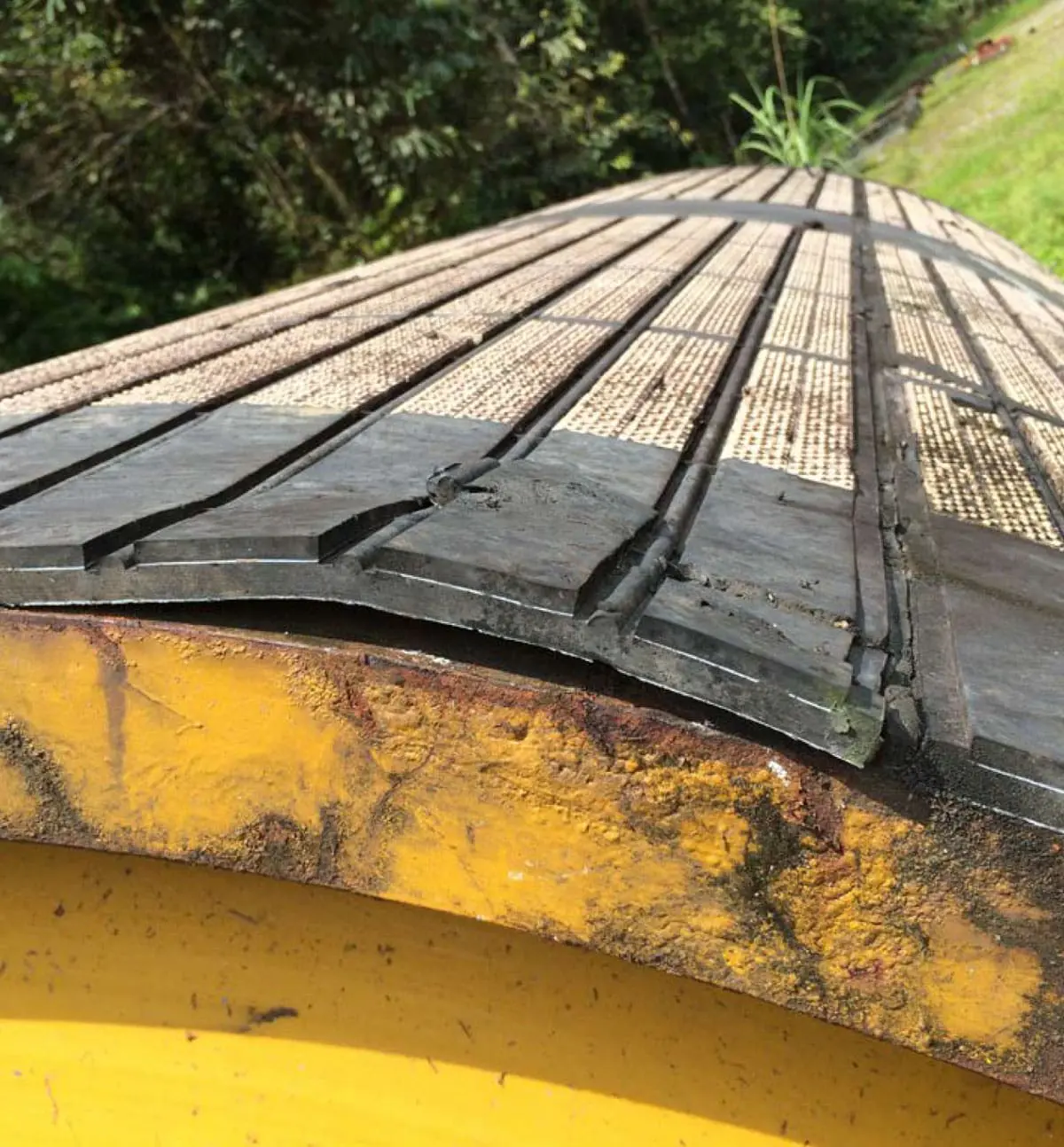
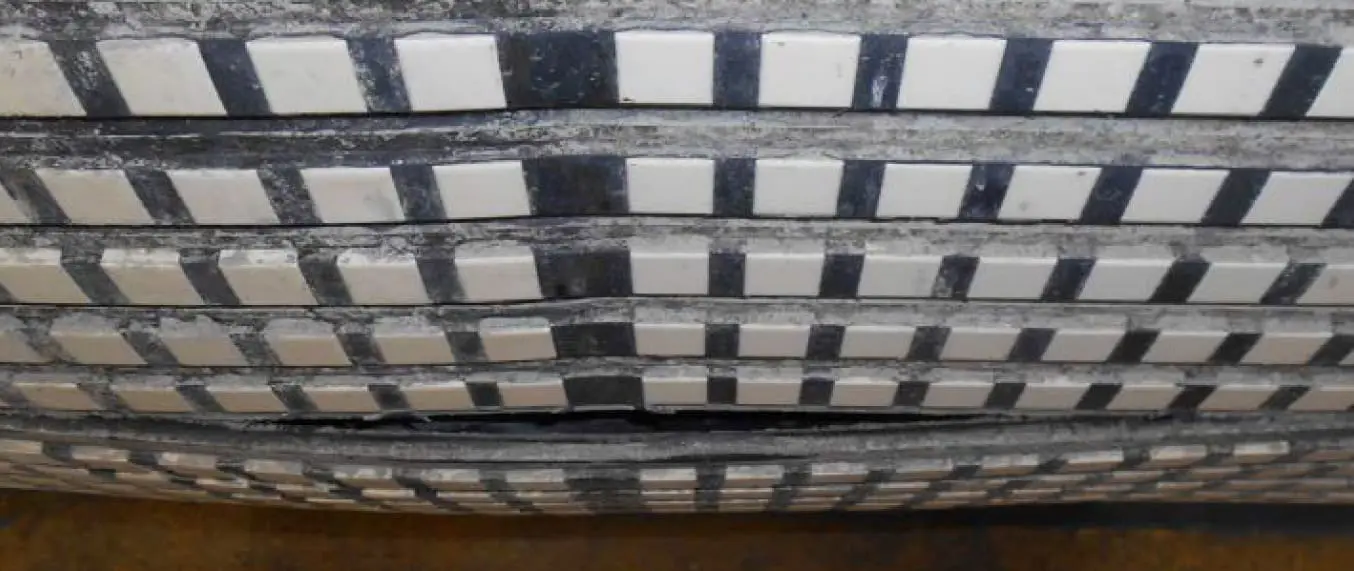
- Lifting of the lagging at the edges of the pulley
- Lifting of the lagging along the joint between two strips
- Opening up of the joint between two strips (this allows water to penetrate the lagging and start corroding the pulley shell).
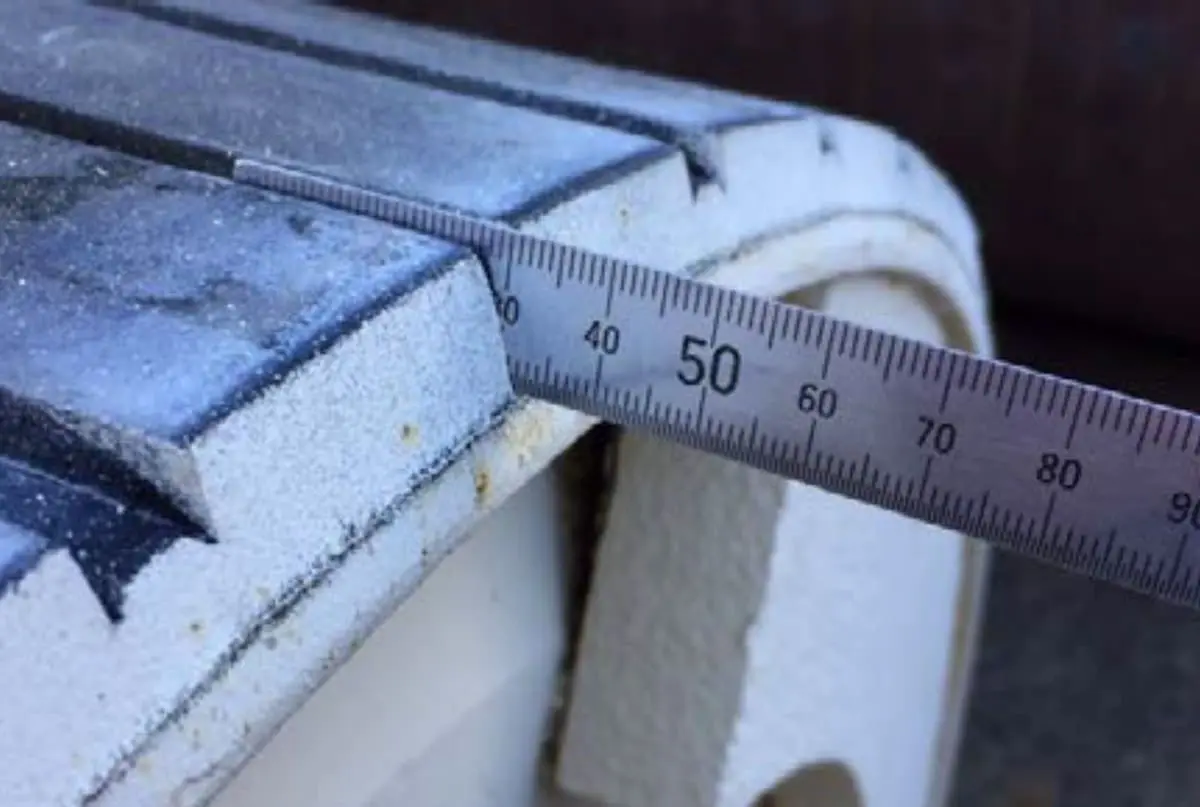
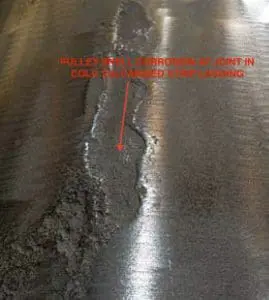
Hot vulcanised lagging offers significant advantages over cold bonded lagging when pulleys may be held in storage for extended periods and in less than ideal conditions. The advantages of hot vulcanised lagging relate directly to the much better adhesion between the lagging and the pulley shell (100% rubber tear adhesion is the standard) and also to the elimination of any joins between the lagging strips. The following photos show how hot vulcanised lagging eliminates the problems of lagging lifting at the pulley edge and of separation of the lagging along the joints between strips.
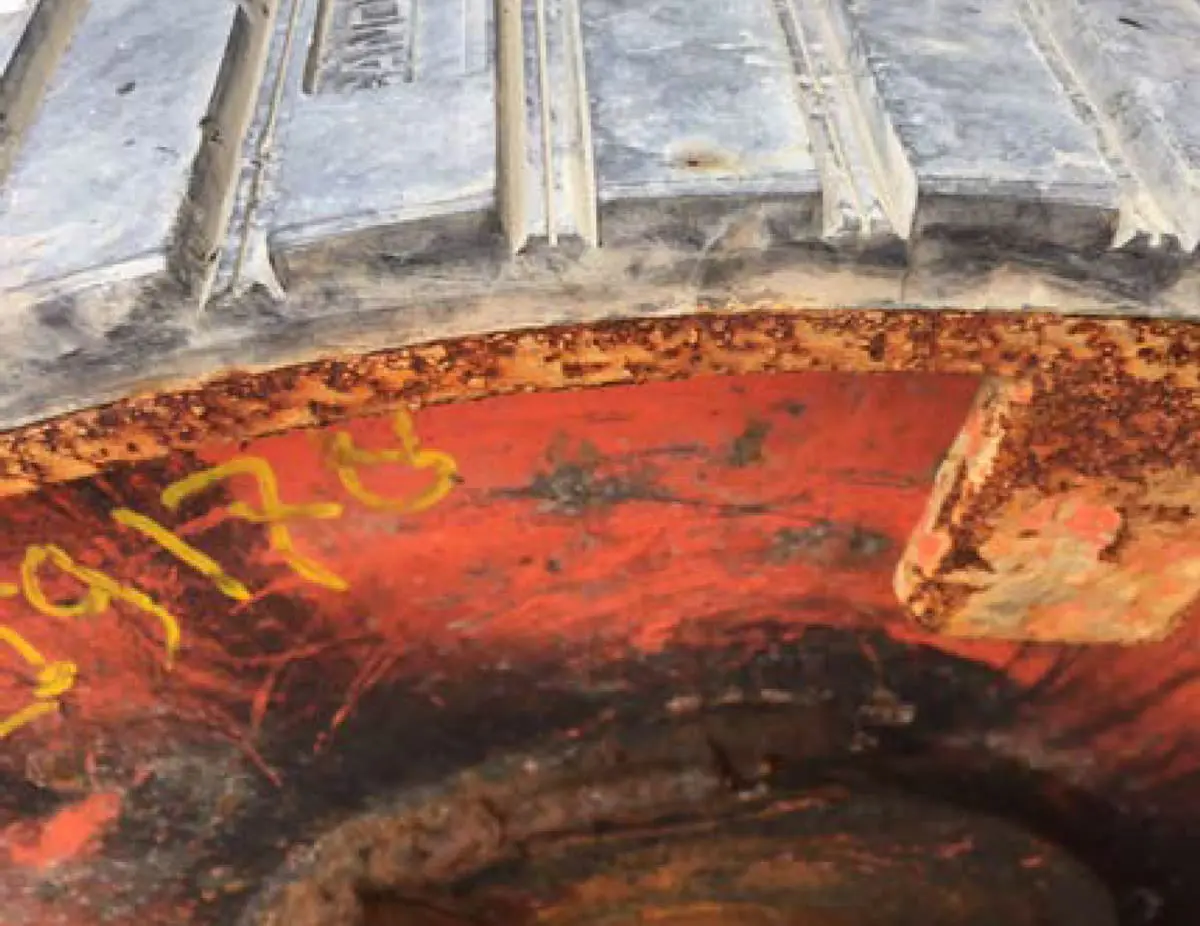
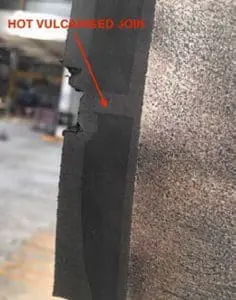
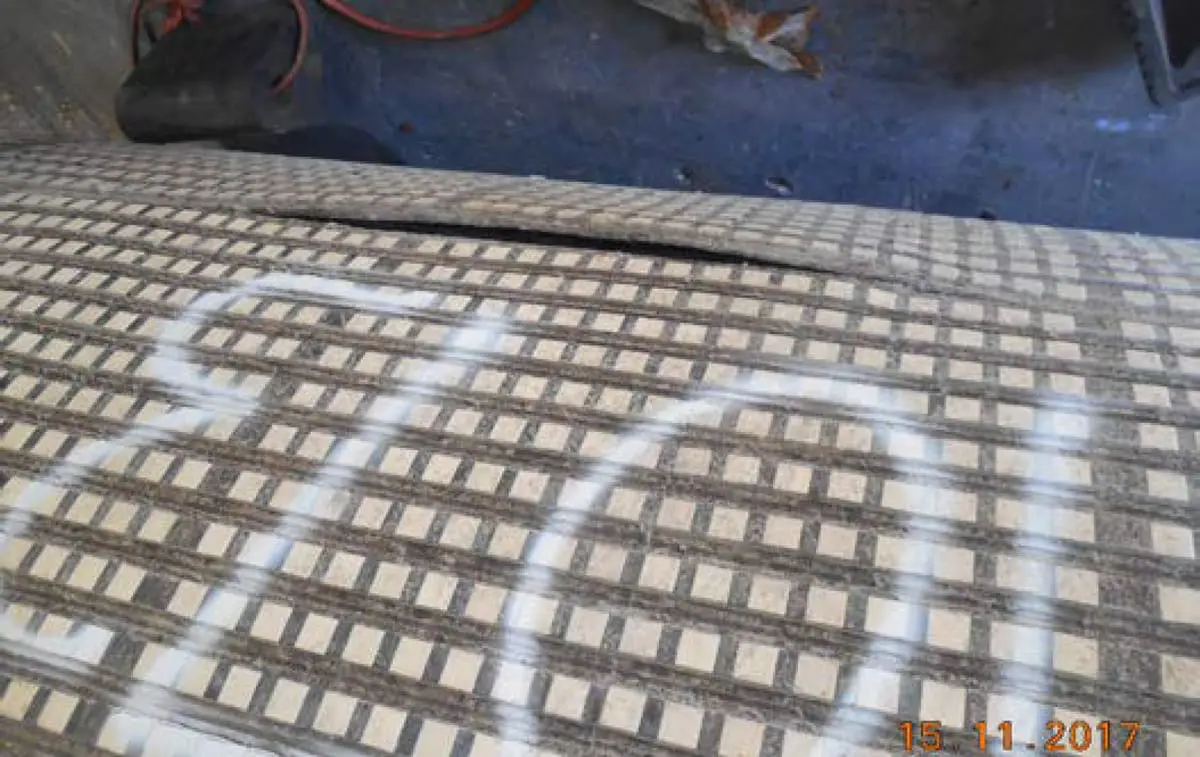

In summary hot vulcanised lagging offers increased certainty to maintenance personel that spare pulleys held in storage for extended periods will have the lagging ready for operation when required because the risk of the lagging debonding or opening up along the joins between strips has been eliminated.
Large Gold Mine in Australia – increased service life of pulleys with Elastotec/PROK HVCL
One of the largest gold mines in Australia, located in southeast of Perth, produces around 750,000 o
T&T Perú 2023
Thank you to the Peruvian mining sector. Thank you for the space to discuss your challenges. Thank y
Prevention of blisters in steam heated autoclaves
This technical bulletin will outline the causes of blister formation and will detail a series of sim